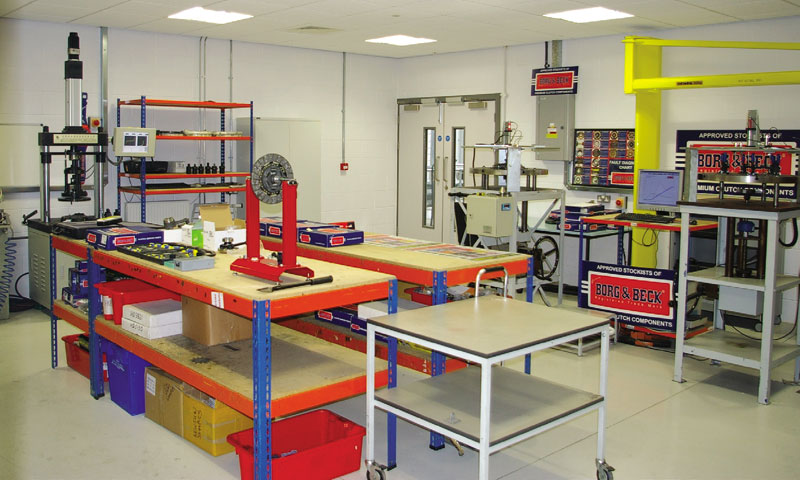
Technicians need to be confident in the quality of all the products they install, but because of the demands on the system and time now required to fit a replacement, clutches in particular need to be of the very highest quality.
Quality is the foundation principle for the First Line Group and its Borg & Beck Clutch programme, which is why it has invested in a testing facility to ensure this is guaranteed across the range.
Housed in its Banbury HQ, the facility enables the Borg & Beck Clutch team to manage the whole process of quality control, testing and warranty management. Not only are all components checked against OE specification and tested to carry out prolonged performance trials, the facility also enables the team to subjectively analyse any warranty claims and diagnose faults, meaning claims can be resolved in an optimum time.
Using an assortment of specialist rigs, the team is able to carry out a wide variety of product tests, including clutch cover assembly loads and releasing movements, the torsional load/vibration and cushion deflection curve of drive plates, the static assessment of dual mass flywheels (DMF) and the performance and durability of concentric slave cylinders (CSCs). Once completed, each test is accompanied by a detailed test report.
Common installation errors
The test facility has enabled the Borg & Beck team to identify several errors that can be avoided when it comes to clutch installations, but alignment related issues are fast becoming among the most common.
The consequences of not aligning the input shaft correctly when reattaching the gearbox back onto the engine are very evident and will lead to symptoms such as clutch judder, drag or, in the worst case scenario, the total loss of drive to the transmission.
The results of inspecting misaligned clutch components reveal that what can tend to happen as the gearbox is being offered up to the engine, is difficulty in locating the splines on the input shaft into the corresponding splines on the drive plate. Some technicians have even admitted to resorting to using long bolts between the gearbox housing and engine, to force the two surfaces together. This practice should never be undertaken as it can cause significant damage, not just to the input shaft and/or drive plate, but also to other interrelated clutch components.
Another common cause of misalignment occurs when a technician does not use a suitable stand or support when guiding the gearbox into position. If the gearbox input shaft has only been partially inserted through the new clutch drive plate and then is ‘hung’, because the stand is dropped before the gearbox is mated to the back of the engine and at least some of the securing bolts fastened, then damage to the drive plate and/or input shaft is highly likely to occur.
Both of these misalignment issues can be easily avoided with a little sensible preparation and by following the correct installation procedures as set out by the vehicle manufacturers and available through reputable technical service data providers such as TecRMI.