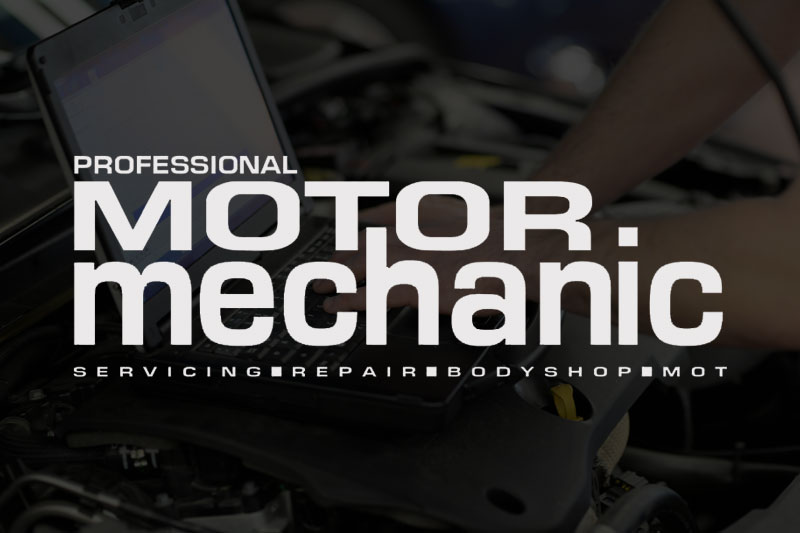
There are two types of EPB system design that are in use: the first is the ‘cable puller system’, and the second is the ‘calliper type’ system, which we’ll outline here.
Calliper type
The calliper type uses an electric motor and a two stage reduction gear. Two pulleys and a toothed belt provide the first reduction of 3:1 and a swash plate gear provides a second reduction of 50:1.
The swash plate has 51 teeth and is prevented from turning by the lugs located in grooves in the calliper body. As the drive gear makes one turn, the swash plate oscillates moving from position 1 to 2 and back again (see pic below). The output gear has only 50 teeth and because in one oscillation the 51 teeth of the swash plate mesh with the output gear, the output gear must move around one tooth pitch to compensate. This gives a 50:1 drive ratio.
The swash plate reduction gear drives a threaded spindle which in turn winds the thrust nut in (or out, dependent on direction of the motor) which is located inside the calliper piston; applying the brake. Hydraulic operation is unaffected. This 150:1 reduction ratio (compounded) means that the internal friction in the drive mechanism prevents the system from reversing and releasing the brake. The piston remains locked after actuation and is only unlocked when the motor is reversed electrically. The current draw of the electric motor is measured by the control unit and when the current draw exceeds a certain value, the control unit switches off the current supply to the electric motor. This effectively limits the calliper clamping force.
The images below show the mechanism in position 1 (centre image) and position 2 (far, right).
Functionality of the system
It is easy to see that the parking brake can be applied and released by just using a switch on the control panel but some of the functions of the parking brake require much more control than just ‘on-off’. The system programmers had to think of all the possible uses (and misuses) of the system.
Applying the brake
This can be done at any time with the ignition ‘on’ or ‘off’ by pushing the EPB button.
Emergency stop (calliper type)
If the vehicle is travelling at more than 7km/h and the EPB button is pressed and held, the
system activates the Electronic Stability Programme which applies the hydraulic brakes to bring the vehicle to a controlled halt. The brake is released when the button is released. If the vehicle is travelling at less than 7 km/h when the button is pressed then the EPB is applied. This type of control and functionality cannot be achieved with a conventional parking brake, you pull the lever at speed, the braked wheels can lock and control could be lost (the author recalls a time when his front seat passenger pulled himself upright in his seat by grabbing the nearest convenient lever……..)
Releasing the brake
This can only be done with the ignition switched on, the footbrake applied and the EPB button pressed (some manufacturers have a pull mechanism for the driver).
Drive away release
The brake will automatically release when you drive off. To do this correctly, certain conditions have to be analysed:
1. Gradient
This is provided by the longitudinal acceleration sensor which is part of the ESP/VSC control system.
2. Clutch position
The clutch is fitted with a sensor which provides information about the operating position of the clutch. It is used for the ‘automatic hill start’ function and also provides information for cruise control and engine fuelling during gear changes.
3. Engine torque
This is a calculated value provided by the engine control unit.
4. Direction
Information on forward or reverse gear selection is provided by the reversing light switch.
Roll back is prevented by the system not releasing the EPB until the torque applied to the driving wheels is sufficient to propel the vehicle. The system uses the Controller Area Network (CAN-BUS) for the receipt and transmission of necessary information.
Auto hold
This uses the ESP control valves to retain hydraulic braking pressure. When the vehicle is brought to rest using the footbrake, braking pressure is retained (regardless of brake pedal position) until the accelerator pedal is pressed.
Summary
So, it can be seen that these systems, although comparatively complex (when compared to a conventionally applied system), provide significant advantages to the driver.
After more technical advice? Click here to view the third part of this series