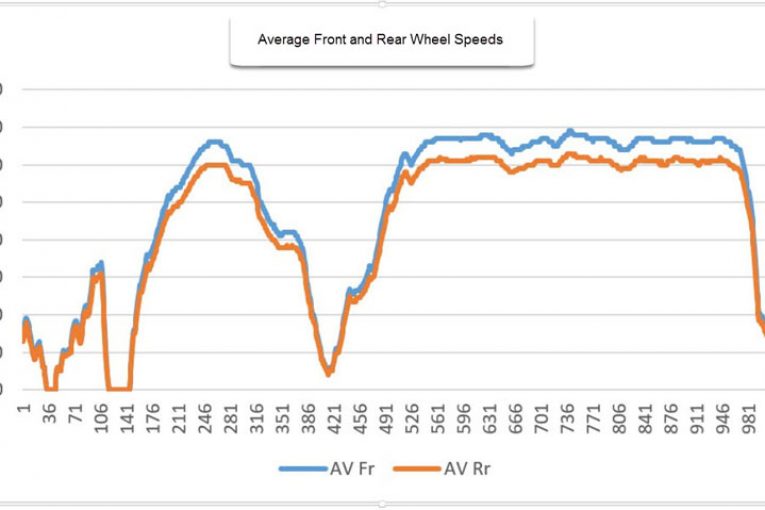
Pico Technology look at a case study of a faulty ABS operation on a 2005 Subaru Legacy SE.
Problem
There was a noise from under the bonnet when driving at low speed over speed humps, accompanied by the ABS warning light. During initial testing, it was noted that the noise came from the ABS pump and happened when the rear road wheels travelled over speed humps (5-10mph). It was revealed that the vehicle had been purchased recently. The rear right wheel bearing had been replaced due to excessive bearing noise.
Diagnosis
The basic inspection highlighted no areas of concern. All relevant ABS components appeared to be original, undisturbed and secure.
Tyre wear, brand, orientation, condition and pressure were inspected and confirmed to be correct. The wheel/tyre configuration and dimensions were also confirmed. This is important as the ABS controller monitors the rate of acceleration and deceleration of wheel speeds to determine if brake pressure intervention is required. A vehicle scan confirmed a single ABS fault code, ‘C0115 – Wheel Speed Sensor’. Available VM service data then confirmed that there were no relevant outstanding issues.
Serial live data evaluation was used to monitor the rear wheel speeds, while driving over speed humps at low speeds. There appeared to be a discrepancy between the rear wheel speeds at different time intervals. In order to qualify the serial data, a frequency math channel was created to graph the frequency of each wheel speed sensor.
This displayed a sudden drop in frequency when the rear wheels rolled over speed humps (15Hz frequency drop within 30ms). The front wheels’ frequency decreased progressively. This drop would definitely trigger the ABS. The wheel speed signals displayed noise immediately after the drop in rear wheel frequency but not before. As the ABS wheel speed sensors were recording wheel speeds, the wheel speed signal noise was then considered.
Results
As the noise was only apparent during ABS operation, the voltage and current to the ABS pump was inspected.
The pump current peaked at 80A, while the ABS sensor supply voltage fell to 10V. The ABS sensor speed signal current was also measured, to reveal minimal noise and zero distortion, unlike the speed signal voltage.
A cause was difficult to establish, marking the point at which the Pico Auto Forum was consulted. After numerous discussions, new information came to light – the ABS operation.
The EMI/noise in the wheel speed voltage signal was a consequence of high frequency switching by the ABS solenoids, causing momentary collapse of a magnetic field in close proximity to the power/ground supplies of the wheel speed sensors.
Knowing that the noise appears after the reduction in wheel speed and that it was not present in the wheel speed current signal, the actual wheel speeds were investigated.
The vehicle was driven, with the fault code erased, at high speed to record wheel speeds. While maintaining a speed of 70mph, the ABS warning lamp came on, the cruise control disengaged and the fault code returned. Fig 1 plots the average front and rear wheel speeds during the road test: a considerable difference between front and rear.
It was worth counting the number of teeth on the ABS pick-up rings (front and rear). In Fig 2, you can see the different pole count between front and rear (waveforms above), which explained the differing wheel speeds and the inadvertent ABS operation.
But which wheel had the incorrect pole count? An optical test from a donor vehicle showed that the pole count on both the front and rear ABS was 48. The customer had mentioned that a wheel bearing had been replaced. They had, however, purchased the full set of four wheel bearing/hub assemblies.
By using the Magnetic Field Finder, it was possible to confirm 44 teeth on the remaining assemblies in the set. Had all four wheel bearings been replaced, there would not have been an ABS fault, but a speedometer error of around 10%.
Armed with this information, the rear wheel bearing/hub assemblies were replaced again.