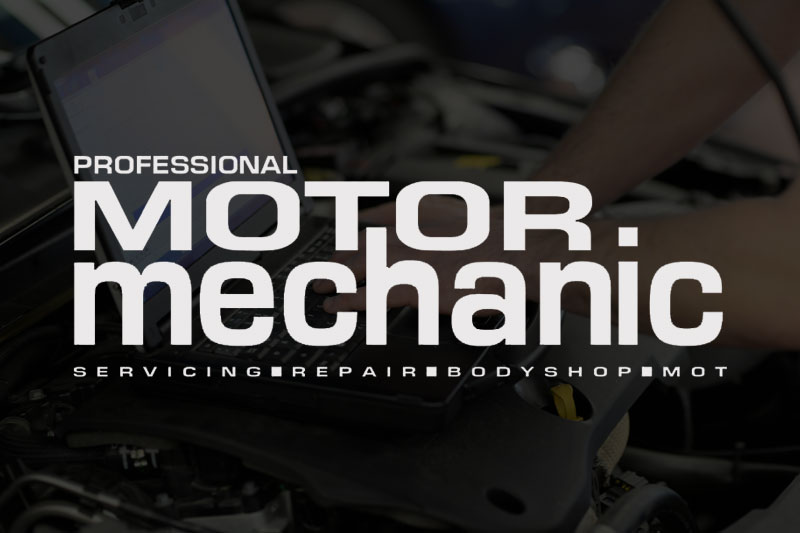
All power assisted steering systems utilise a pump –mechanically or electricallydriven – that pumps hydraulicfluid from the reservoir through some control valves and then back to the reservoir. However, should there be a requirement for the fluid to assist with steering, some of the fluid becomes pressurised to overcome the mechanical resistance directed to the steering rack, whilst the displaced fluid is returned to the reservoir (pictured below).
Fundamental power assisted steering components
As a general rule, the control valve housed within the steering rack or steering box relies on precision engineering for metal-to-metal sealing.
With ever-increasing service intervals and the minimal attention given to power assisted steering system fluids, it is hardly surprising that the hydraulic fluid deteriorates and the system fails. Perusing a widespread independent service reference, the service requirements of hydraulic power assisted systems indicated ‘Power Steering fluid check/top-up’. However, the service requirement for other hydraulically operated systems showed a fluid replacement every 24,000 – 48,000 miles. Some vehicles equipped with power assisted steering did not even mention the power steering on the service.
Power steering fluid
So why is power steering fluid overlooked? Maybe it is because the reservoir is inaccessible (especially when fitted with an electrically driven pump) or because the fluid cannot be readily drained. Some vehicles may never have their power steering fluid changed. What happens to all the contaminants within the system – do they continue to create further friction and material erosion? How many vehicles have a fluid filter? If so, what is the service interval? If you can at least drain the fluid reservoir and replenish, there is a dilution of the contaminants, so that the service life of components can be increased.
Like all fluids used in the automotive industry, hydraulic fluid has some very important roles to fulfil. These could include, amongst others: friction reduction, lubrication and viscosity stability. Therefore, what does the hydraulic fluid do? The fluid choice of the OEM is of utmost importance to ensure faultless operation, operational reliability and long service life. Generally, hydraulic fluids are mineral based, though it is not uncommon to see synthetic and ester based fluids used too. Remember, do not mix the different types, as they frequently use different sealing material technologies and may react with one another.
The primary demands of a hydraulic fluid are:
-
The transfer of the mechanical energy of the pump to hydraulic energy and then reversed to mechanical energy, typically in a cylinder housed within the steering rack, though it could be a rotary actuator in a steering box.
-
Lubrication of moving parts, such as sliding surfaces of pistons and bearings.
-
Protection of the surfaces actually in contact with the hydraulic fluid.
-
Removal of contamination (dirt, water and air).
-
Thermal stability, as the fluid could easily reach 80oC, a critical temperature for hydraulic fluid.
Reviewing these demands, the fluid manufacturer must ensure that the fluid meets these along with secondary considerations.
Viscosity Index and ATFs
Viscosity is a measure of the fluid’s internal resistance to flow, when two adjoining surfaces are moved in opposite directions, and is a technical consideration many professionals consider, mostly with reference to engine and transmission oils.
There are many different viscosity grades of hydraulic fluid. The grading used for engine and gear oils are the SAE and ACEA grades, such as 5w/30 and A3/B3 respectively. However, hydraulic fluids are graded using the ISO-VG system.
Most of the hydraulic lifts and jacks used within vehicle service environments use an ISO32 fluid, though for some heavy duty applications, an ISO46 or ISO68 may be used. There are universal hydraulic fluids available, though they must have a definite viscosity, which is a compromise between the three most popular ISO-VG grades 32, 46 and 68. ISO-VG grades range from ISO10 to ISO200. Various grades are commercially available and ISO/SAE grades can be cross-referenced.
In almost all hydraulic fluids, the viscosity changes with regards to temperature in a linear logarithmic relationship; this is shown in the graph below.
This viscosity – temperature relationship is expressed by the Viscosity Index for the fluid. The higher the Viscosity Index, the wider the temperature range the particular fluid can work within. Viscosity Index can be improved by the use of additives by the manufacturer, however it can also worsen due to heavy loading during the service life and extended drain intervals and poor maintenance.
Automatic Transmission Fluid (ATF) is a common fluid used within power assisted steering systems. If used in its native application, at least it would get a filter and fluid change to mitigate the longevity of the system and its components.
Technician appreciation of the different fluids is imperative, as many different fluids may look the same, i.e. are the same colour, have a similar odour and ‘feel’ the same when rubbed between the fingers. However, the technical data reveals many differences. Traditional ATF Dexron®II and Dexron®III have similar appearances (both red, similar odour), though Dexron®II is a mineral based fluid, whereas Dexron®III is a synthetic based fluid. Similarly, LHM+ – the green mineral based fluid used by Citroën – looks very similar to the Central Hydraulic Fluid (CHF) used by VAG, MAN and BMW amongst others, which is green too. However, the CHF is a fully synthetic fluid which is incompatible with LHM+ and other power steering and ATFs. They have different viscosities too, which will affect the performance of the system.
Useful advice
To ensure maximum service life of power steering systems, ensure that the fluid filler cap and surrounding area is clean before removing it and the replacement fluid bottle cap is clean too. Tell your fluids supplier what vehicle you are working on; don’t automatically order one fluid to suit all, as in modern vehicles it won’t – it is just as critical as having the correct oil for the engine.
Purchase service quantities rather than bulk – supply the remainder of the bottle to the customer for top-up, should they need to. Should you need to change a power steering pipe or rack, ensure that all connections are covered to minimise the ingress of contaminants. When refilling after maintenance work, maintain a suitable fluid reservoir level to minimise air ingress – you would not allow air into a brake circuit and this is just as safety critical.
Finally, inform customers of the need to change their power steering fluid as often as their brake fluid, to mitigate the effects of negligible filtration, oxidation and contamination. Explain that this will prevent further failure of mechanical components within the power assisted steering system when they book their vehicle in for service.