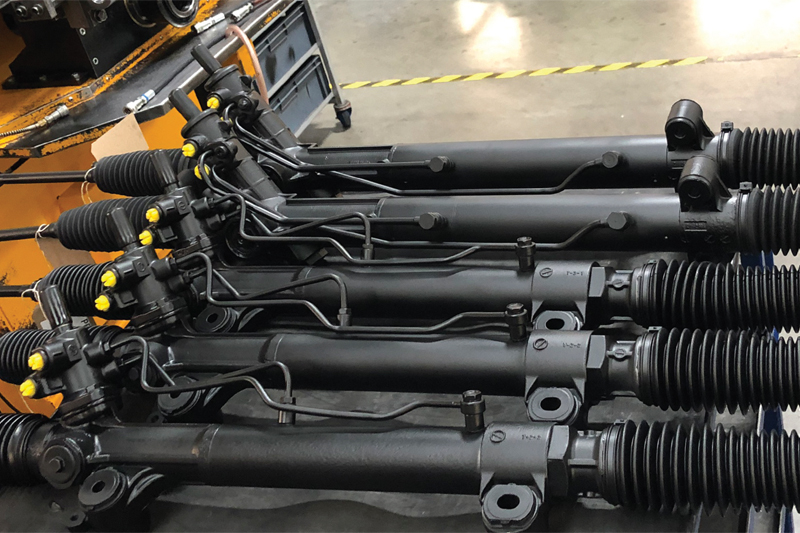
Joe Toakley, Marketing Manager at UK remanufacturer Shaftec, offers PMM readers an insight into the latest electronic power steering (EPS) developments, and how the automotive network communications protocol FlexRay is affecting this area of steering technology.
In 2021 you’d be hard pushed to find a vehicle rolling off the production line without EPS fitted, as standard. In line with industry trends, this makes perfect sense as the components are lighter in weight and more durable, require less maintenance, give a better response at different speeds and necessitate less fuel consumption. Because the numbers have been ramping up over the past couple of decades, most vehicles which fall into the aftermarket sphere for service and repair are fitted with EPS parts – and yet, there still seems to be a lack of knowledge across the industry in how to deal with them effectively.
Add to this a lack of investment by independent garages in the technology needed to programme the parts, and independents could be missing out on a large chunk of the available income stream.
If they don’t know which particular parts need specialist equipment in order to reprogram them, and then find that they don’t have the correct equipment, they may have to call in the expensive services of the main dealer who does – clearly increasing cost. This means they make less on the job than they anticipated, or worse still, have to explain to their customer that the job will be more expensive and take longer than they had quoted.
Once the fundamentals of ensuring you protect the integrity of the part by careful removal and storage, as well as protecting your surcharge by making sure cables are not cut and EPS motors remain intact and undamaged, and that the EPS part remanufacture processes are dealt with, you then move into the realms of software and programming…lots of programming.
Reprogramming EPS
At Shaftec, we have a stringent process of formatting the software on the EPS units so that when they are removed from the box they are ‘oven ready’ to ‘work’ in another vehicle. We make this crystal clear by adding a ‘Tamper’ label to the box to prove this has been done. In the unlikely scenario of a garage receiving a component with a damaged/broken label, they should source a replacement from their local motor factor. The part will then be returned directly to us and we will check the product thoroughly to ensure it complies.
But this is only part of the job. The bit we can’t physically do for our customers when it comes to EPS is the actual reprogramming – because this has to be done when the part has been fitted to the vehicle. Some parts can be reprogrammed using generic diagnostic tools – which garages really should invest in if they want to capture market opportunities. Certain steering systems, however, require bespoke Vehicle Manufacturer (VM) equipment in order to be successfully programmed for fitment. It helps massively if the garage is aware of which parts require which programming tools so that they can factor the cost of main dealer intervention into the original quote – and decide up front if they can make a profit.
FlexRay and EPS
In essence, the concept of FlexRay is a bit like going from broadband to fiber, and basically refers to the intercommunication through all electronic parts via the cars own mini ‘ethernet’. At the moment, the current ‘wired-up’ technologies in vehicles are up to their limit when it comes to sharing data across the vehicle.
FlexRay has a much larger bandwidth (ability to send receive far more data) resulting in greater control over safety systems and management of all components. This is paramount with the constant expanding technologies in cars and their components. And, as more and more vehicles use FlexRay, the parts have to remain compliant.
Knowing this was coming (FlexRay started to increase in prominence about 2014), and understanding that growth within the aftermarket was inevitable, at Shaftec we’ve been working on this project for some years.
We now have the capability to read the racks prior to beginning the remanufacturing process; allowing us to incorporate the programming and acceptance of FlexRay, ensuring reliable fitment without coming into electronic blockers. This has required a massive amount of R&D as well as greatly expanding the physical space being used within our facility to accommodate the different steering technologies.