Common turbo failure modes create much discussion amongst the turbo industry, however, an area often overlooked as a potential for failure is the re-installation of a turbo following repair. There are many simple checks to carry out before a turbo is installed, which help prevent catastrophic failure and unexpected repair costs.
When a turbo fails and is removed for repair, it is possible for debris to find its way into the air intake and exhaust systems in the form of foreign objects or liquid contaminants – such as coolants, water, fuel, lubricants or cleaning products – which enter into the lubrication system.
At Melett, we continually inspect failed units which can often reveal contaminants in the engine oil, despite the oil being changed during the installation process. A cause of this could be insufficient cleaning of the bearing housing during the repair, leading to shot-blasting beads finding their way into the oil feed and contaminating the oil supply.
Oil obstacles
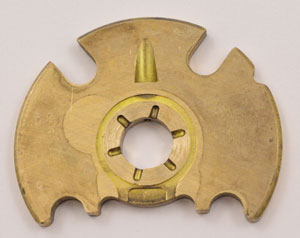
Oil is a critical component to ensure the longevity of a turbo and its components. If materials fall into the sump area of the oil return feed, they would normally be collected by the engine’s oil filter system and are unable to find their way back into the lubrication circuit. However, small amounts of debris in or around the threads or joints can bypass these filters and cause irreparable damage to the internal components if they enter the lubrication circuit. Turbos are precision engineered products and it can take a matter of seconds for a new turbo unit to fail if debris is present.
Liquid lessons
Liquid contamination is another cause of premature component failure as the presence of liquid within the oil drastically reduces the capability of the oil to lubricate and cool the turbo. Water contamination, for example, causes the oil to have a higher viscosity, as well as causing a loss of film strength, which is critical to the performance of the bearing systems. Therefore, care must be taken to avoid contaminating the oil supply, as liquid contaminants can do as much damage as foreign objects.
Feed fundamentals
Another failure is a blocked oil feed, caused by silicone sealants. Every turbo manufacturer stipulates that high-quality gaskets must be used rather than sealants. Before a sealant cures, there is time for it to spread and travel into the oil feeds of the bearing housing. This results in a blocked or restricted oil feed, preventing correct oil flow through the turbo, causing irreparable damage to the components within the turbo through lack of lubrication.
Debris dangers
During installation it is essential to ensure that no foreign objects can reach the turbo through the air intake or exhaust system. Checking these systems are clear from debris and other objects is a must, along with replacing the air filter, and cleaning the filter housing in the process.
Prime time
As a final precaution, before bolting the oil feed pipe to the turbo, prime the turbo with clean oil; using a syringe makes this much easier. During start-up of the engine after installation, there is a short delay before oil reaches the turbo. Failure to prime the turbo will cause wear to the bearing systems, resulting in premature failure due to dry start-up.
Seek a specialist
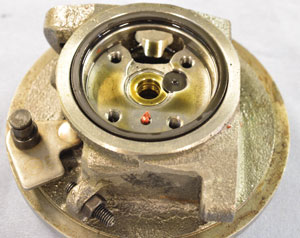
In recent years the turbo repair industry has grown significantly and replacing turbos is becoming common practice amongst garages. These checks, therefore, will aid a quality installation. It is advisable to use a qualified turbo specialist for turbo repairs, with the correct experience and know-how, and who will be able to offer assistance and guidance when refitting a turbo. Failure to carry out any of the checks described could prove to be extremely costly and, in some cases, extend the repair waiting time for the customer.
Installation Checklist
✓ Ensure no debris or fragments from damaged components remain from the previous turbo failure.
✓ Use new high-quality gaskets to prevent gasket failure and leaks.
✓ Make sure all air pipes are thoroughly cleaned and are clear from blockages and other loose objects.
✓ Void liquid contamination of the oil supply.