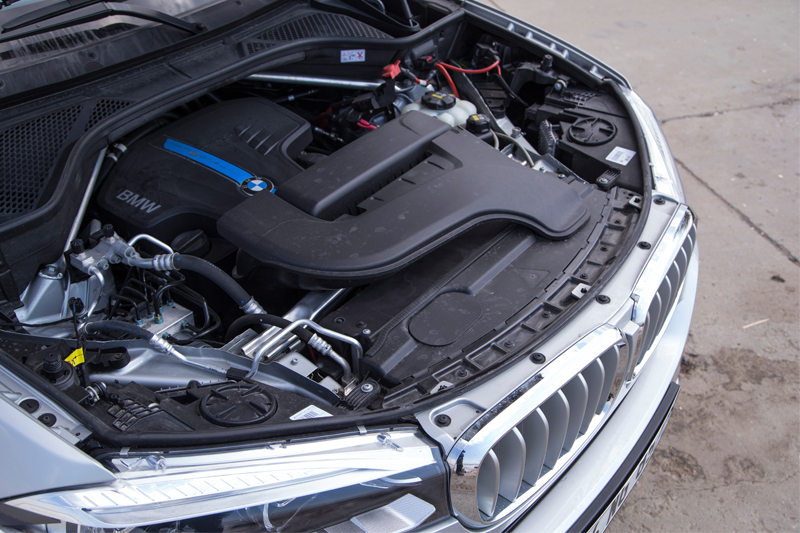
Ben Johnson is driven to his wits’ end by yet another BMW X5 40E in the workshop. This time, the car refused to start, until it did start… meaning it wasn’t simply the fuse at fault.
These days, the phrase “here we go again” seems to slip from my lips more often than not. It’s a refrain that frequently accompanies the sight of yet another X5 40E being towed in, the nature of its latest breakdown a mystery. This Monday morning was no different, as another one – this time an M-sport variant – sat forlornly in the car park. The recently installed towing hook in the front bumper area caught the glint of the early morning sun, its golden hue suggesting that before any diagnostics could commence, a push inside might be necessary. True to form, the tow truck driver had chosen the most distant spot from the workshop to deposit it.
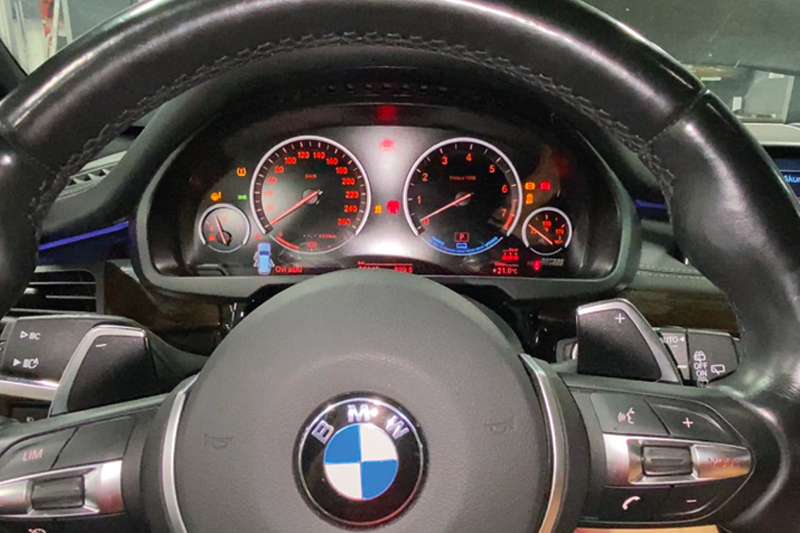
With a sense of determination, I attempted to start the engine. After two unsuccessful tries, hope was not lost. As the saying goes, perseverance pays off, and on the third attempt, the engine roared to life, albeit with a touch of smoke billowing from the tailpipe. But that was inconsequential. The primary goal was achieved: it could be driven to my ramp under its own power. After all, no one relishes the thought of exerting the effort to push nearly two tonnes early on a Monday morning.
Once securely positioned on my ramp, I made another attempt at starting, only to be met with resolute refusal. Despite my efforts to crank it, the engine remained stubbornly silent. Alongside the sound of the starter motor’s efforts, a check control message appeared, displaying “fuel system” on the Kombi LCD screen.
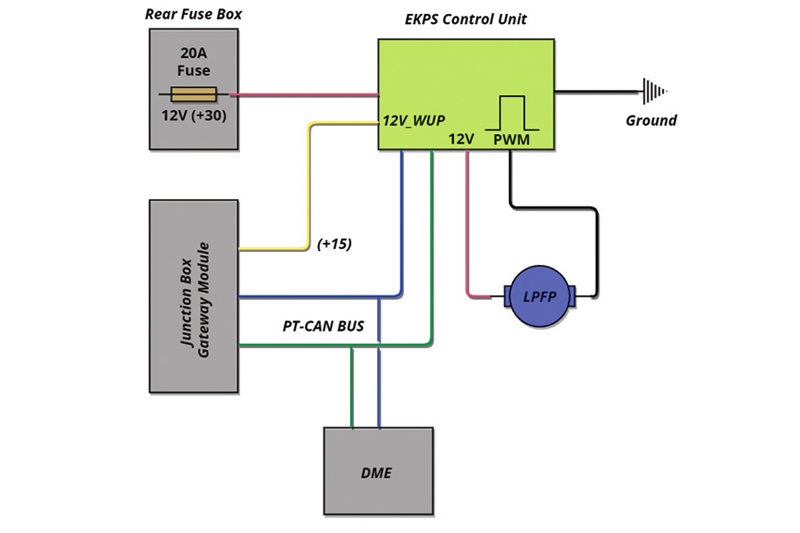
The diagnostic process using ISTA promptly unveiled fault codes pinpointing issues within the fuel system. Specifically, the codes indicated both excessively low high-pressure and low-pressure levels. In the realm of the X5 40E, the fuel system is straightforward and is overseen by the EKPS control unit. Operating on the PT-CAN bus, this unit’s primary responsibility involves energising the fuel pump – serving as the single-phase variant in this vehicle. Additionally, the EKPS undertakes the task of regulating fuel pressure, ensuring that minimal output from the in-tank low-pressure pump suffices when fuel demand decreases. This modulation is achieved through precision PWM control. The fault codes do not explicitly pinpoint a faulty control unit per se, rather the fault codes are stored due to the feedback from the fuel rail pressure sensor during engine cranking – pressure that is too low triggers the DME to set the fault codes. To provide an in-depth perspective on the fuel system, I’ve crafted an illustrative diagram (Fig.2).
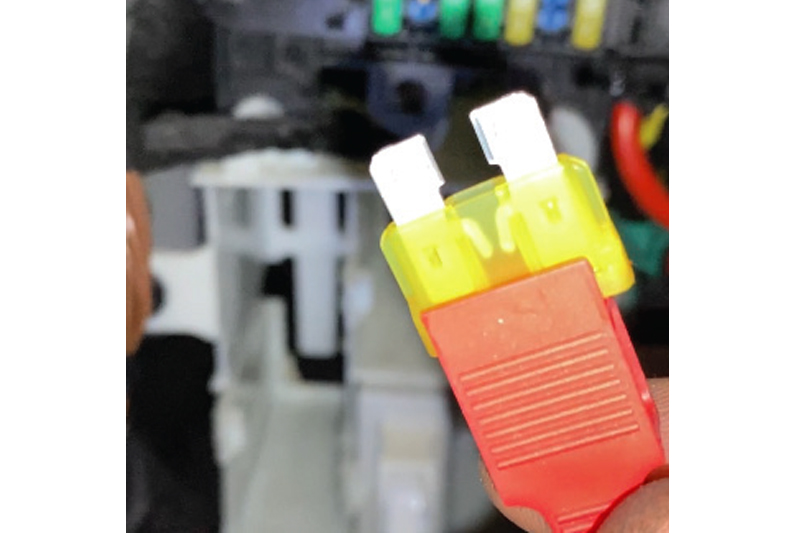
Getting started
So, where does one begin? Initiating a comprehensive vehicle test exposed a clear lack of communication from the EKPS control unit on the PT-CAN bus. As I consistently emphasise to newcomers embarking on this career path, the starting point is invariably the fuse check. True to form, the 20 amp fuse had met its demise. Positioned within the rear fuse box – located on the right rear section of the boot area – it’s this fuse that provides a permanent live power supply to the EKPS (Fig.3). The root cause behind the EKPS’ communication failure on the PT-CAN became evident, and logically, this issue would prevent the car from starting, given the fuel pump’s reliance on the EKPS. Yet, an intriguing puzzle remained: why did the vehicle fail to start for both the customer and myself, but then obediently roar to life after three attempts? This mystery was soon to be unravelled, revealing an intermittent pump malfunction that at some point had managed to evade excessive current draw. My working hypothesis is that this intermittent behaviour prevented the fuse from blowing earlier and the pump had simply just gone open circuit sporadically.
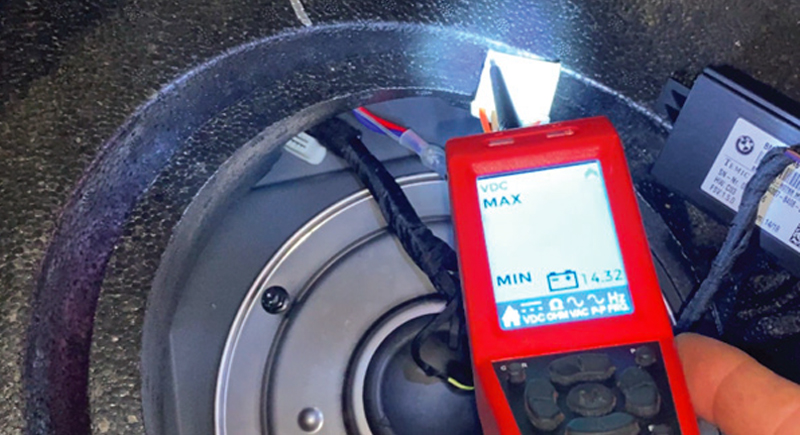
Pinpointing the issue
The open circuit phase was clearly now over as inserting a fresh fuse unveiled a repetitive pattern – every time the engine was cranked, the fuse would succumb immediately, joining its fallen comrades in the electrical graveyard (aka the bin). After enduring this exasperating cycle four times, I exercised prudence and shifted my focus towards disengaging the EKPS connector, marking the commencement of the testing phase.
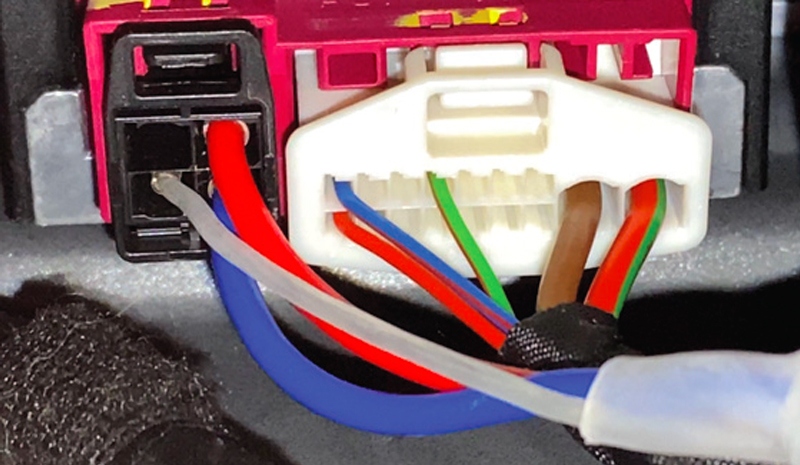
Upon inserting another fuse and activating the ignition, a glimmer of progress emerged – the EKPS showcased its willingness to communicate. Consequently, my focus pivoted to scrutinising the fuel pump itself, especially considering that detaching the fuel pump from the EKPS connector prevented the fuse from blowing. It was a clear indication that the fuse was blowing due to the excessive current draw attributed to a faulty fuel pump.
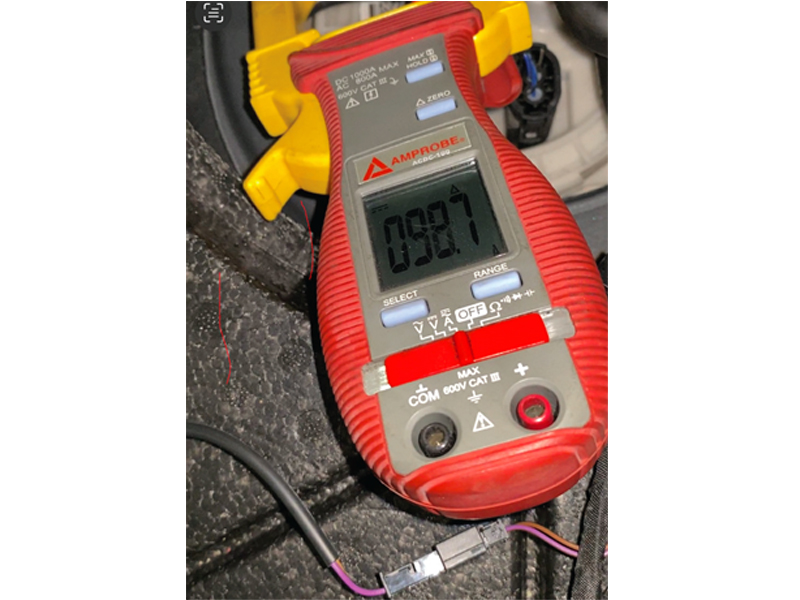
The task at hand demanded the deployment of an amp clamp, although the fuse’s swift demise made it nearly impossible to capture a meaningful reading. Compounded by the unavailability of my usual, smaller, amp clamp, I was compelled to employ a substantially larger clamp calibrated for the hundreds range. To obtain a tangible reading, I resorted to recording the clamp screen on my iPhone and subsequently reviewing the playback. The revelation was staggering: the current draw surged to an astonishing 98.7 amps. It became abundantly clear why the seemingly feeble 20-amp fuse met its end instantaneously every time the car was cranked over (Fig.6).
Having meticulously inspected the pump and discovering no anomalies, I deemed it necessary to check the pump wiring leading back to the EKPS. My efforts to unveil potential issues yielded no traces of shorting to ground or to 12V. A thorough assessment, conducted with both ends of the harness disconnected, again yielded nothing out of the ordinary. Armed with this evidence gathering, the course of action became clear: the decision was made to order and fit a fresh pump and EKPS. The outcome was as anticipated – the issue was resolved. Curiously, there were no indicators of scorching, arcing, or loose connections; the root cause appeared to be confined within the pump itself.
Although a simple fault find, this fault discovery brought a profound sense of relief, especially considering the myriad of issues that this generation of X5 has been prone to. It highlighted that the problem at hand wasn’t as severe as the array of potential faults that could have arisen.
The temptation to disassemble the pump in search of a cause was outweighed by the fact that the vehicle was fixed and running well. In a world where time is perpetually in short supply, expediency dictated moving forward to the next waiting customer. With any luck, the forthcoming months might usher in a period of respite, marked by a reduction—ideally, an eradication—of issues afflicting hybrid X5s and a well-earned break from these troublesome vehicles.