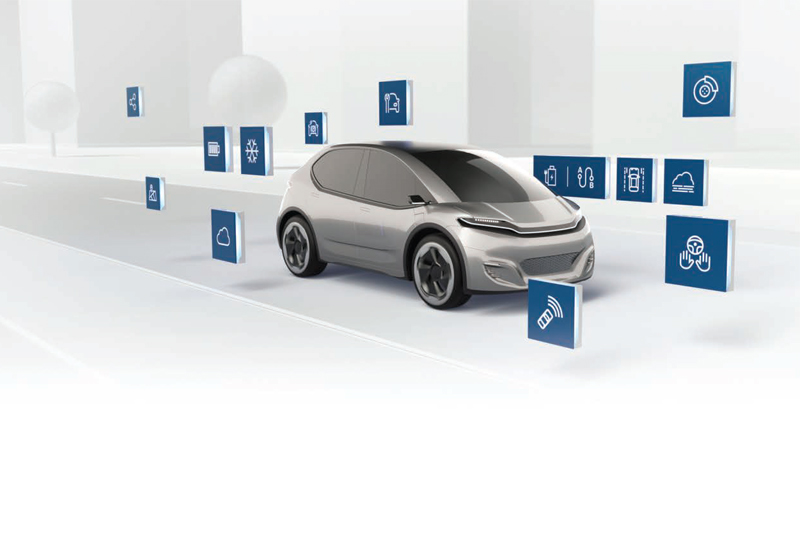
Welcome to the final instalment of our workshop guide to Bosch’s KTS diagnostics software, ESI[tronic] 2.0. It’s a been a long journey over more than a year. To refresh yourself on any of the topics covered so far, you can find all fourteen instalments on PMMOnline. Now though, let’s take a look at the concept of connected repair and see where the future of diagnostics lies.
Time, energy and cost are a premium in any workshop. If you are imagining a world where you can save time and cost without cutting corners or compromising quality, that world is a lot closer than you think. The Bosch ESI[tronic] 2.0 has some features that enable you to futureproof your workshop and have the support you need to focus on what really matters – the task in hand.
Your workshop is your business. This is where the action is and intuitive, connected technology that helps you improve the efficiency of your workshop can also make your life much easier. As technology continues to develop over the coming years, ‘connectivity’ will become less of a buzzword, more of an expectation. Bosch is facilitating connected workshops, helping give the businesses of the future a head start.
Different workshops have different requirements, which is why each CoRe solution reflects this. Workshops can choose the package to best suit their needs based on the amount of connectivity they want to have.
So why choose a greater level of connectivity? Well, Bosch argues that a simple system which is convenient for you and gives your customers peace of mind allows you to focus on the job in hand. The connected workshop stops you wasting time and effort on the small issues that can all build up to interrupt the flow of your day. Better still, these systems can be used in conjunction with ESI[tronic].
How connected are you?
1. Local Connectivity
- You have your own server and system.
- Data stays local as it’s stored in your workshop.
- However, if anything should happen to your workshop, such as a fire, you could run the risk of your data going up in smoke, as you won’t have backup.
2. Central Connectivity
- This uses the IT infrastructure of your workshop to store data on a core server, making it shareable.
- The data stays local and is stored on your own server.
- Again, you run the risk of losing your data should anything happen to your workshop.
- This version is included in the ESI[tronic] Advanced and Master packages.
3.The Bosch CoRe Cloud
- Your data stays local, but it is connected via DMS to the Cloud.
- You have a connected workshop solution without needing to operate a server.
- Data is stored securely in a central location, which keeps it safe should anything happen to your workshop.
Make your life easier
It is a requirement for workshops to hold data and audit trails are part of your business. But when it comes to cutting down on processing time, digital is the slicker option. By holding your data digitally, you are bypassing cumbersome filing structures and it becomes easier for your team to refer to past jobs and processes.
The connected workshop lets you adapt in a way physical paper and filing cabinets simply cannot – you are safeguarding your data and making the task more convenient for you and your team.
- The full history of a vehicle is all at your fingertips
No vehicle selection or identification is needed when a vehicle comes into the workshop, as it is all stored on a central system. That means less time spent trawling through the system to find makes and models. Additionally, as you have access to the vehicle’s full history, you immediately see what kind of service and repair activities have been done in the past on the vehicle entering your workshop. You can compare it with a ‘medical file record’ of the car, including all the historical diagnostic and test protocols.
- Your team have the information they need, exactly when they need it. Technicians may not always have access to workshop management systems or members of staff may leave the business. The connected workshop system cuts out laborious checks and having to navigate different people in your business. Your technicians have everything they need – as it’s all there!
- Vehicle owners can see the work for themselves A connected workshop means technicians can upload photos to the central server easily, helping owners to see exactly what work has been done on their vehicle. This is particularly useful when used as supporting material for invoices.
A more connected world
We know searching the internet for a diagnostic or repair solution can be a time- consuming business – particularly when you’re factoring hundreds of different car makes and models into your search. So Bosch is working with specific manufacturers that will enable data sharing – the crossover of technical information and data between car manufacturers and independent workshops.
One example of this is a first notification of service need in the independent aftermarket. Detailed live data will enable independent workshops to let customers know directly when their car is ready for service. Vehicle drivers would then have the option to select the workshop as their preferred service provider and the relevant data is then transmitted into the Cloud by the vehicle, so that the preferred workshop is notified of the vehicle’s requirements. While still in conceptual form, this is a step towards a more connected world between independent workshops and vehicle owners.
One stop shop
Car diagnostics can be tricky to navigate and expensive for many workshops. When diagnostics and repair require solutions that are specific to different vehicle manufacturers, you need to know you have the right tools for the job (Fig.1).
The problem is these tools differ between makes. One option is to buy the tools you need from each manufacturer or multiple all makes solutions, along with the licenses, hardware and subscriptions required – all of which are extremely costly.
Another is to specialise in three or four car brands, limiting the vehicles you can bring through your doors. Finally, you could take vehicles directly to the manufacturer’s garage, which costs money and takes away valuable resource from your workshop.
But as of last year, there is another option: the Remote Diagnostics Service. Bosch is building the infrastructure to provide a complete solution to workshops, which consolidates all your requirements in one place. Using a combination of ESI[tronic] and a remote diagnostic solution connected to the vehicle via a single VCI (KTS 560 or 590), technicians can connect Bosch’s specialists with the vehicle. Bosch’s experts can then access the vehicle and solve the issue remotely. This one stop shop has the functionality to solve issues with vehicles across a wide range of makes and models, cutting down on the time and expense of searching for a solution online. Instead, one solution gives you access to a wealth of knowledge and expertise!
We’ve shown you how the power of connectivity can elevate your workshop for the future. Your ESI[tronic] 2.0 can facilitate this, but to conduct quick and efficient, repair and maintenance using Bosch vehicle system analysis technology, use the KTS 560 or KTS 590 alongside your ESI[tronic] 2.0. With vehicle systems and components becoming ever more complex and diverse, the KTS covers everything a workshop is going to need to not just survive in the future, but thrive.