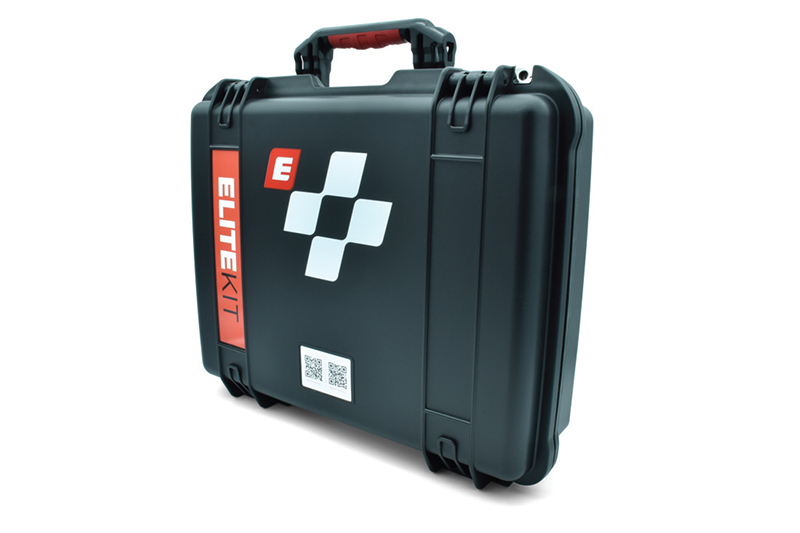
Turn windscreen chips into an opportunity instead of a disappointment. Esprit explains.
If you’re regularly carrying out MOTs, your heart may sink when a customer comes in with a cracked windscreen. You know that you’re going to have to tell them that the car will fail the MOT, or they’re going to have to fork out for a windscreen replacement. You might be confident carrying out chip repairs, but a crack is beyond what a repair kit can deal with, right? Wrong!
Most windscreen repair kits can’t repair cracks, and many repairers think that crack repair is beyond their capabilities, but we spoke to Victoria Evans from Esprit Windscreen Repair Equipment about how the Esprit kit can repair cracks as well as chips, and how they’re confident that any repairer can perfect the art of the crack repair. She told us “when we first designed the kit, we specifically made the lamp long enough to repair cracks up to 300mm in length because lots of our customers like to carry out crack repair as well as chip repair. When we started working on the larger bus and coach screens, they often had cracks so it was one of the key objectives of the kit that cracks could also be repaired. We actually considered making a smaller lamp a few years ago, but we decided that as we were one of the few kits on the market with the capability for crack repair, we would keep the existing lamp which can be used for chips and cracks.”
She went on to say “crack repair isn’t necessarily any more difficult than chip repair and with today’s screens often needing ADAS recalibration after a replacement, it’s often quicker to repair a crack, and certainly much cheaper for the customer. There is a different technique to repairing cracks, but they repair very well and can save your customer a lot of time and money. The full details of how to repair cracks is shown in our free training video which is on our website, and if you have any issues, you can pick up the phone and speak to our head of technical and training, Dean Proctor, who can address any issues you have. We also offer crack repair with our OEM training as part of the full training course. If you’re new to windscreen repair, or even if you’re experienced but feel that you could use some refresher training, we offer this both in Staffordshire, or we can come to your premises.”
Accredited choice
Victoria went on to say “when we received TUV accreditation last year, we specifically wanted crack repairs to be included in this. We know that a lot of other repair kits on the market don’t recommend repairing cracks, but we firmly believe that there is no difference between a crack and a chip, and if you follow the crack repair process properly, you’ll get a great result.”
So what should you be talking to your customers about if they come in with a cracked screen? Victoria told us “take a look at the windscreen – if the crack is 300mm or below, and isn’t in front of any ADAS cameras, then you’re good to repair. You can talk to your customer about how much cheaper and quicker repair is than replacement, and also that a repaired windscreen will pass the MOT while a cracked one is a fail. It’s also a great extra source of income for your business. You can charge a little more for crack repair, because it is a little more specialised, but the consumables used are the same as those used in chip repair, so your profit margin is great.”