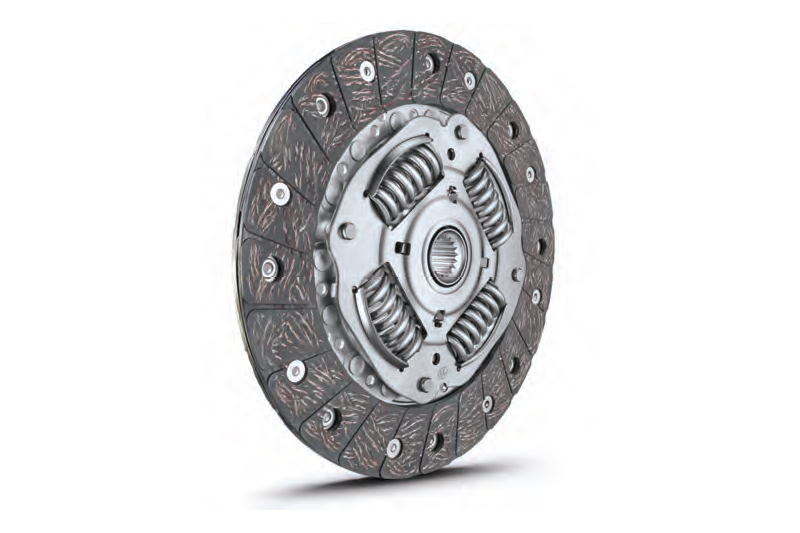
Schaeffler investigates dual mass flywheels (DMF) and how they affect modern vehicles.
Let’s start with a basic question, why do we need a DMF? Quite simply, it is designed to absorb the torsional vibration/power pulses from the crankshaft to give smooth rotation to the transmission. When the engine is running, the crankshaft rotates in pulses, meaning it speeds up and slows down during the compression and power strokes. These pulses are more pronounced at lower engine revs, and with today’s challenges of lowering vehicle emissions the trend is to run engines at lower speeds (less fuel in equals less emissions out).
DMFs were introduced in the mid-eighties when diesel engines started to become popular and we also started to see turbos introduced into both diesel and petrol applications. These engines produced stronger power pulses, requiring extra vibration absorption that could not be obtained by a dampened clutch plate (Fig.1).
A standard dampened clutch plate has about 18° of rotational damping compared to a DMF with over 100° of rotational damping – 50° in each direction. In some applications this can be up to 180°, which means the DMF can cope with higher compression ratios in smaller engines that are more efficient at a lower engine rpm, reducing engine emissions whilst maintaining a smooth operation and improved drivability.
What’s inside a DMF?
As we can see in Fig.2, there is a primary flywheel (2) that bolts directly onto the crankshaft, which also carries the ring gear (1) for the starter motor. Inside the primary flywheel we have arc springs (3) which are matched to the different power pulses of the engine, absorbing the torsional vibration before pushing against the flange (5), which is riveted to the secondary flywheel (8). The arc springs are injected with grease to lubricate them during compression and expansion, and the primary flywheel is sealed by the primary cover (7).
In 2008, the DMF technologically evolved further with the introduction of a centrifugal pendulum absorber (CPA) to the drive flange (Fig.3). This feature was developed to cope with engines getting lighter, inherently absorbing less vibration, with the CPA further counteracting any vibration giving an even smoother path of transmission. Another advantage was that that the engine could be driven at an even lower rpm, helping to further reduce emissions and fuel consumption. CPA equipped DMFs are generally fitted to more premium brand vehicles such as BMW, Audi and Mercedes Benz, and when this type of DMF is removed from the gearbox, the pendulum weights can often be heard rattling inside, as they need to move freely which indicates correct operation. When the vehicle is started the centrifugal forces push the CPA into position and the noise disappears. Schaeffler also now uses CPA technology on dampened clutch plates mated to solid flywheels in some applications.
Another internal component that has been added is the friction control plate (Fig.4), which supports the arc springs in high load situations, such as stop/start applications when the arc springs are subjected to high torque, by giving additional resistance to rotate. This can be felt as a hard stop when rotating the secondary mass if rotational free play is being measured.
The latest DMF evolution remains a proven technology that is very much a key component in the latest popular hybrid vehicles on our roads, as they still feature an internal combustion engine. Miniaturised DMF technology is also used inside the pulley decoupler (Fig.5) on the auxiliary belt drive system, to absorb torsional pulses and thus protect all associated drive system components. It is always advisable to test a DMF when replacing a clutch to determine if it is within its operational parameters or if it requires replacing. The two tests that should be carried out are for rotational ‘free play’, which indicates the condition of the arc springs, and ‘rock’, which indicates the wear on the centre bearing (Fig.4). The recommended tolerances for both tests plus further instructions and information can be found on the REPXPERT app or online knowledge portal.
What can cause premature wear to a DMF?
- Engine misfires/cylinder imbalance/poor compressions introduces greater vibrations/pulses, causing the arc springs to work harder thus reducing their service life
- Overloading extra load gets transmitted through the arc spring, over-compressing the arc springs
- Chip tuning increasing power above the original engineering specifications can over-compress the arc springs, leading to increased power pulses and wear rate
- Misalignment between the engine and gearbox will put a side/lateral force on the centre bearing/bush causing the bush to wear/fail prematurely
- Thermal overload where the clutch has been slipping and additional heat has been generated, potentially affecting the arc springs and grease