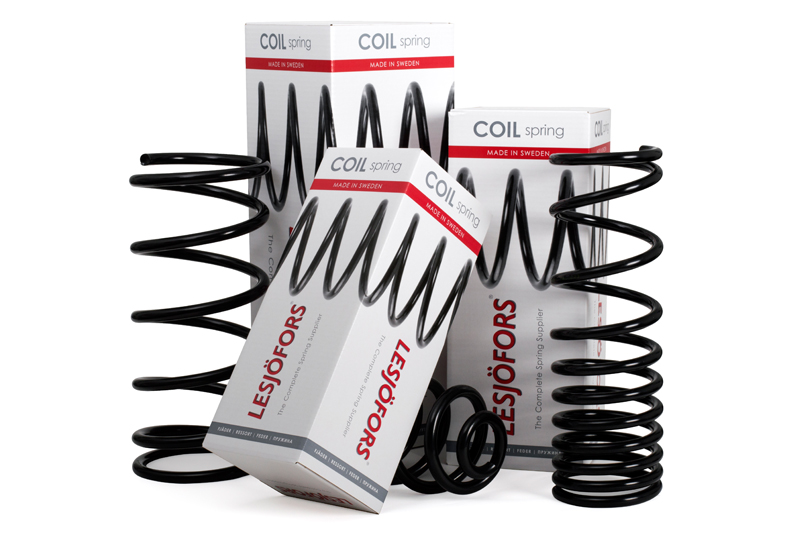
There are currently weak regulations in respect of coil spring testing when it comes to the MOT, but this shouldn’t stop technicians paying these components the attention they require, says Lesjöfors.
MOT inspection rules changed on 20th May 2018, giving additional guidance for the testing of suspension components, including coil springs.
Despite some improvements, the regulations are still too vague and should be updated with specific examples of reasons for rejecting a coil spring. Currently, a coil spring should only be rejected if:
- The spring is insecurely attached to the chassis or axle, or has loose fixings to the extent that relative movement is visible
- The spring is fractured or seriously weakened
- The spring is missing
- The spring has an unsafe modification
These guidelines give MOT testers a lot of leeway to pass a spring which may in fact be dangerous, as words like ‘insecurely’ and ‘seriously’ are not defined and thus must be interpreted by the tester.
The new guidelines finally include ‘unsafe modification’ of a coil spring as a potential reason for rejection/failure, but still allow welded repairs in certain circumstances, despite the fact that introducing heat to a coil spring can pose a significant safety risk:
Every automotive coil spring requires heat- treatment during the production process. This involves hardening (heating and rapidly cooling the spring to make the spring hard and brittle), tempering (further heating to decrease the hardness but increase the toughness, giving the required spring properties) and stress-relieving (a low- temperature heat treatment which increases fatigue performance), followed by pre-setting to further improve fatigue performance and reduce the risk of breakage.
Once the heat-treatment process is complete, introducing extreme temperatures via welding will alter the internal structure of the spring, while the electrode rod used to complete the weld will not be of spring-steel quality, significantly increasing the risk of breakage. Even errant weld spatter from neighbouring repairs can create stress risers in the spring, leading to premature failure.
The document also states that: “welded repairs to highly-stressed components aren’t normally acceptable, other than where the component is made up of sections that are welded together. To pass, the repair should appear to be as strong as the original design.”
This ambiguous guideline appears to allow welded springs to be passed without testing the actual strength of the spring, as long as it looks as strong as the original. As the ‘appearance’ of strength does not necessarily indicate a strong spring, this is potentially dangerous.
The guidance given about coil spring corrosion is similarly vague. The guidelines for corrosion of highly-stressed components state that a spring should be rejected if corrosion has resulted in a ‘serious reduction’ of the overall thickness of the material or has caused a hole or split. Once again, the word ‘serious’ is not defined and is open to interpretation by the inspector.
Overall, the new guidelines are an improvement on the old, but are still too vague and give inspectors latitude to pass springs which may be dangerous. The guidelines should be updated with clear examples of what is and is not acceptable, and any vague language should be clearly defined, with examples, or removed. This would result in much clearer guidance for inspectors, reducing the possibility of unsafe coil springs being passed and allowed back on the road.