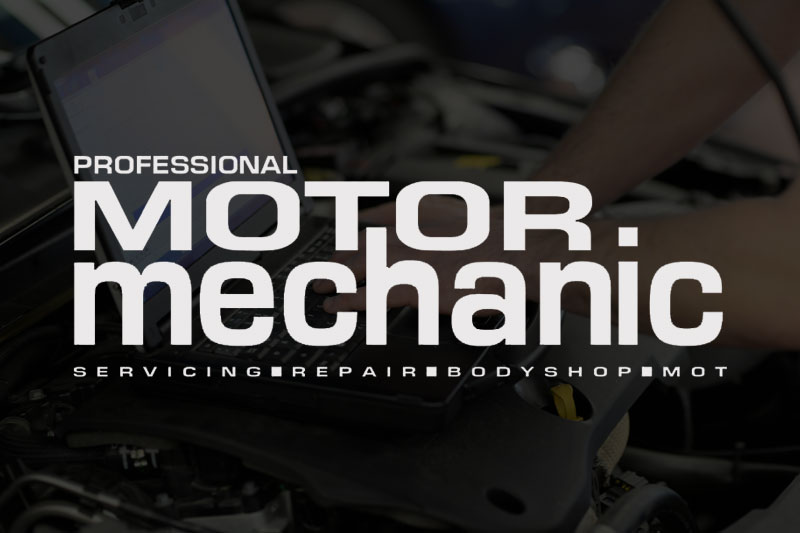
The primary task of the vehicle’s suspension system is to keep the wheels on the road and isolate the chassis of the vehicle from vibrations coming from irregularities and bumps on the road. When the car is in motion, the suspension is exposed to:
- Forces of gravity
- Driving forces – reaction forces resulting from the bumpy roads
- Lateral forces generated during cornering
- Hot and cold temperatures
- Debris
- Water
Suspension parts found on the front axle of the vehicle must allow for the wheels to turn. Over the years, vehicle engineers have developed a number of different solutions for the front axle, including dependent and independent suspension systems. Independent systems have a number of advantages over other types of system and are commonly used by VMs today.
This type of suspension is usually found on the front axle, but many VMs also use it for the rear.
A vehicle’s front axle has three basic types of independent suspension:
1) McPherson struts
2) Double wishbone suspension
3) Multi-link suspension
The latter of these systems is now increasingly utilised by VMs, particularly in the premium segment, where vehicles often have significant weight and develop considerable speed. Users of such cars expect a very high level of comfort and road holding capability.
What does a multi-link suspension consist of?
A typical example of a multi-link suspension is found on the front axle of the VW Passat B5. The basic elements in this system are two pairs of upper control arms (front and rear), two pairs of lower control arms, stub axle, stabiliser, connecting rods, shock absorbers and springs. All control arms are made of light alloys and integrated ball joints.
The mounting points for the control arms at the chassis allow for certain changes to the geometry of the wheel in line with the specifications from the VM. These parts may take the form of a metal bushing vulcanised in rubber, which reduces vibration and noise.
The design of the rear lower arm mount bushing is more complicated. It is a hydraulic bearing, featuring a membrane containing hydraulic fluid. Well-designed metal-rubber bushings enhance the stability of the vehicle when cornering at high speeds and braking.
Failure is more likely
Because it features many more structural components in comparison to other systems, the multi-link suspension has a higher probability of component failure. As such, inspection of individual parts should be made periodically, or when the driver complains about noise coming from the vicinity of the suspension.
Early detection and repair is very important because the individual suspension components work together, and the failure of one component can cause rapid wear on the rest of the system. Furthermore, a broken control arm can result in significant change in geometry, causing deterioration in the car’s handling as well as faster and uneven tyre wear.
While this type of suspension is susceptible to damage from improper use, there are a number of other factors to consider. Some believe there are durability issues for parts within the system; however, this mainly applies to low quality spare parts offered in the aftermarket.
TRW provides a range of high-quality components that will ensure optimum comfort and excellent driving performance for cars that utilise a multi-link suspension.