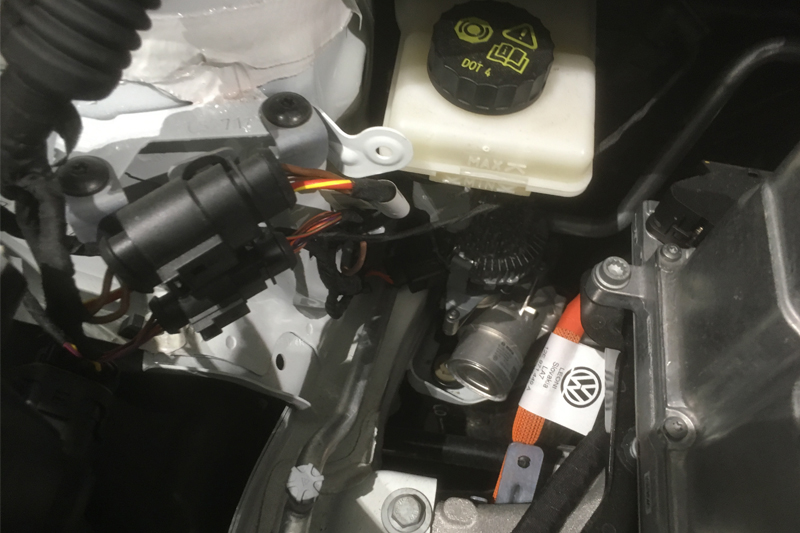
HEVRA’s Pete Melville continues his series of articles focusing on hybrid and electric vehicles, as he turns his attention to braking systems.
In the last article we looked at some of the high-voltage components that make up an electric or hybrid car. Now we’re going to look at some of the other differences between these cars and their more traditional cousins, starting with the braking system.
There are two challenges here, and the first is brake assistance. Brake assistance on traditional petrol engines came from the suction of the inlet manifold, and on diesels and some of the more modern petrols, a mechanical vacuum pump driven by the engine. Both of these need a constantly running engine to operate, whereas our hybrid engine runs as and when needed, and our EV has done away with it altogether.
The other issue is regenerative braking – if we can use the motor to slow the car, this is our preference. Regenerative braking gives us free fuel, and doesn’t wear out our brake pads or create dust emissions. However, we can’t pump energy into the battery if it is already full. Regenerative braking also doesn’t always work well at very low speeds, and of course we need to be able to stop the car in the event of a problem. We also need friction brakes for ESP functions, where the brakes are carefully applied to one or more wheels to keep the vehicle in the desired direction (if a difference between the steering angle and the yaw rate is detected).
So, we need a system that can provide brake assistance, whilst also providing a means of splitting the brake force between the motor and the friction brakes. As with a lot of hybrid and EV technologies, different manufacturers each have their own way of doing things.
Toyota, for example, completely separates the brake pedal from the braking system. When you push the pedal, you are simply pushing against a stroke simulator – a hydraulic device which makes the pedal feel as though it is connected to something. The car measures the brake pedal travel, and calculates the desired braking force. It then calculates how much can be done by the motor, and how much by the friction brakes, and if the friction brakes are needed, pressurised fluid is diverted from an accumulator to the calipers. The accumulator is kept full of pressurised fluid by an electric pump. There is no need for additional brake assistance. In the event of a total electrical failure, a unit in the rear of the car supplies emergency power to the braking system, and if this fails, or a different type of fault develops, valves spring open that connect the pedal to the front wheel calipers.
Nissan uses a similar principle, but the brake pressure is generated on demand, rather than being stored and used when required. The master cylinder’s internals can be moved by an electric motor, providing brake assistance, and can be moved away to allow for regeneration (a stroke simulator takes up the slack to ensure pedal feel).
Some other manufacturers, such as BMW and Tesla, use a more traditional system, although of course the vacuum pump is electric. Pedal position sensors are still used in order to monitor driver braking demand. On hybrid cars, a mechanical vacuum pump or manifold suction is sometimes used in conjunction with an electric pump, and a pressure sensor ensures sufficient vacuum is generated. Volkswagen does away with the vacuum system, preferring an electromechanical brake servo.
So what do these systems mean for us repairing cars? The systems are generally reliable and you’ll only need to understand the inner workings in order to diagnose a problem. However, routine service work becomes a more complex task, with each different system having a particular procedure for bleeding the brake fluid, and with some systems not connecting the pedal to the wheels, a firm pedal doesn’t mean the system is air-free.
When it comes to replacing brake pads, most systems are straightforward, although it’s worth putting the car onto its lowest regenerative brake setting and bedding the pads in during a road test before returning the car to the customer. In the event of a vacuum pump failure, it’s important to check whether the pump could have ingested liquid or dirt to prevent a repeat failure.
Because the friction brakes are used as the secondary braking system, they tend not to wear out at anything like the rate of those fitted to traditional vehicles, so you may find most of your brake repair work becomes removing corrosion rather than replacing worn parts. The most important thing, as with everything in this trade, is to understand the system you are working on, and ensure the correct procedures are followed.