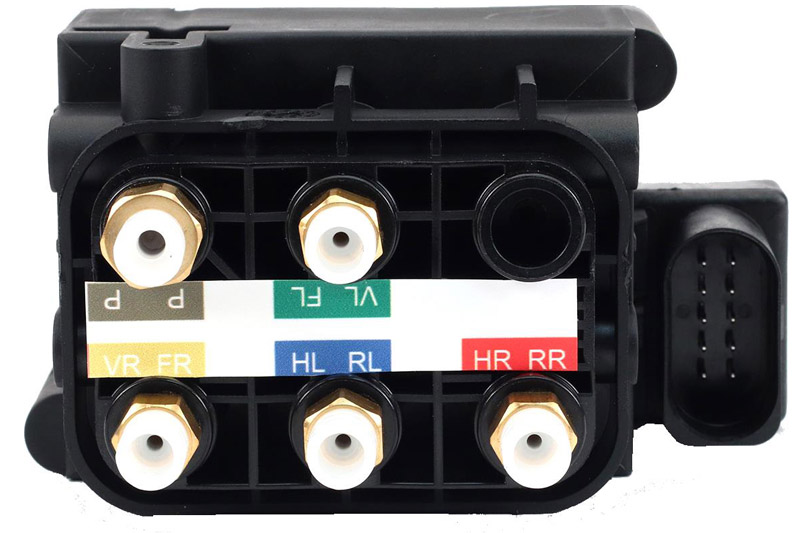
PMM and Arnott take a deeper look at the solenoid valve block – a small but significant component of the air suspension system. Symptoms that seem to point to a leak in an air spring, could also be due to a defect in the valve block.
The valve block takes care of the distribution of pressurised air. A valve block for a four-corner air suspension system with pressure reservoir contains a total of six air connections. One for the air compressor, four for the air springs/struts and one for the pressure reservoir. To avoid making mistakes when installing a new valve block, all connections are colour-coded.
The six solenoid valves inside the valve block are activated by the ECU (Electronic Control Unit). It is a common misconception that the air springs are always directly fed by activation of the air compressor. In most cases, the air bellows are filled through the pressure reservoir. The air compressor pressurises the air in the reservoir up to 15-16 bar, this pressurised air in the reservoir is then used for controlled pressure build-up and as a buffer. The general objective is to use the pressurised air as efficiently as possible, so the compressor runs as little as possible. This prevents overheating and keeps the energy consumption low.
Common Faults
Over time, the solenoid valves in the valve block can become sticky or blocked by small particles that have circulated through the system when operating. For example, when an ageing compressor breaks down, the valve block can consequently become damaged too. Due to overheating, small metal particles can block the solenoid valves and disturb the air distribution. This can result in the vehicle being lower in one or more corners. This symptom could also occur when there is a leak in the air spring. Fortunately, the actual cause can be easily identified by swapping the concerned airline in the valve block. If the valve block is the issue, the problem should then move to another corner and if the problem stays on the same side, it is indeed an air leak.
The valve block is also involved in the release of excessive air pressure. If needed, the solenoid valve towards the air compressor is opened. The pressure is then released through the pressure release valve on the compressor. Thus, in case a vehicle stays “locked” on a certain ride height, first check the functioning of the pressure release valve on the compressor before diagnosing a faulty valve block.
If an air compressor is no longer running, the usual suspect is often the compressor itself or a faulty relay. But it might just be the valve block. The air suspension pressure sensor is located inside the valve block, not in the compressor. If this sensor isn’t working correctly anymore, the signal for activating the compressor stays out and pressure is no longer built up.
If the dryer no longer has the capacity to keep moisture out of the system, the valve block can corrode internally. Additionally, when the outside temperature drops below 0˚, the moisture inside the valve block can freeze, causing it to stop functioning.
One last thing to keep in mind is that normally the airline from the air compressor to the valve block is unpressurised if the compressor is not running. This is done to allow the compressor to start easily. If, for one of the abovementioned reasons, this airline stays pressurised, much more heat builds up each time the compressor is activated. This could lead to a burned-out compressor. So, even though it is small, this significant component of the air suspension system deserves some attention – especially after a compressor replacement.