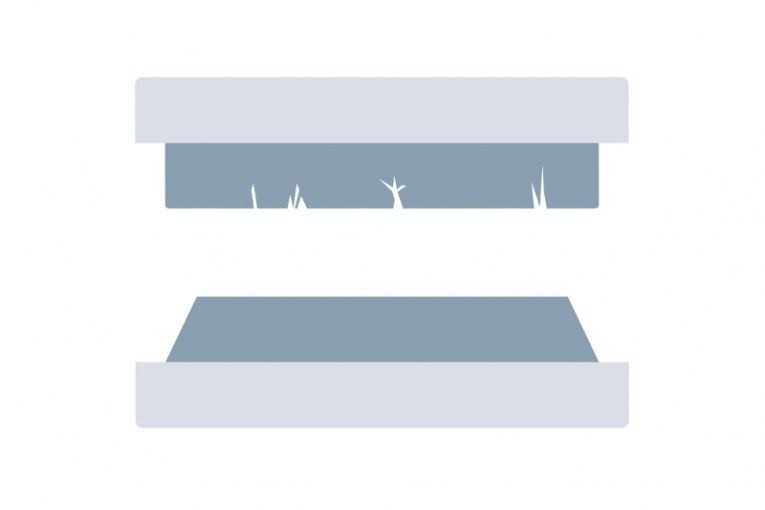
The ability to distinguish between different types of brake pad wear is an important skill for technicians. It helps pinpoint possible causes and streamlines diagnosis, saving you and your customer time and money, and ensures a more accurate repair. Here, brake manufacturer Delphi Technologies provides a useful guide to types of wear, causes, basic remedial actions, and more in-depth installation advice.
Even Wear:
Although your customers might not agree, even wear across both the inside and outside pads on each wheel is positive – it shows that the brake system has been functioning correctly. In this instance, replace the pads and hardware and service the caliper guide pins and slides.
Outer Pad Wear:
If the outside pad is worn more than the inside one, the mounting hardware is causing the caliper to seize. Consequently, the caliper will not be able to fully retract the pad from the disc, creating friction even when the brakes aren’t applied. This type of wear is typically caused by seized sliders, guide pins and dry bolts and can be corrected by servicing the mounting hardware, lubricating the sliders and replacing the pads.
Inner Pad Wear:
If the inside pad is worn more than the outside one, it is likely that the caliper piston is hanging up and not returning to its rest position. This could be caused by damage or corrosion to the caliper or an issue with the master cylinder. To correct, service or replace the caliper hardware, inspect the caliper for damage to the guide pin hole or piston boot, replacing if needed. Check the hydraulic brake system for any residual pressure and replace the pads.
Tapered Pad Wear:
If the friction material is worn in a wedge pattern, horizontally or vertically, it’s a good indication that the pad has not been installed correctly. Worn guide pins and a seized caliper slider on one side of the pad can also cause this. To resolve it, service or replace the caliper hardware, lubricate the sliders and replace the brake pads. This can also happen on dual piston, four piston and six piston calipers where the internal drillings for pressure equalisation are blocked.
Glazed Wear or Cracked Pads:
A grazed or cracked pad with lifted edges will show signs of physical damage and/or thermal distress to the friction material and can signify several problems, usually brought about by excessive heat in the brake system. The most common causes are overuse, improper break-in of new pads, seized calipers, a faulty pad or a parking brake that is not fully retracted. To remedy, simply replace and bed-in the pad and adjust the parking brake if needed.
Overlapping Pad Wear:
This happens when the top edge of the pad overlaps the top of the disc. Common causes include installing the wrong pads or discs onto a vehicle or excessive wear to the guide pins, caliper or caliper bracket.
In addition, the following best practice installation advice is recommended:
- Always bed-in brakes – 30 stops, from zero to 30 mph, with at least 30 seconds between applications is a good rule.
- Thoroughly clean brake discs prior to installation. Any contaminants on their surface will transfer to the pads, reducing their friction coefficient.
- Also ensure that the caliper carrier is clean and that the slider pins are lubricated, free of rust and moving freely.
- Always check the disc for minimum thickness using a micrometre. The maximum allowable thickness variation is around 0.015mm.
- Similarly, use a dial indicator to measure the disc’s runout. 0.05 to 0.10mm is a good maximum runout limit; any more can cause premature and uneven pad wear.
- Replace all pad-to-caliper hardware such as anti-rattle clips, springs and pins, as they gradually lose tension due to high brake heat.
- Never re-use shims. Shims are exposed to significant force on an average application and can lose their elasticity and ability to dampen over time.
- Lubricate all metal-to-metal contact points between the brake pad and caliper using high-performance brake grease. Never coat the friction material, the disc’s surface or rubber parts.
- Always check that the right pads are fitted and that they’re positioned correctly in the caliper to avoid disc contact.
Of course, one of the best ways to prevent excessive wear is by using a pad that is manufactured to the same standards of performance and longevity as an OE part. Delphi Technologies’ brake pads use over 130 different friction elements and feature OE noise-absorbing underlayer technology, chamfers and shims.