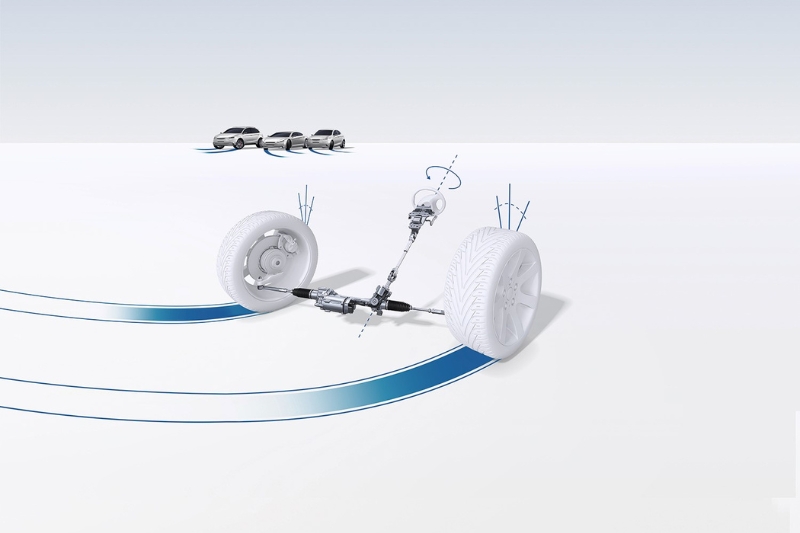
Will we soon have to say goodbye to the trusty steering wheel? As automation continues to focus the attention of vehicle manufacturers’ research departments, Bosch provides garage owners with a beginner’s guide to the technology allowing the radical re-invention of the (steering) wheel…
Petrol, diesel, hybrid, electric or gas powertrains – in order to meet as many customer demands as possible, most vehicle manufacturers launch their vehicles with a wide range of different powertrains. This large variety of drive concepts requires different versions of numerous vehicle components. This is where electric power steering plays to its strengths. In general, the system is powered by the on-board power supply. EPS systems can thus be used to equip vehicles featuring different powertrains and drive concepts. Additional advantages of EPS compared to hydraulic power steering systems are a reduction of both fuel consumption and CO₂ emissions, the possible integration into driver assistance systems – up to automated driving – as well as the possibility to select different steering modes. For these reasons, most of the recently registered cars are equipped with this system. Modern EPS systems even allow for connectivity via over-the-air technology. By now, Bosch EPS versions steer all types of vehicles reaching from compact to middle-class cars, sports cars and through to light commercial vehicles.
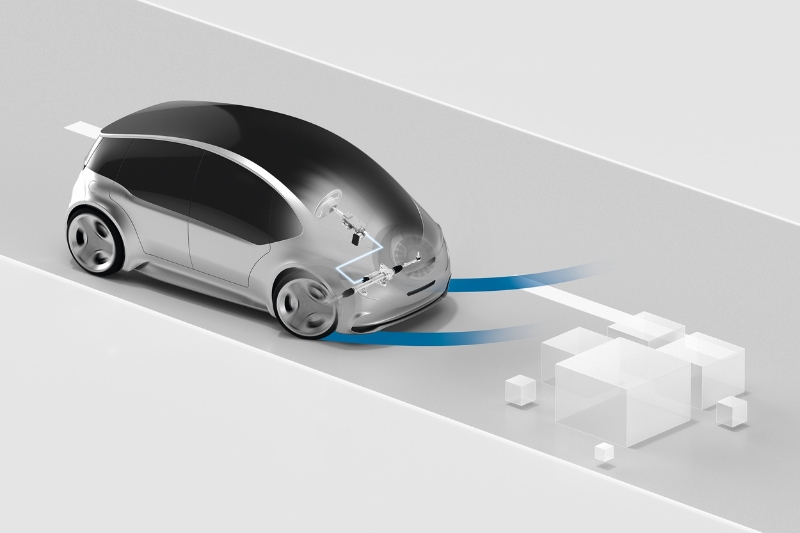
Key role in automated driving
EPS systems are a key technology for assisted and automated driving. They control and assist vehicle steering systems by means of an electromotor combined with a control unit for optimum steering behaviour and a great feeling when steering. By now, the electronic interface already allows Bosch electric steering systems to be used for automated driving concepts up to SAE level 4. Besides sophisticated software and connectivity of different vehicle components such as powertrain, braking and steering systems, the redundancy of safety-relevant features is a prerequisite for high levels of automation. Systems are known as redundant, if they are doubled for safety reasons.

EPS system as fail-save steering system
As all other electric steering systems, EPS systems with fail-operational functions are equipped with a torque sensor detecting the steering signal and sending it to the control unit calculating the optimum steering support. The required steering force is provided by the electromotor. This doesn’t just make driving much more comfortable. At this fail-operational version, power supply, electronic circuits, the control unit and the dividing machines within the servo unit are doubled. If one of the components fails, the other one continues operating the respective function. Even in case of a defect, at least 50 percent of the steering support remain. Besides steering systems, fail-safe Bosch systems are also used for braking systems, environment sensors, control units and the on-board power supply.
A look into the future: steer-by-wire
As automated driving functions become increasingly common, the demands placed on automotive technologies increase as well. Vehicle weight is meant to reduce whereas safety and comfort must increase – and so do personalisation and customisation possibilities. So-called steer-by-wire systems help starting into a new era of automotive technologies. As these systems are designed for both manual and automated driving, the steering wheel is not mechanically linked to the steered wheels. The elimination of the mechanical connection between the steering wheel actuator and the steering rack actuator provides additional options concerning the interior vehicle cabin design and the realisation of previously impossible functions. In future, the steering wheel could, for instance, be positioned individually for the driver during automated driving, or – in the case of highly automated vehicles – could be temporarily stowed away completely. Several vehicle manufacturers have already announced the market launch of such systems. The first vehicles equipped with steer-by-wire solutions will be launched throughout the upcoming years. This will gradually also create the corresponding demands on the aftermarket. Bosch thus also pays attention to ensuring a reliable supply of high-quality spare parts for workshops – right from the development stage.
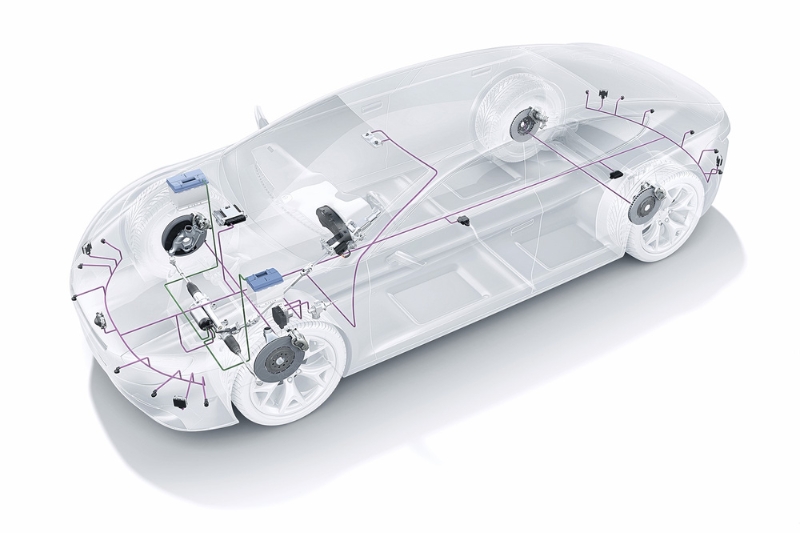
SAE Levels of Driving Automation
Level 0 – The driver is driving the vehicle, with only safety features such as automatic emergency braking, blind spot warning and lane departure warning active.
Level 1 – The driver is driving the vehicle, with features providing steering or brake/acceleration support such as lane centering or adaptive cruise control.
Level 2 – The driver is driving the vehicle, with recourse to both sets of features from Level 1
Level 3 – The driver is no longer driving the vehicle, unless requested by the car. The relevant features can drive the car under limited conditions and will not operate unless those conditions are met.
Level 4 – The driver is no longer driving the vehicle and will not be required to take over. Like Level 3, however, the features require certain conditions and will not drive unless those conditions are met. Pedals and the steering wheel may or may not be installed.
Level 5 – The driver is no longer driving the vehicle, will not be required to and the vehicle will be able to drive in all conditions.