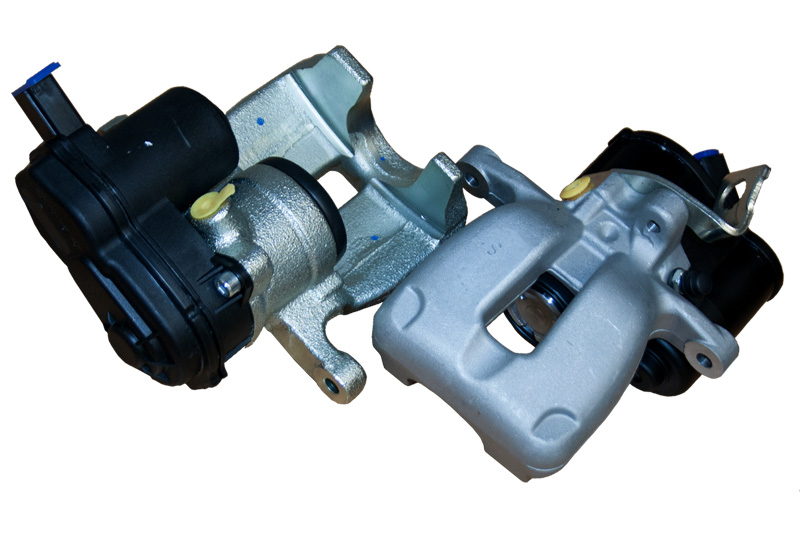
According to transmission supplier, Shaftec, remanufacturing is the way to go, providing efficient use of existing materials and resources, parts which perform to the same standard as new, and a more economical way to keep many vehicles on the road. A win-win for all involved?
Tom Curtis, Shaftec Director, states: “Remanufacturing is not just a poorer substitute for new. It’s a process which results in components that are as good as new, tested new and which perform in that way for the lifetime of the part.”
In line with this, the business operates a thorough, efficient and safe ‘Recon & Return’ programme for brake calipers, driveshafts, steering pumps and racks. Put simply, this means that, if used core meets its returns criteria, Shaftec will recondition and return the part to you, as new, with the same warranty as a new part.
The expert remanufacturer first of all assesses the core for its reman suitability. The criteria are bespoke to the product being remanufactured, but in all cases the core has to meet certain safety standards, so it cannot be broken or cracked. The team then uses state-of-the-art methods and machinery and always uses new high quality hardware and perishable parts (and new motors in the case of Electric Parking Brake (EPB) calipers).
‘Recon & Return’
Shaftec carries all popular references as stock. Subject to rare part availability, ‘Recon & Return’ calipers are returned to the customer within three to five working days:
■ The customer calls with a vehicle registration, or vehicle details.
■ Shaftec arranges UPS collection direct from customer.
■ A production job sheet is prepared.
■ If the company doesn’t hold the kits and pistons as stock, they are ordered immediately so as not to hold up the process.
■ If there is no part number available, the customer is informed that Shaftec will need to see the caliper. This then goes through a specification procedure with a caliper specialist in order to identify the kit and pistons needed.
■ The caliper is high pressure air tested to check for any cracks in the cast. In addition, all threads and sliders are checked.
■ The caliper is then stripped. The piston, seals and bleed screws are removed.
■ The core is shot blasted and chemically cleaned. This strips the core right back to its original state.
“Remanufacturing is not just a poorer substitute for new. It’s a process which results in components that are as good as new, tested as new and which perform in that way for the lifetime of the part.”
■ The caliper is then painted using anti corrosion paint – silver as standard but, for an additional cost, red, green, yellow, blue and black are also on offer.
■ All hand brake mechanisms are checked and repaired if needed.
■ The caliper is rebuilt by hand using new pistons and kits.
■ The caliper will then go through a final pressure testing procedure.
■ The caliper is boxed using anti corrosion packaging and placed on a designated shelf in the warehouse.
■ The production job sheet is returned to the technical team ready for invoicing.
■ The job sheet is then filed for future reference, in the event of a similar request being received.
■ All the customer’s original parts are kept for seven days.