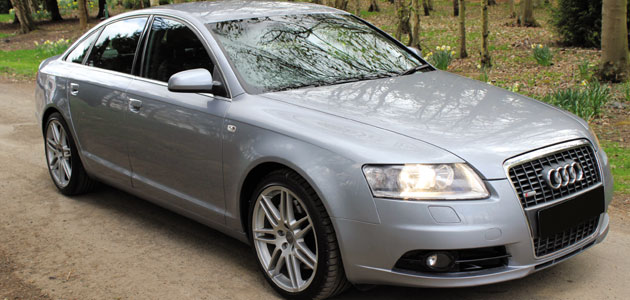
Author: Andy Horwat of Engine Tuning & Diagnostics in Swindon
The vehicle in question was an Audi A6/V62 2.7l turbo diesel and the complaint was that the vehicle was continuously going into ‘limp home’ mode with the glow plug lights flashing and a loss of engine power.
Recalling the first time that it happened, the owner explained that he went to accelerate hard on the motorway and the glow plug light illuminated, before a loss of power soon followed. Fortunately the car restarted and he made it home. This appeared to be a one off thing, until a week or so later when the problem got progressively worse – even on a short trip.
Evidence gathering
Once the vehicle entered my workshop, the first port of call was to gather some facts, so I called upon the Hella Gutmann Mega Macs 50 scan tool to help me with this. It presented me with one fault code – PO1020: fuel pressure regulation – a good start. This then needed to be followed by a test drive.
From driving the car myself it was clear to see that in stop/start traffic there were no real effects, however, once we hit the open road in a lower gear, and with max throttle, the reading was showing around 900 bar – nowhere near the expected pressure required from this system. The vehicle subsequently went into limp home mode and the same fault code had returned.
The Audi only had one previous owner and the mileage of the car was around 170,000 – a high figure, but not something that should have caused an issue in this case. In the workshop we had to consider all the factors that could be responsible for the low pressure generation, such as: fuel supply, a blocked fuel filter, excessive leak across the injectors, a faulty pressure regulator or faulty pressure pump.
I therefore decided to carry out an injector back leak test; a dynamic test with the engine running on idle. The back leak should be around 2-3 min and the limit within 10%. Starting the engine, and running on idle, the first fault was discovered – injector no.3 took 30 seconds to fill the flask. I now knew that we had a faulty injector, however, one injector can’t be responsible for such a big drop in pressure. A replacement was fitted but the injector that was removed appeared to be contaminated with deposits of water, or some kind of acid, so I had to bear in mind that there may be more trouble ahead.
Desired reading
My next test, I decided, should be the supply pump and fuel filter. The low pressure pump is a mechanical-type, and, once fitted to the rear of the high pressure pump, with the low pressure gauge connected and the system primed, the desired reading of 10-20CMHG appeared.
After starting the engine and observing the flow and pressure, before allowing the engine to idle, it became clear that there was contamination in the fuel as it was off-colour and there were cavitation air bubbles present. I also observed that the negative pressure was beginning to rise to 40CMHG and beyond so it became clear that we had a clogged fuel filter. What was most worrying to me, however, was the fuel being significantly off-colour.
I replaced the fuel filter and, at the same time, emptied the original filter into a clear flask; heavy deposits of dirt and dark coloured fuel could be seen. A fuel sample was taken from the flask, but it appeared to have no signs of contamination. The evidence was pointing towards a disintegrating fuel filter and the main concern was to find out what damage had really been done.
In the high pressure system a replacement filter was fitted and the system was primed. I opted to leave the low pressure gauge connected, restarting the engine and allowing it to run, thus removing any pockets of air in the system. The clear pipework was now shown as clear and fuel was flowing at the correct pressure of 16CMHG.
Return of the warning light
The next step was to take the car on another test drive to see if we had come to a successful conclusion. The warning light immediately presented itself as we accelerated up a slope; the slight difference this time, however, is that we managed to travel a little further with fuel pressure at around 950 bar before the usual limp home mode and loss of power. So, we have a normal/clean low pressure supply and flow and the evidence is slowly pointing towards high pressure fuel regulation. The readings obtained by the scan tool clearly showed that the high pressure pump didn’t like being pushed beyond 900 bar for too long.
I decided to carry out my next test on the high pressure system. This is split into three separate areas: the pressure regulator valve, pressure sensor and the high pressure pump. The tests were carried out with the flow volume valve disconnected to produce max fuel flow to the pump and the first course of action was to disable the injectors connecting the high pressure gauge.
Using this to drive, I closed the PCV and, after disconnecting the fuel return pipe, the expected value should be 10cc over a period of five seconds. Additionally, engine cranking at the required pressure should be 1,000 bar and it must hold another point. The rise time and stability also had to be monitored. Connecting the scope to the output circuit from the pressure sensor is ideal and I found the PCV was leaking well in excess of the permitted amount – in fact it filled a small flask. Even more alarming was the scope reading of 1.8V!
After observing the rise time on the scope, the high pressure pump appeared to be on the lazy side, so a second test was carried out over a longer period of time. The return pipe was then reconnected and crimped to prevent any back leak. This test, however, didn’t show any significant improvement. The high pressure pump should be capable of holding the pressure but this didn’t happen. Instead, as soon as the engine cranking ceased, the scope reading showed a drop from 2.8V to 1.4V (holding steady at 1.4V), meaning the pump wasn’t able to hold a pressure beyond 400 bar.
Faulty pump
In an attempt to put the matter beyond doubt, I replaced the PCV with a dimming regulator. When connecting the high pressure gauge to the rail pressure sensor, a pressure of 1,000 bar should be reached in around 5-6 seconds and must hold, however, when the cranking time ceased, the indicator dropped very quickly and stabilised at 400 bar. This proved that we certainly had a faulty pump on our hands!
With all of this evidence at hand, I knew it wasn’t going to be a cheap repair or a quick fix. The first step was to remove the pump and send it off to be tested to find out exactly why it had failed. The pump was sent to a diesel specialist – who, in my experience, has the best facilities to deal with this particular job – and a replacement pressure regulator was ordered in the meantime. I also took another fuel sample which, to my surprise, was clean.
Bad news then reached me from the specialist: I was informed that the pump was beyond repair. They explained how the internal part of the pump was covered in rust and two out of the three non-return valves had failed. A replacement for the part was estimated at around £1,000 and, as they were in short supply, it would take up to four weeks to be delivered. This was not so much a solution as a complete disaster!
Alternative supplier
A second course of action was decided, so a second-hand pump was purchased from an alternative supplier and sent off for testing. Following their recommendations, all three valves were replaced to be on the safe side and, at the same time, the bill was more than halved. The pump arrived shortly after and was fitted, but there were still a few questions I wanted answered. My customer had mentioned that the car had been run on low fuel levels for a long period of time, so I decided to cut the fuel filter open and what I found was very interesting – put simply, a diesel tank on low levels of fuel is a breeding ground for all sorts of parasites and condensation.
To assemble all the parts took around two hours, the system was primed and the engine started. I allowed for the requisite warm up time and carried out the necessary checks, before road testing the car. As the moment arose I was confident that there would be a satisfactory outcome and, with the scan tool connected, I didn’t have to wait long. The tool soon read 1,700 bar under load and the car was then taken on an extended test drive. Bingo – I had my (expected) positive result.
Conclusion
This was a fairly irregular case for me as, for a change, I got to tackle this job first before any other garages had got their hands on it. It has taught me the value of applying a systematic approach and everyone concerned has learnt something useful, including the owner, who now keeps his tank topped up and purchases fuel from a more reliable source. For me, an additional satisfaction came from the fact that we were able to find a very viable alternative for the ridiculously overpriced pump replacement!