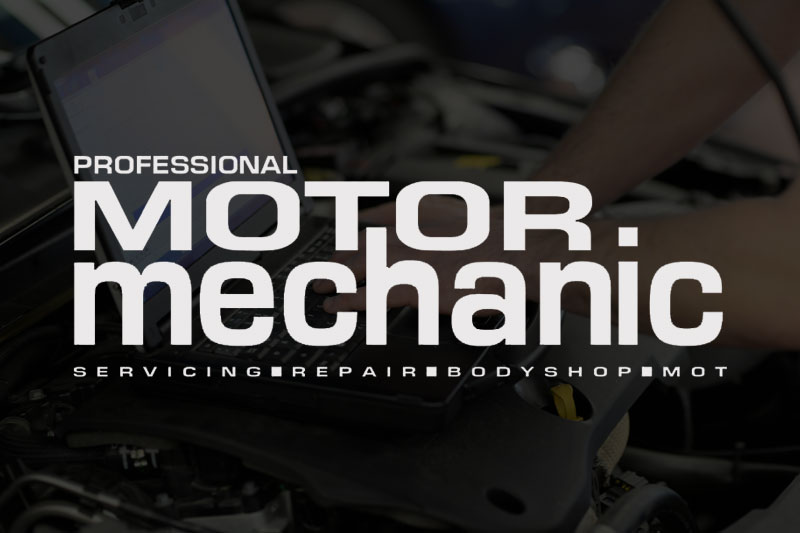
The number of advanced driver assistance systems that process information from cameras and radar systems is growing rapidly. As a result, workshops need to be able to calibrate the vehicle sensors, for instance after accident damage or the replacement of a windscreen.
A diagnostic unit that simply communicates with the control unit in the vehicle is insufficient for this crucial work. Instead it needs to be combined with a device for the calibration of the sensors in the vehicle’s X, Y and Z axis. This calibration is critical to ensure that safety systems such as the ‘intelligent lighting’, Auto Emergency Braking and Lane Departure technology are correctly aligned.
Developed by Hella Gutmann Solutions (HGS), the affordable and universal CSC (Camera & Sensor Calibration) Tool works in conjunction with the company’s range of mega macs diagnostic tools to ensure the correct positioning of the reference panel, in relation to the vehicle’s axis. The mega macs diagnostic tool then communicates with the vehicle’s ECU to perform camera calibration.
“With a little practice, calibration can be completed in less than 20 minutes.”
STEP 1 – Setting up
Implementation varies with each VM, though the initial position is always at the rear axle of the vehicle, together with the diagnostic tool.
Calibration will be explained here and the different calibration procedures can always be adapted quickly and simply.
Before the tool can be aligned with the vehicle, connect the diagnostic equipment to the car. After the vehicle selection you’ll receive step-by-step instructions for that particular model.
STEP 2 – Adjusting the CSC wall
Place the wall in front of the vehicle.
Now place the measuring heads on the front axle.
The distance from the middle of the tyre of the front axle to the reference panel must be adjusted based on the information from the diagnostic tool.
STEP 3 – Adjusting the CSC tool parallel to the vehicle
Place the wheel sensor on the rear wheels and balance it with the level.
Now site the scales on the alignment bar using the laser on the wheel sensor.
Then adjust the CSC tool by moving it to the left and right until both scales have the same value.
STEP 4 – Adjusting the CSC tool centrally in front of the vehicle
Aim the wheel sensor laser at the mirror on the alignment bar so that the laser reflects back to the scales of the wheel sensor.
Then adjust the CSC tool by moving it forwards and backwards.
You should do this until both scales of the wheel sensor have the same value.
STEP 5 – Adjusting the height of the CSC tool
Measure the CSC tool’s height value using the rulers and a zero point adjustment on the back of the frame – it should be measured from the ground up to the mark.
The allocated level specification can be found in the diagnostic tool.
The CSC tool can now be centred using a level and by turning the feet.
STEP 6 – Measuring the level values of the individual wheels
Measure the height of all four wheels – from the edge of the wheel arch to the ground.
Then enter the height (in mm) into the allocated fields in the diagnostic tool and start the calibration process.
The camera control unit will now automatically compare the picture from the entered information to the actual picture. The diagnostic tool then shows the calibration information and will inform you if the calibration has been successful.