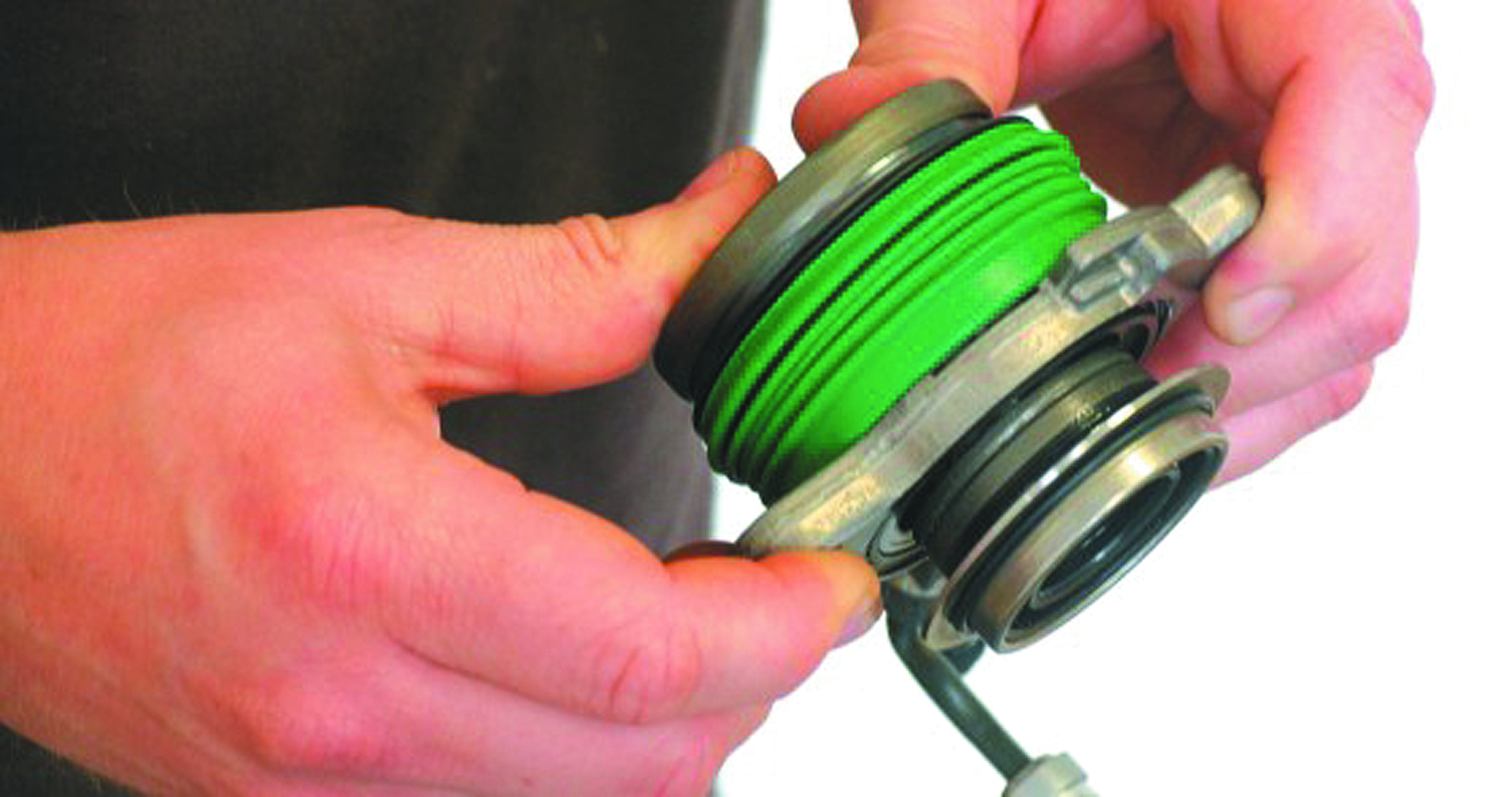
Clutch release bearings: Fault diagnosis and replacement advice.
Despite its apparent functional simplicity, a vehicle clutch is a complex system comprising many individual components, including the release mechanism. On older vehicles this may comprise a separate release bearing and release fork assembly, operated mechanically by cable or hydraulically by an external slave cylinder and push rod. Newer vehicles use a concentric slave cylinder (CSC), in which the bearing and hydraulic cylinder are integrated in a compact unit.
Like the clutch driven plate and pressure plate, the release mechanism is subject to wear, and when damage occurs it can’t be repaired so must be replaced. Renewal of the release bearing or CSC is also recommended when replacing the clutch or removing the transmission, as renewing the clutch in isolation may lead to the need for further repairs shortly afterwards.
At ZF Services we’ve compiled some technical and best practice advice related to common issues associated with release bearings, with tips on how to spot faults. These include:
Grooves on the inner ring of the clutch release bearing
These grooves are the result of abnormal wear (see Fig 1).
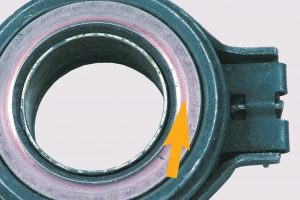
They may be caused by contact with a clutch release bearing that is off-centre due to parallel misalignment of the transmission during refitting, a worn guide tube on the bearing, or by insufficient release bearing preload. The first indication of this fault is often a whistling noise from the clutch.
Heavy wear to the tips of the diaphragm spring
This type of damage (see Fig 2) occurs due to wear in the actuation system, a worn release bearing guide tube or if the release bearing preload is too high.
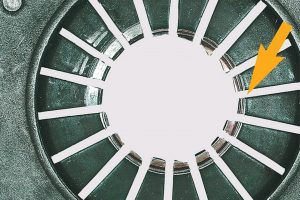
The result can be clutch slip as the high preload prevents full clutch engagement, or loss of clutch operation due to the release bearing becoming jammed or milling completely through the diaphragm spring tips.
Handling and fitting precautions
Maintaining a clean working environment is vitally important during handling and replacement of clutch release bearing components, particularly the CSC. Any dirt deposits on the outside of the CSC piston guide can damage the sealing lip, as the piston will pass over the particles when it returns to its non-extended position.
Installation errors can also cause CSC defects. When removing the clutch and transmission with a closed hydraulic circuit, the clutch pedal must not be operated. Should this occur, it will over-extend the CSC piston, possibly damaging the piston sealing lip, causing hydraulic fluid loss and resulting in clutch operating problems.
The natural temptation to manually compress the CSC to ‘check’ its operation should be resisted, as this can result in seal damage (see Fig 3).
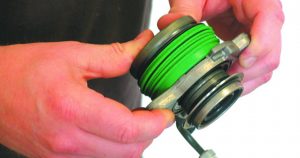
The application of lubricants must also be avoided; these may cause the seals to swell and lead to early CSC failure.
CSC filling and bleeding
With the clutch fitted, the CSC installed in the clutch bell housing and the transmission fully mounted to the engine flange, only then should the CSC be filled with hydraulic fluid and bled, observing the VM or CSC manufacturer’s instructions.
Careful attention to the aforementioned recommendations should enable rapid tracing and rectification of faults and ensure long and reliable operation of replacement components.