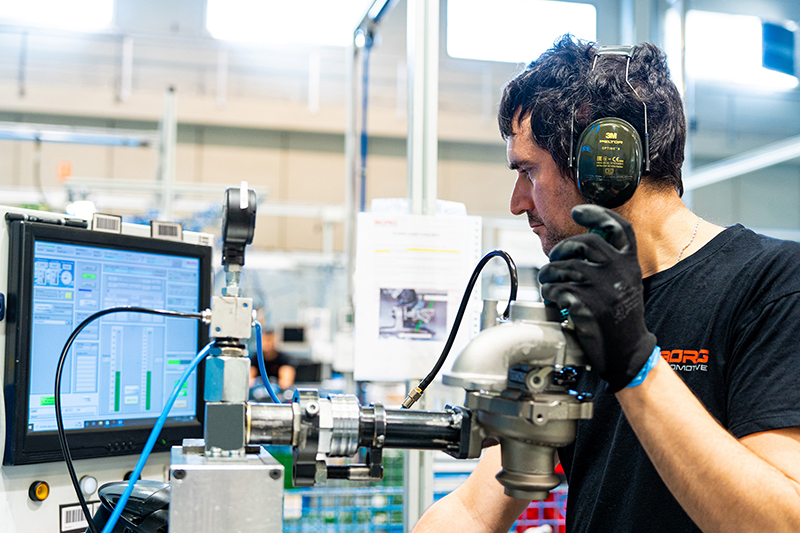
BORG Automotive Reman has announced it is addressing the doubts surrounding remanufactured turbochargers by demonstrating how they deliver performance on par with new ones, even though the cores are sourced from used components.
Through a remanufacturing process and quality assurance, including certifications such as DIN EN ISO 9001:2015 and the IATF 16949 automotive supplier standard, BORG Automotive Reman ensures each turbocharger meets the highest industry standards.
Only original parts are remanufactured. Each incoming turbocharger is disassembled, cleaned and thoroughly inspected. If it is suitable for remanufacturing, the specialists remove all dirt and oil residues from the housing parts. Small scratches on the inlet are polished out, and threads failing the quality test get repaired. Small and wear parts are replaced by parts from Tier 1 and Tier 2 suppliers. Each turbocharger is then balanced and the flow rate is adjusted according to the specifications. Each device must pass more than 30 tests before it goes on sale and is individually traceable as part of the quality assurance process.
What’s more, as thousands of used turbochargers pass through the hands of BORG Automotive Reman’s remanufacturing specialists, they can identify differences between various original designs. By applying the design optimisations from the latest versions to older models, they can help prevent premature failures.
Trend Towards Electronics Recognised Early
BORG Automotive Reman recognised a trend towards electronics and the integration of vehicle systems at an early stage and invested in the required expertise and processes to reengineer spare parts. As a result, the company is able to remanufacture not only electrically actuated turbochargers, but electric power steering racks or electric air conditioning compressors as well.
Nelson Gracias, Product Manager at BORG Automotive Reman, said: “It takes specialised know-how to remanufacture turbochargers with electric actuators. Depending on the design, communication between the turbocharger and the ECU is possible via both CAN bus and a pulse-width modulated signal. Understanding the flow of information is vital to guarantee optimum quality.”
Compared to purely mechanical or pneumatic systems, this allows the engine control unit to control the turbocharger performance particularly precisely and flexibly. Nelson explained: “Therefore, turbochargers like these are common in modern vehicles. This shows once again that the topic of electronics is becoming more and more important for remanufacturers. Those who don’t master it won’t be able to offer a broad and contemporary range in the future.”
Meeting Market Demand: New Turbochargers for Popular Models
A lot of the latest additions to the range of remanufactured turbos BORG Automotive Reman offers, feature an electric actuator, such as models from Hyundai, Kia, Nissan and Renault. They represent a pool of around 450,000 vehicles in Europe.
The turbocharger for Hyundai and Kia adds 44 new vehicle applications to the range. It is designed to be a replacement part for various 1.6-litre turbodiesel versions of the Hyundai models i30, i40, Kona and Tucson and the corresponding Kia vehicles from the Ceed, Optima, Proceed, Sportage and Xceed model series. The second turbocharger is designed for Renault and Nissan vehicles with 1.6-litre petrol engines. It covers a total of 18 vehicle applications, including versions of the Nissan Juke and Qashqai and the Renault Clio, Espace, Megane and Kadjar series.
Turbochargers from BORG Automotive Reman are available under the company’s own brands Elstock, DRI and TMI, as well as under the traditional Lucas brand, which is used under licence. The range now includes around 880 references for passenger cars and light commercial vehicles, covering more than 157 million vehicles in Europe.