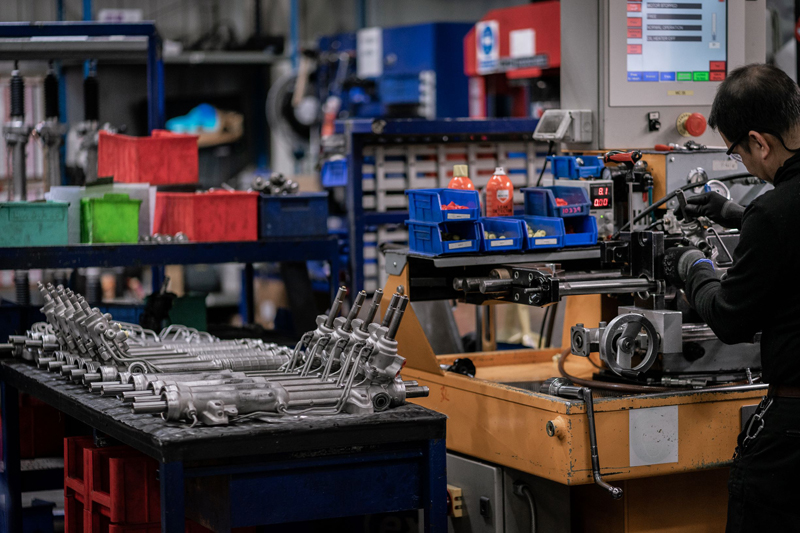
Shaftec’s Marketing Manager Joe Toakley discusses the importance of flushing your steering system and why you should never try and cut corners.
A single litre of flushing agent to flush the system is never enough. It should be five litres, every time.
The steering system consists of several items: a rack and pinion connected to the front wheels; a piston inside the rack and pinion, which is moved by pressurised fluid from the power-steering pump that helps to turn the wheels; and a cylinder containing fluid mounted on the pump or remotely mounted for easier access.
Leaks in the system allow foreign particles to enter more easily and with low fluid, steering becomes more difficult and parts can become damaged.
If you discover a leak in a customer’s system either by fluid on the ground or by a low power steering fluid, you should check it immediately. Low fluid levels can be a warning sign: if everything is working as it should, the fluid levels should never drop. It’s therefore vital to regularly check power-steering fluid levels and top up when necessary.
Pumps and racks will live longer if the system is flushed regularly, as systems deteriorate over time. As the system ages, small particles start to break off – then it can get really tricky. Contaminants are suspended in the steering fluid which then becomes abrasive, which then speeds up wear in other parts. Contaminants from rubber pipes and particles of metallic swarf from other areas – such as the impellers of the pump – gradually build up, causing more wear.
This, together with fluid oxidisation which propels the build-up of air and results in further inefficiencies and noise, causes ongoing deterioration until, eventually, the system fails.
As all contaminants originate from inside the enclosed circuit, the only way to prolong the life of a pump is to change the fluid regularly, flushing the system thoroughly each time. The contamination collects inside the system where you can’t see it, so the effects may be barely noticeable until the system fails. By the time the system fails, you are in trouble.
Because of this, there is an ongoing debate as to whether fluid change should be a standard part of the service schedule. If the system has failed on a vehicle it’s highly likely that there are raised levels of contaminants in the lines, making it even more important to flush the whole thing out before fitting a new part.
Fitting a new part without flushing out the system would be somewhat counterproductive. With raised levels of contaminants in the lines, the fluid would still be abrasive. You can sometimes see if the fluid is contaminated by its darker colour, or if you feel particles between your fingers, you shouldn’t take the risk or it can be costly.
Before any change, the system should be flushed properly using a professional machine which sucks out all of the old fluid and any contaminants. Only after washing it through thoroughly with a flushing agent until it runs clear should new fluid be added.
It’s also important to clean out the reservoir because any larger particles will settle at the bottom as the fluid circulates. If you don’t, when the new fluid is poured into the reservoir, any remaining silt at the bottom will be forced straight back into the system, causing a leak almost instantly.