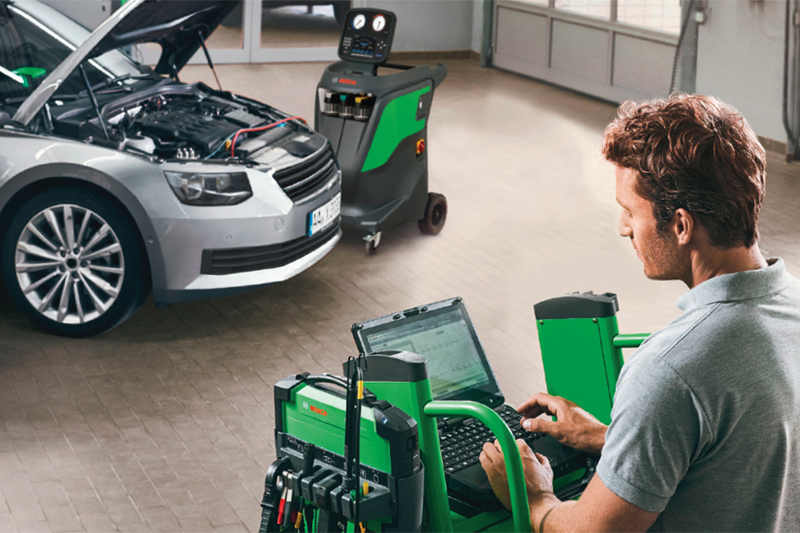
PMM hears from Bosch about how its Connected Repair solution can significantly increase the efficiency of the diagnostic processes required for air conditioning (A/C) servicing.
Workshops are dealing with a constantly growing demand for professional servicing of A/C systems. Most of the vehicles produced in recent years are equipped with heating and climate control. For this purpose, the control unit ensures the functional interaction between actuators, A/C compressor, engine cooling fan and the cabin fan motor. It also controls the heating system and the flaps guiding the air flow into the cabin. In addition, several sensors supply the system with information concerning temperature zones inside the cabin, exterior temperatures, engine conditions and settings made by the driver.
Accordingly, modern air conditioning service is much more than just standard routines. Using ESI[tronic] 2.0 Online and Bosch Connected Repair, Bosch A/C service units can be combined with troubleshooting and linked to diagnostic equipment to increase the efficiency of A/C servicing.
The A/C option
Bosch A/C service units are known for their easy handling, fully automatic procedures and their particularly high performance. Thanks to their ‘deep recovery system’, both the premium and standard models are said to recover up to 99% of the refrigerant even under difficult environmental conditions. The integrated forming-gas pressure test option allows accurate ‘leak-proof’ tests. The ACS 563 and ACS 553 entry-level units support workshops with daily service tasks such as refrigerant recovery, filling and recycling. They feature a recovery rate of up to a reported 95%.
In addition, the top model ACS 863 automatically tests the purity of R1234yf refrigerant. Moreover, ACS 763, ACS 753 and ACS 863 also feature an integrated nitrogen and hydrogen pressure test. Using the WLAN dongle, the units can also be integrated into as a network or linked to Bosch Connected Repair workshop software.
Staying connected
The ACS units can be combined with ESI[tronic] 2.0 Online and KTS-series diagnostic solutions. Due to the complexity and ongoing connectivity of today’s vehicle systems, the workshop’s way of working when servicing and performing repairs changes continuously. By means of the ESI[tronic] 2.0 Online features and the connectivity via Bosch Connected Repair, the company’s diagnostic solutions expand the workshops’ range of services while easing maintenance and repair procedures. Using the connected system, a vehicle driving up for its maintenance or repair can be identified by its vehicle identification number (VIN). This application eases entering vehicle and customer data. All information is entered just once. It is stored in a workshop internal database and can be accessed and reused at any time.
At the initial scan using Bosch KTS, the vehicle condition is analysed and possible faults are listed. The fault memory monitors the components connected to the air conditioning system via control units. In this manner, all of the vehicle’s fault memories are checked while allowing to save the results.
Besides reading out actual values of the components installed – e.g. the values of the temperature sensor – the A/C system pressures can also be analysed. The functionality of the control panel is checked as well.
Moreover, the ECU diagnosis includes different functional tests concerning the air conditioning system. For this purpose, components such as the compressor, the fan or even the air distributor can be operated and checked via KTS device. The nominal values and filling quantity are specified at the database of the A/C service unit and at ESI[tronic] 2.0 Online. In addition, technicians can also use experience-based repair (EBR). It comprises the most common A/C faults compiled by vehicle types. EBR is a database listing known faults and the respective solutions or remedies.
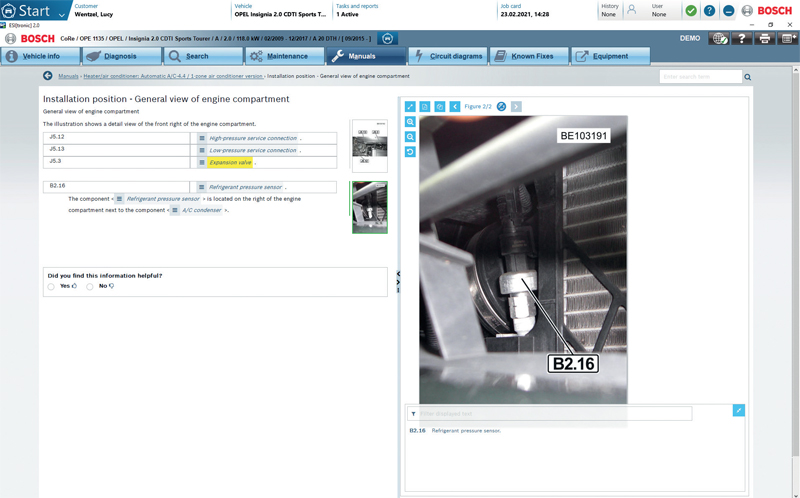
For additional information and regarding specific issues, users can access technical documents such as circuit diagrams, test values, installation positions, information on spare parts and additional support using ESI[tronic] 2.0 Online (as shown above).
The diagnosis includes routines to check proper A/C functionality. The results are documented as a protocol. Bosch Connected Repair provides a further unusual feature. It connects the test equipment such as ACS units, KTS and ESI[tronic] 2.0 Online with one another. That is, once the vehicle has been identified, test protocols and repair procedures are stored centrally in a paperless form. Even product information such as the order number of suitable cabin filters, installation instructions and test routines in line with the manufacturer specifications can be accessed easily for each vehicle.
Using a WLAN network and Connected Repair, workshops are able to connect their workshop equipment to one another. The data workflow enables them to increase both speed and efficiency of their work and save the results.