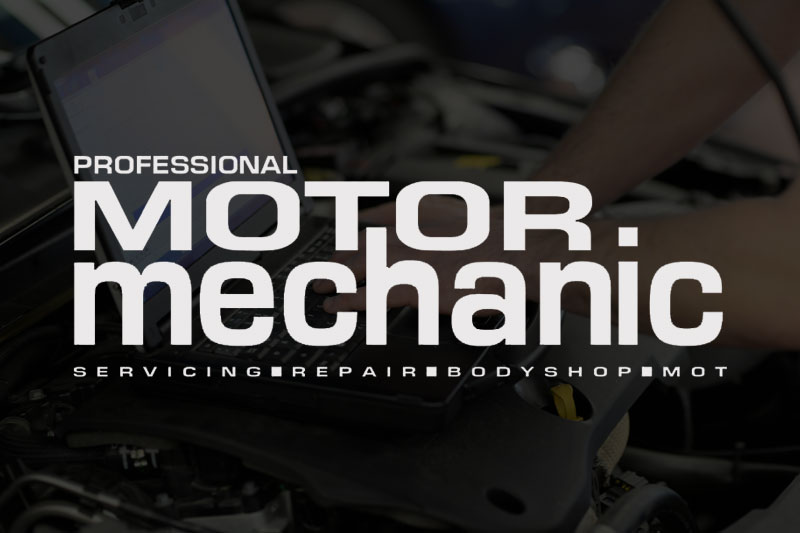
A measure of unjust criticism is levelled at the dual-mass flywheel, which is often charged with being more susceptible to failure than a conventional clutch. In reality, faults in other vehicle systems are regularly found to be the cause of noise and vibration issues attributed to the DMF, some of which may go on to accelerate DMF wear if not corrected promptly.
Diagnosis
The following procedures for fault diagnosis and damage assessment are suggested by ZF Services UK, which supplies the aftermarket with OE DMFs and ZMS clutch/DMF kits under the Sachs brand, as fitted and certified by some major vehicle manufacturers.
At the outset, do not assume that the DMF is the source of noise or vibration symptoms. First confirm that the correct DMF is fitted according to the vehicle’s engine code, and extract any engine fault or flash codes. Then check all relevant vehicle systems for correct operation to ensure they are not the cause.
Check the injection rate and ignition waveforms at idle to isolate misfires and examine the condition of any turbo boost pipework and hoses. Cylinder compression pressures should be correct, equal, and within the vehicle manufacturer’s tolerances. Examine camshafts for wear and check that crankshaft end float or lift is not excessive and that the crankshaft damper is undamaged. Check the EGR valve and swirl valve/actuator for correct operation, along with torque limiting valves and frequency modulators where fitted.
Do not overlook any user modifications to engine components or systems, as chip tuning or other performance enhancements may increase drivetrain vibration. Finally, check the gearbox for wear on its input shaft and associated bearings.
Assuming that all of these pass scrutiny, the DMF can be removed and examined in more detail for wear and fault indications.
Wear assessment
Full DMF function can only be reliably checked on a special test rig but some provisional tests are possible. Check radial movement by rotating the DMF in either direction; the movement should be smooth without jerking or binding. For a Sachs DMF, if the primary and secondary flywheels can be rotated more than 20mm in opposite directions by hand at the circumference, the wear limit has probably been reached. Only a small amount of axial (tilt) movement should be possible between the two masses – this is best assessed by comparison with a new unit, which typically has 2.00mm tilt. If a vehicle’s clutch is being replaced for the second time, replace the DMF too as its torsion damper is also a wearing component.
Mechanical damage
If the driven plate wears down to the rivets it can cause scoring on the secondary flywheel of the DMF. Check working surfaces for heavy wear and, if evident, replace the DMF – skimming is not permissible.
Excessive DMF oscillation may cause premature wear to the arc springs within. This typically occurs at very low engine speeds – driving in too high a gear, allowing the engine to idle for excessively long periods (e.g. to run air conditioning when parked) or frequent engine stalling are common causes. It is worth explaining to customers that avoiding such practices can significantly extend DMF life. Other possibilities include misfiring due to ignition or fuel system faults, uneven compression pressures or vibration caused by worn powertrain components as described earlier.
Overheating
Blue- or straw-coloured annealed areas or heat cracks on the secondary flywheel (see image below) indicate overheating, generally caused by excessive clutch slip.
This causes the lubricating and damping grease within the DMF to break down, reducing vibration damping and causing internal parts to run dry and wear prematurely. Compromised lubrication may ultimately destroy these parts, which subsequently damage the housing (see image below). If there is any evidence of grease leaking from the DMF it should be replaced.
The circle of rivets around the hub area on the primary flywheel provides further evidence of overheating. A line of yellowing joining these rivets indicates wear of the collar separating the two flywheel masses, which could result in metal-to-metal contact. Replacement is the only option for an overheated DMF.
Technical training
ZF Services UK has recently launched a technical training programme which includes modules covering clutch and DMF. Training takes place at the company’s centrally located Crick site, with each module combining classroom-based theory and discussion sessions with practical, hands-on workshop experience. The course material covers components and their operation, wear and damage assessment, vehicle system faults and their diagnosis, root cause analysis and fitting awareness, both in theory and practice. The emphasis throughout is on gaining advanced skills in identifying and rectifying problems in constantly evolving vehicle systems.