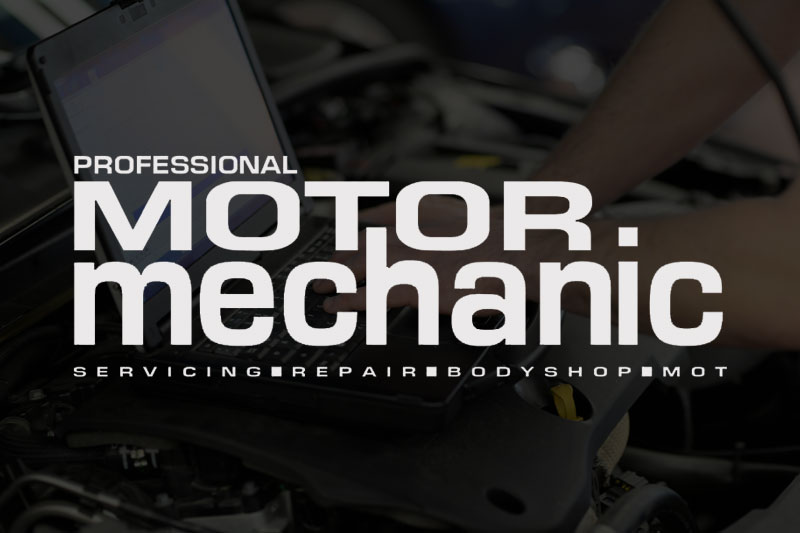
In order to meet strict Euro 4/5 emission limits, modern diesels have to reduce gaseous and particulate emissions. To do this, they use a particulate filter. There are two main types of diesel particulate filter (DPF): aDPF and cDPF.
How they work
The aDPF is used by Ford, Volvo, and Peugeot/Citroën. It uses an additive to help the regeneration process take place, giving the advantage of working at a lower temperature but the disadvantage of needing to be replaced at around 75k miles as a service item due to the additive used.
The cDPF is used by Jaguar, Land Rover, Audi, BMW and Mercedes-Benz. It uses a coated catalyst type DPF, giving the advantage of lasting longer (around 150k miles) as there is no additive to help regeneration but the disadvantage is that it runs at a hotter temperature.
The particulate filter uses new filter technology based on a combined filter and oxidation catalytic converters to store and, when the conditions are right, destroy the particulates.
The exhaust gases pass through the filter leaving the particulates behind that are too big to pass through the filter’s pores. As the filter fills with particulates, the engine management will access this and carry out a regeneration of the particulate filter to stop it blocking.
The engine management monitors the volume of the particulate in the filter by measuring the pressure in a pipeline before and after the particulate filter.
As the exhaust gas flows through the filter and the amount of particulate increases, the pressure difference will increase. This will lead to a change in signal voltage from the pressure sensor. This signal is one of the parameters required before the regeneration of the filter can take place. The particulate filter has two types of regeneration: passive and active.
Passive regeneration
This requires no special intervention from the engine management and occurs during normal engine operation. It involves a slow conversion of the particulate matter into carbon dioxide, becoming active when the DPF temperature reaches 250˚C (482˚F) and a continuous vehicle speed of above 40 mph is maintained.
During passive regeneration, only a portion of the particulate is converted into carbon dioxide. This is due to the chemical reaction process which is only effective within the normal operating temperature range of 250 – 500˚C (482 – 932˚F). Above this temperature range the conversion rate of particulate into carbon dioxide is increased. Higher temperatures can only be achieved using the active regeneration process.
Active regeneration
This generally occurs every 450 miles (725km) – although this is dependent on how the vehicle is driven. For example, if a car is driven at low speed in urban traffic, active regeneration will occur more often than for motorway high speed driving when passive regeneration will occur. This is due to greater particulate build up at lower speed. The DPF control software incorporates a mileage trigger, used as a back-up for active regeneration should it not start because of filter pressure.
Active regeneration of the filter starts when the temperature is high enough to burn the particles. The filter temperature is increased by introducing post injection of fuel after normal operations have occurred. Depending on the filter temperature, the DPF software requests either one or two post injections of fuel.
The first post injection of fuel retards the combustion inside the cylinder which increases the temperature of the exhaust gas.
The second post injection of fuel is injected late in the power stroke cycle. The fuel partly combusts in the cylinder but some un-burnt fuel also passes into the exhaust where it creates an exothermic event in the filter, further raising the diesel particulate filter temperature.
The active regeneration process takes around 20 minutes to complete. The first phase increases the filter temperature to 500˚C while the second phase increases it to 600˚C – the optimum particle combustion temperature. Temperature is maintained for 15-20 minutes to ensure complete incineration of the particles within the filter.
The regeneration temperature of the filter is monitored by the DPF software to maintain the optimum temperature and to ensure the temperature does not exceed the operational limits of the turbocharger. If the regeneration process can’t take place due to vehicle usage or driving style, certain diagnostic equipment such as Autologic can force a regeneration to take place.
These screen shots show the forced regeneration in progress (above) and completed (below).
The ‘forced’ regeneration process
To force a regeneration to take place using the Autologic select “DPF FUNCTIONS” and then select “DIESEL PARTICULATE FILTER REGENERATION”. After this option has been chosen, on screen instructions are displayed for the technician to follow with the procedure usually taking around 30 minutes to complete.
MAKE SURE YOU CHECK THE OIL!
As a warning, if the owner only carries out short journeys and the vehicle never completes the regeneration cycle, it could cause the condition of the oil to become very poor due to the fuel passing into the oil. If this continues it could then cause the car to run away or start to run on its own oil which will usually end in destruction of the engine. Therefore the first check on any DPF-utilising vehicle arriving in your garage should be the oil level and condition.