Apec Braking take us through the preventative steps you should take to avoid brake judder.
Brake judder is one of the few ailments that can affect all types of vehicles. Brake judder manifests itself in vibration, and it is a sensation that can be felt through the steering wheel, through your pedals and potentially through your seat. Depending on the severity, a car’s chassis has even been known to pulsate.
Customers affected by brake judder often jump to one conclusion: that they’re experiencing a side effect of warped discs or, more technically, distortion. The truth about the real causes of brake judder are, however, far more complicated; in the majority of cases warped discs have nothing to do with disc manufacture or quality and everything to do with fitment or driver behaviour.
In most cases, brake judder develops or worsens over a given timeframe. This is vital to understand from a technician’s standpoint as it highlights that when fitted, a customer’s brake disc was within manufacturer tolerance, and thus aggressive braking or a fitment issue is the root cause of the problem. In fact any disc, regardless of quality or materials, can warp (distort) under the correct circumstances.
Main causes
Let’s begin with the main cause of brake judder: Disc Thickness Variation (DTV). One of the major causes of DTV is lateral run-out caused by improper cleaning of the hub surface. Similar to the butterfly effect, even the most minute particles of rust caught between the disc face and hub (measuring as small as 0.04mm) can lead to lateral run-out (where the turning disc starts to deviate from its axis) in excess of 0.1mm when measured at the centre of the braking surface.
The important point to note is that while this deviation may not immediately induce brake judder, it has provided the foundations for a vibration that will eventually lead to it, causing potentially irreparable damage to the braking disc (although this may not occur for over 2,000 – 5,000 driven miles).
Secondly, it is essential brake discs and pads are “bedded in” properly, and customers need to be aware of the potential damage caused by excessive heat build-up. During the first 100 miles the driver should drive normally but try to avoid excessive braking which would elevate the temperature of the disc and pad.
All Apec brake pads go through a ‘High Pressure Treatment’ process, burning off many of the resins and gases at the factory that would normally find their way into the atmosphere during bedding-in; this gives a good initial braking performance.
During the bedding process a layer of friction material is evenly distributed across the brake discs. Too little heat during bedding keeps the material from transferring to the rotor face. Feathering the brake pedal while overheating the system can therefore generate uneven pad deposits due to the material breaking down and sticking to the disc, causing a stick/slip situation.
Once this has happened, heavy braking will lead to imbalanced heat build-up due to the uneven distribution of friction material across the disc, with high-spots heating excessively in comparison to the rest of the disc. If the temperature at these high-spots exceeds 650 ̊C cast iron changes structurally, transforming into an immensely rigid substance called ‘Cementite’.
As the disc is now composed of varying materials of different strengths, judder will progressively get worse, which explains why customers often return with their vehicles months after installation. This cause may be as simple as poor technique, using the brake pedal to slow the car rather than engine braking on serious inclines and repeated emergency stops without adequate cooling time!
Other factors
Outside of DTV, judder can also be caused by uneven torque on wheel bolts and issues regarding floating, fixed and sliding calipers. Fixed calipers have pistons on both sides of the discs due to the stationary caliper housing.
Excessive run-out will cause piston movement and can result in pedal pulsation and binding pads in the caliper will cause DTV. Sliding or floating calipers that aren’t sliding or that have seized will prevent the caliper housing from moving, so check the slider bolts for movement and corrosion and replace, if necessary. Always replace springs where a floating caliper is fitted.
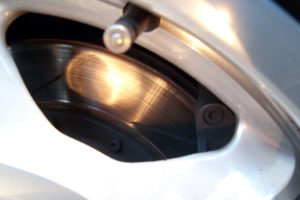
Poor quality pads may also be a root cause of brake judder as the friction material can overheat quickly, particularly if the brakes are used often and aggressively. It is also possible to warp a vehicle’s hubs, which will always result in brake judder. Again the root cause of a warped hub is excessive heat build-up caused by excessive friction.
Excessively worn or poorly fitted wheel bearings can also cause run-out at the hub. There are also occasions where manufacturer error can be the root cause of brake judder, but with modern machining and production lines this is increasingly unlikely.
How can technicians minimise brake judder?
Technicians must check disc thickness before refitting a disc, as if it’s outside manufacturer tolerances then it isn’t a serviceable item and requires replacement. Technicians are advised to pick eight equidistant points around the perimeter of the disc and to never base a determination of thickness on a single spot. Any variation in disc thickness will translate into brake judder.
You should always check lateral run-out, even when fitting new discs. With the use of a dial indicator you should target 0.05mm – 0.10mm as your maximum run out limit. If you want to check run-out of the discs independently of the hub, check the disc on a lathe and perform a dial indicator reading. In an effort to remove variables from the equation, make a run-out reading of the hub flange itself, without the disc. If the flange itself is causing the run-out problem, you’ll be able to isolate the cause.
Finally, it is imperative when refitting wheels, that bolts are checked and in serviceable condition. You should check the condition of the bolt threads as well as the integrity of the bolts. Never use fasteners that are suspect and also make sure all threaded locations are clean and free of dirt, grime or other contaminants; poor quality or unclean threads can result in incorrect torque readings. Never use an airgun to fully tighten a wheel nut or bolt as this could distort an aluminium wheel. The final tightening should be done with a torque wrench in the correct sequence.
Good practice prevails
Our final piece of advice is to always service the caliper, ensuring that the pad abutment points are lubricated, sliders (where fitted) are serviceable and working correctly and replacement springs are fitted. Although it can be time consuming, it is vital that the measures we’ve advised are taken and heeded by technicians. It is also essential that the importance of correctly bedding in new discs and pads is emphasised to the customer, because that conversation is nowhere near as expensive as replacing an unhappy customer’s discs and pads.