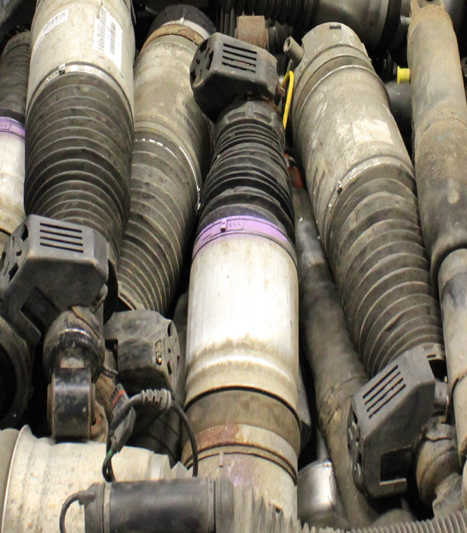
A look at the key elements required to produce a quality remanufacture.
Typically, the remanufacturing process can be split into a number of separate stages:
1. Disassembly;
2. Inspection;
3. Sorting;
4. Cleaning;
5. Reprocessing;
6. Reassembly;
7. Checking and testing.
The same steps used in the process of disassembly, re-processing and restoration are generally utilised by most quality remanufacturers, however the checking, inspection and testing processes can vary from company to company, or depending on product group.
Core collection
Before any quality remanufacturing can take place, companies must first obtain ‘core’ units. The core is essentially the original ‘carcass’ of the failed component, which has been returned to the supplier by motor factors (via their garage customers) or by specialist core collection services.
By working with a good quality returned core the hard parts, such as engine blocks, crankshafts, valves, rod bearings and cam shafts are able to be cleaned up and re-used, while high-wearing components such as sleeves, gaskets and bearings are then replaced with new.
“Obtaining core in a fit state to remanufacture can be difficult,” says Kevin Price, Marketing Manager at Brake Engineering.” “Damaged core isn’t suitable for the remanufacture of safety-critical parts, such as
brake calipers, so we have to invest heavily in the quality of the return and the source of collection.”
Tom Curtis, Director at Shaftec, adds: “The importance of core quality varies from product to product. When remanufacturing driveshafts we always replace the pots and CV joints and, as long as they’re not broken or bent, we can re-use them. “Calipers are similar; as long as the casting isn’t badly corroded or cracked we can generally remanufacture them, as everything else is replaced.”
So how does a remanufacturer decide which components need replacing?
Tony Bhogal, MD at Autoelectro, answers: “In the overall remanufacturing process the disassembly process is perhaps one of the most critical elements. It is within this process that the product is fully understood and recoverable parts are identified.”
At this moment in time, there is no EU legislation that standardises the process by which companies should remanufacture different components, but APRA’s Gregor Schlingschröder says that good quality remanufacturers should have stringent production and testing processes in place. He says: “It’s important to realise that there is a huge amount of investment needed in the correct test equipment that can allow any supplier to check the quality of their remanufactured components.
“By committing to the implementation of industrial standard processes, remanufacturers are able to achieve a high level of remanufacturing quality and can support this by offering a warranty with the product.”
Tony Bhogal adds: “Most reputable remanufacturing organisations will work to internationally recognised standards such as the ISO9001:2008 quality standard and the ISO14001:2008 environmental standard. “These standards give potential customers confidence in the processes and procedures that the organisation has adopted.”