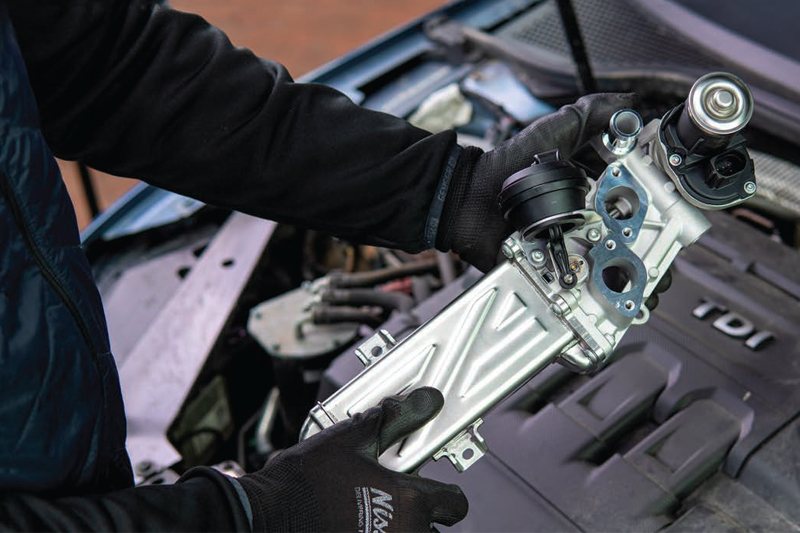
Nissens Automotive highlights some key information about exhaust gas recirculation systems and what opportunities they provide independent workshops.
A s the vehicle manufacturers strive to limit the impact that combustion engines have on the environment, the majority of new vehicles are equipped with an exhaust gas recirculation system, which subsequently provides opportunities for workshops, because of the way they are driven and the quality of the fuel used can result in a high rate of failures and, consequently, a growing demand for replacement components.
A fault with the EGR valve, for example, can lead to severe OBD errors that can result in the engine being set to limp mode and may provoke failures in other parts of the system. Common reasons for EGR system failure include unclean combustion, frequent short distance travel patterns, excessive thermal stress and moisture/contamination of the fuel.
Although there are several elements within the EGR system, the valve is central and it’s the part that is most often replaced. However, before doing so, it is important to undertake the correct diagnosis to find any underlying faults that may have caused or contributed to the problem the vehicle was brought in for. Common issues with the EGR system include:
- Engine irregular idling or jerking
- Engine “chattering noise”
- Insufficient engine performance (lower RPMs in petrol engines and higher RPMs in diesel engines)
- Engine limp-mode activation
- Engine misfires
- Illumination of the check engine light, often accompanied by diagnostic trouble codes such as P0401, P0102, P0402, and P0103.
However, before concluding that the EGR valve has failed, it is highly recommended to thoroughly inspect the complete EGR system, including components within the engine’s intake, exhaust and emissions control systems. It is also important to understand that the engine control unit monitors several sensors and components to maintain optimal performance and comply with emission standards, so if a problem occurs in one of the related systems, it can affect the EGR system’s function and result in error codes.
Therefore, a thorough diagnosis of the entire intake and emission control system is important if error codes are related to the EGR valve and this often requires inspecting and testing multiple components to identify the exact cause of the issue.
If, after following these processes, it is found that the valve does need to be replaced, once correctly installed, the valve must be calibrated with the ECU to function correctly. This adaptation process involves calibrating the EGR system to work seamlessly with a new or replaced EGR valve, or its related components and is essential to ensuring that the engine operates efficiently and meets emission standards.
The EGR adaptation process is critical for maintaining proper engine performance, reducing emissions, and preventing issues, such as rough idling or reduced fuel efficiency. It should be carried out by experienced technicians using appropriate diagnostic equipment, following the specification stipulated by the VM. However, the following section provides an overview of the EGR adaptation process.
Initialisation – After replacing the EGR components, the EGR adaptation process begins with the initialisation of the ECU. This step is performed using specialised diagnostic tools.
Learning phase – During the adaptation process, the ECU enters a learning phase. It collects data from the new EGR component to understand its specific characteristics and behaviour, such as voltage readings, response times and temperature ranges.
Calibration – With the collected data, the ECU calibrates itself to work optimally with the new EGR component. This calibration involves adjusting various engine parameters to ensure that the EGR system operates efficiently.
Verification and testing – Once the calibration is complete, it is essential to verify the correct operation of the EGR system. This may involve conducting tests to ensure that the EGR valve opens and closes as required.
Error code clearance – If error codes related to the EGR system were stored in the ECU before the adaptation process, these codes must be cleared to ensure that the vehicle’s ECU is not operating in a limp or reduced performance mode.
Final checks – After the adaptation process, a final check of the EGR system’s functionality should be performed to confirm that the EGR valve and related components are working as expected.
Road testing – To further validate the EGR system’s performance, a road test may be conducted to ensure that the vehicle operates smoothly under real driving conditions.
In addition to the technical support that Nissens provides, a further benefit for workshops committed to completing a full and thorough repair, comes in the form of the company’s “First Fit” concept, which, in common with every component in the Nissens range, means that whenever extra parts are needed for an EGR coolers’ correct installation, for example, these are automatically included in the box, making them easy to install, as well as saving professional installers time and effort in the process.
The entire Nissens engine efficiency and emissions programme now encompasses EGR valves, modules and coolers, turbochargers and oil feed lines, intercoolers and a throttle body range, and consists of 1,403 individual products, catering for more than 7,600 OE part numbers and serving the majority of the European PC/LCV parc.
Workshops already fitting Nissens parts, will be aware of the wide ranging technical support the company provides, but for those who don’t, a broad spectrum of technical information from training modules and videos, to best practice procedures and product information is available through the Nissens Experts portal.