Nissens offers best practice tips for avoiding damage to the compressor.
Additives are vital to the performance of the compressor. Without oil, the compressor will cease to perform, and UV dye is essential when it comes to detecting leaks or cracks in the system. But additives are only beneficial as long as they are kept under control. Nissens highlights an often- underestimated issue – the overuse of additives, which is slowly damaging compressors.
As a manufacturer of air conditioning compressors, and an expert within the field of climate solutions, Nissens is calling for increased awareness when it comes to additives. According to the company, the lack of focus on the liquid supplements can lead to serious consequences for mechanics and car owners.
Nissens’ Communication Manager, Jacob W. Smedegaard, explains: “Extensive use of additives can cause serious harm to a compressor. It is recommended that UV dye should never exceed 5% of the liquid mixture in the compressor. Extended use of UV dye, combined with the presence of flushing liquid/alcohol, reduces the viscosity of the oil considerably and can lead to blocked pistons. Adding too much lubricant-based UV agent will increase the pressure in the system, exposing the compressor to a higher load, which in the end can cause it to fail.”
It is essential that the root of the problem is found – and that it is corrected. Misinterpreting the signals from the system can prolong the issues, causing additional stress on the system that could have been prevented.
“We have seen many cases where the process could have been simplified, had the system been diagnosed correctly from the start”, states Jacob W. Smedegaard. “An example of this is flux. We have seen cases where flux has been accused of being the root of the problem. However, in modern, high-end manufacturing processes, it is impossible for flux to enter the system. These issues are, in 99% of the cases, found to be caused by either too much UV agent, leak-stop contamination or remains of flushing agents in the system. If a leak sealant is to be used, it should be a non- polymerising type that cannot form solids. If mechanics are aware of this, they can take the necessary precautions, and in the end give a better service to the car owners.”
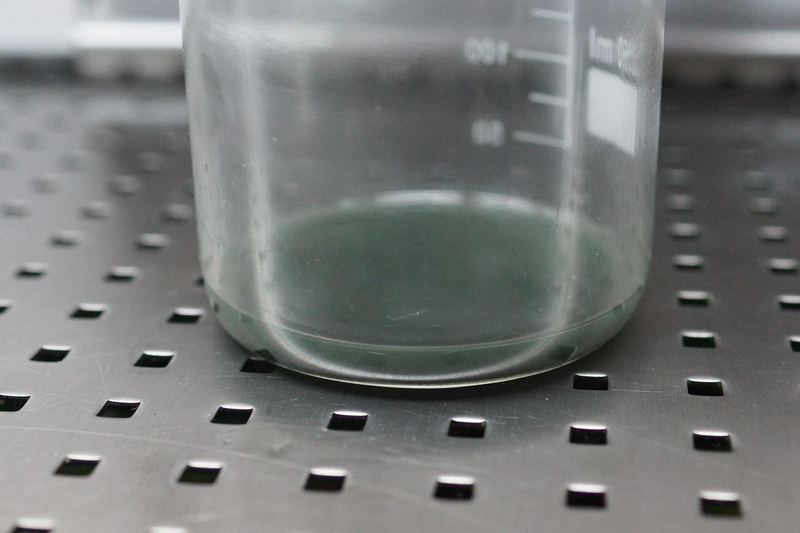
How to avoid damaging the compressor with additives
When the originally applied oil is mixed with another substance, it can affect the structure and composition of the oil film, thereby weakening its lubricative abilities. This will impair the compressor’s performance and shorten its lifespan. A lubricant that is not optimised to the compressor specifications can lead to overheating, friction, and seizure in the compressor. In a gravimetric purity analysis, the particle contents must not exceed 200mg/m2 (milligrams per inside surface area). The diameter of the largest particle must not exceed 1mm.
Therefore, it is of vast importance to always follow the compressor manufacturer’s installation instructions to ensure proper lubrication. Always apply the lubricant type and volume required by the compressor manufacturer. When using a UV dye agent, leak-stop agents, or system flushing solution, always follow instructions strictly. System service procedures like flushing, drying or vacuuming require great attention to detail, following every step carefully and in the correct order.
Common causes of damage:
Too much UV agent
Using an excessive amount of detergent-based UV agent will dilute the oil. This will result in an incorrect viscosity and density of the oil, resulting in poor lubrication and leading to compressor failure. Adding too much lubricant-based UV agent will increase the pressure in the system, exposing the compressor to a higher load. The amount of UV dye used should never exceed 5% of the total volume of the oil.
Flushing agent residues in the system
Flushing agent residues in the circuit will significantly impair the oil’s lubricative abilities. Furthermore, it can deteriorate the Teflon coating in the compressor, causing particles to peel off and clog the system. After flushing, nitrogen must always be used to remove the flushing agent remains and to effectively dry the circuit.
Leak-stop contamination
Improper evacuation of the vacuum will leave moisture in the compressor system. As some leak-stop agents work by crystallising moisture in leakage areas, a poorly vacuumed system will experience extensive crystallisation. This will cause contamination inside the circuit, reduce the lubricative abilities of the oil, and eventually cause compression seizure. It is not wrong to use additives, but improper use can result in further problems.