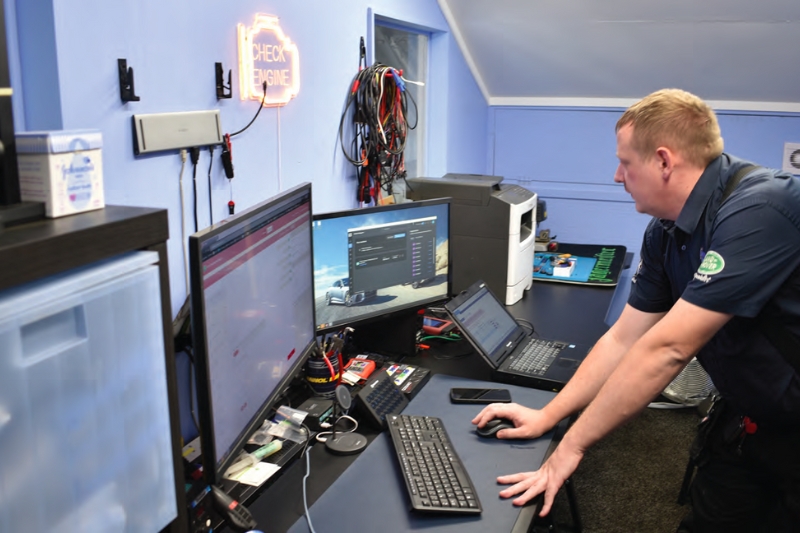
PMM’s editor Kieran Nee visits DTA Group’s Martin Hind to find out more about the benefits brought by Thinkcar’s remote diagnostics offering.
‘‘Who needs remote control?” the Clash asked long before my time, and whilst they might have been singing about the perceived injustice of being ruled by the “fat and old” people in parliament, the question might just as well be asked in the context of automotive fault-finding in a sector where independent workshops are increasingly struggling to access vehicle manufacturer data and to effect repairs through the security gateway. So, who needs remote (diagnostic) control? Quite a lot of workshop owners, actually.
Down to Dartford
To find out a bit more about this modern solution to a distinctly modern problem, I travelled to the DTA Group independent workshop in Dartford to meet with owner Martin Hind, who has been keeping himself busy helping out fellow garages in need via Thinkcar’s ThinkLink network.
Firstly, let’s explain what remote diagnostics actually is and why it might be needed. When I spoke to Thinkcar’s Alex Gillbanks last year for an article about the future of diagnostics, he brought up (among other things) remote diagnostics, referring to the associated tools as like having a “technician in the drawer”. This is because the diagnostic tool that allows you to access remote aid, in effect connects you with a remote-based technician who can dial into your tool and carry out the necessary procedure for you. Why you would want to do this? Well, it’s about who is and isn’t allowed to access and alter the vehicle manufacturer data. To reprogramme certain parts or even just to carry out routine maintenance and servicing on certain vehicles, you’ll need the dealer tool and as Alex put it, “not every garage will have the budget or inclination to buy OEM diagnostics”. Indeed, they can not only cost what is technically termed “a bomb”, but each comes with varying levels of complexity just to use the things. To own and master the dealer tools for all makes that will pass through your workshop floor in a given month is, without specialising on one brand, not feasible.
Remote done differently
What makes the Thinkcar approach to remote diagnostics interesting is that it doesn’t employ a team of technicians to sit in an air-conditioned office, fielding calls all day. Instead, it relies on “an ecosystem of Thinkcar workshops supporting each other with access to vehicle manufacturer level diagnostic platforms, [in which] queries can either be sent to the entire network or to a specific garage.”
When the system was first described to me by Alex, who by the way has the sole rights in the UK to distribute Thinkcar products, I immediately wanted to come and see how it worked for myself, imagining a kind of overworked manic master technician surrounded by computer screens in a dark workshop, solving everyone’s problems from on high… The reality, reassuringly, was much more… friendly!
Meeting Martin
Martin’s approach to remote diagnostics, and to car repair in general, I think it would be fair to say, seems to be based on an honest desire to help. He is, or at least was until really recently, the only JLR specialist on the Thinkcar network, so any Land Rover jobs came straight to him. The morning I visited him he’d already received three whatsapp inquiries – which is how jobs are requested – and he reckoned that usually about five a week convert to jobs.
“It makes more sense to turn to another workshop for help, when you know they have the right software, rather than turn to the main dealer for help,” Martin explains. “On some cars the DPF or GPF won’t regenerate if the service light’s on – simple, right? Just do a service. But if you don’t have the dealer software, you can’t even turn the service light off. So you bring it to the main dealer just to turn the light off and they insist on doing the service again from the start, so now that customer is ending up paying, at the very least, main dealer prices for a simple service. Whereas with the Thinkcar network, you can send the job through centrally or contact someone directly that has the tool you need, which will be me for a JLR job, for instance. I’ll get the job through, you plug your Thinkcar VCI unit, be it the X5, X10, EuroMax or 399, into the OBD-II port and I will be able to connect to it directly on my end and turn the service light off using my JLR software.”
You might be thinking this is just another cost to add, but actually the prices involved are very reasonable, as Martin tells me: “We have already paid for the year subscription of the dealer tool, so when we price up a job for a fellow workshop, we can charge a lot less than the hourly dealer rate, because we’ve already got the software paid for. And included in that price, unlike purchasing an hour’s licence on the dealer tool itself, is my labour, my expertise. I’ll try not to charge them if we don’t manage to sort the problem out. Another reason I can charge a lot less than if the car were physically here in my workshop is that I don’t have to provide space or insurance. Plus, I can typically do a remote job at the same time as doing another job on site. It’s perfect”
But why Thinkcar?
Well, Martin is effusive on the topic. “Aftermarket tools, generally, provide a lot more flexibility than dealer tools. I can do things here that the main dealer can’t! I don’t just have Thinkcar tools, I have a range of aftermarket tools and each one has its strengths. I am a massive fan of Thinkcar, though. The tools are just so intuitive and have a huge range of both cars they cover and tasks they can perform. If I just used my X10, I could still do most of my work. In my experience, Thinkcar tools can often do things that far more expensive tools can’t, so I’m happy with them, definitely.”