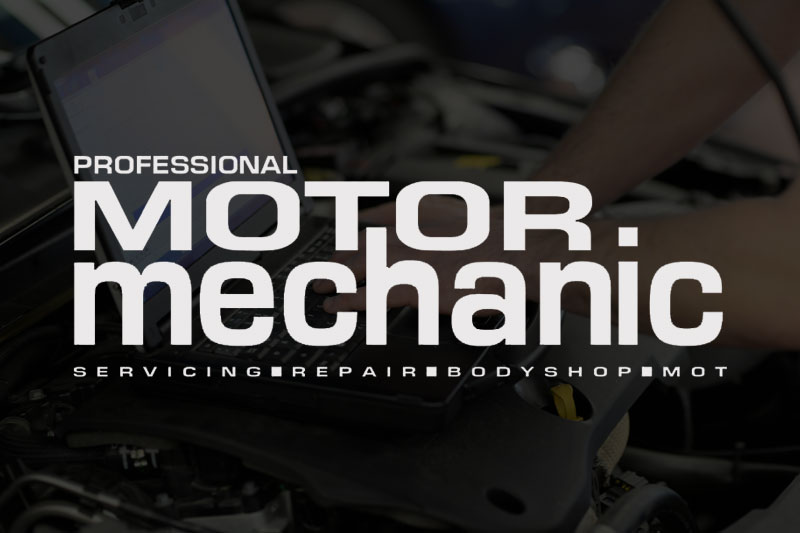
Since 1998, Volkswagen, Audi, Seat and Skoda diesel vehicles have been equipped with variable geometry turbochargers. Other manufacturers followed suit and the majority of diesels manufactured today use variable van technology, including Transits, Sprinters, Crafters and similar sized vans.
Whilst these units are far more efficient, they are prone to carbon build-up on the variable vane mechanism, resulting in restricted movement and causing either ‘under-boost’ or ‘over-boost’. This, in turn, causes the vehicle to be underpowered and eventually ends up triggering the engine management light, generating fault codes and the vehicle moving in to ‘limp mode’.
To overcome this problem, the turbo traditionally had to be removed, stripped, cleaned or replaced at a considerable cost to the owner; however, there is now a very effective alternative method in the form of ‘Revive’.
The product is a safe, water-based, non-toxic and non-flammable fluid, using technology developed and used for the cleaning and maintenance of aviation jet engines, power station turbines, large marine diesel engines and now automotive engines.
Combustion process
The fluid is simply sprayed into the vehicle’s intake system before the turbo inlet whilst the engine is running. As the Revive fluid passes through the combustion process, it locks on to built-up oily/carbon deposits and breaks away a surface layer. These tiny carbonised particles are then carried away and out through the exhaust system.
Revive is extremely effective at cleaning carbon deposits from petrol and diesel engines and especially variable vane turbochargers; however, it can expose mechanical wear issues that have previously been masked by the carbon build up, so this needs to be considered when diagnosing the problem.
By performing three Revive cleaning doses on the vehicle, carbonised layers are removed gradually, making the engine cleaning process very safe.
Three easy steps in just 10 minutes!
Step 1
Starting with a cold engine, unclip the intake trunking after the air filter.
Step 2
Spray Revive in three doses of 250ml into the intake, first with the engine running at 2,200 RPM, next at 1,800 RPM, then stop the engine for approximately 3-4 minutes. During this time, if the vehicle is fitted with a vacuum-operated turbo actuator, a vacuum pump tool could be used to agitate the mechanism before administering the final dose. The engine should then be run at 2,000 RPM until the third and final quantity has been applied. Keep the engine running for a few more minutes until Revive has passed through the system.
Step 3
Take the vehicle for a brisk drive of about 20 minutes; this allows Revive to do its work. The Revive cleaning process can be performed before a service, allowing the vehicle to be checked over and filled with clean oil.