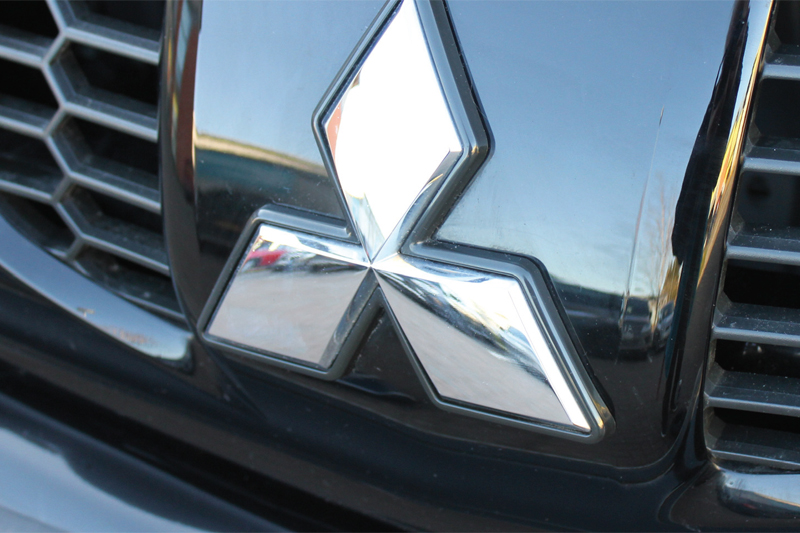
The technical team at Gates explains why technicians should be vigilant when approaching maintenance on Mitsubishi 4D56 diesel engines.
Vehicle information
Engine: Mitsubishi 4D56 Model: Mitsubishi L200 2.5L
The Mitsubishi 4D56 diesel engine has earned a reputation as a reliable workhorse, largely fitted to Mitsubishi L200 2.5L pickups. Unfortunately, many owners have discovered that failure to stick to the maintenance schedules on these engines, especially in relation to the belt drive systems, can be an expensive mistake. The combination of a synchronous drive on the balancer shafts, as well as the hydraulic tension system on the camshaft drive belt, means the maintenance of Mitsubishi 4D56 diesel engines can be a little tricky.
Balancer shaft drive belt
Gates recommends technicians replace the drive belt on the balancer shafts each time the camshaft drive belt is changed.
Should the drive belt on the balancer shafts fail, it is highly likely that debris from the belt will fall down into the camshaft drive. If the camshaft drive belt system is contaminated by this belt debris, premature drive belt failure is likely, which could mean disastrous consequences for the engine.
Camshaft drive belt
In an effort to save money, some car owners will decline the option to replace the hydraulic belt tensioner at a scheduled drive belt replacement. Gates recommends technicians advise their customer that this component should always be replaced with the belt because there is no guarantee that the hydraulic belt tensioner will have a longer life expectancy than the belt.
When installing the tensioner, make sure to remove the locking pin after the pulleys and belt have been installed and note that once removed, a specific procedure must be followed. After removal, manually rotate the crankshaft two turns and make sure that the protrusion of the hydraulic tensioner rod over the housing is within the 2.3 to 7.6mm range.
Time to torque
The tightening torque of the tension roller lever pivot bolt must be within the vehicle manufacturer’s recommended tolerances. These are identified as between 42 to 56Nm.
Insufficient tightening torque will create insufficient clamping force that can cause bending loads on the bolt shaft. This in turn, can lead to fatigue and subsequent fractures of the component. Remember that there’s a washer (see Fig 1) between the pivoting part of the bolt and the engine block; if the bolt is over-tightened, the washer could be deformed.
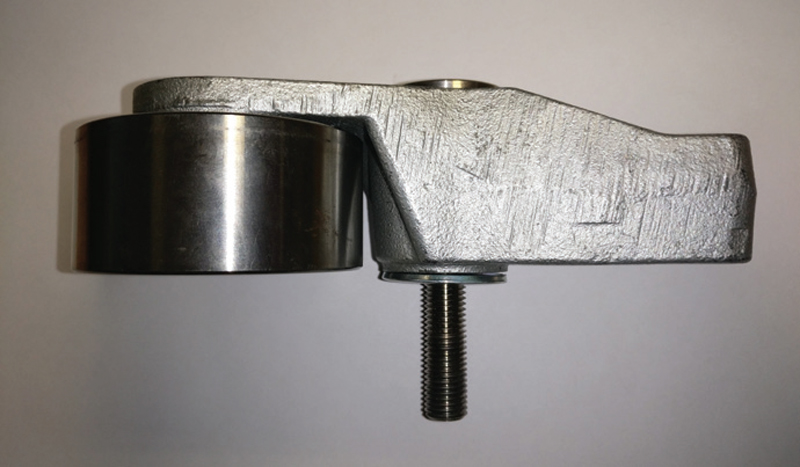
If the washer is deformed, it will come into contact with the end plane of the hole in the pivoting arm of the tensioner lever. This is bad news as it will block rotation. As a consequence, the tensioner will not be able to provide the level of tension that it was designed to produce. As a result, the belt will experience a rapid acceleration of wear. A level typically expected after around 50,000 miles, will be exceeded very much earlier.