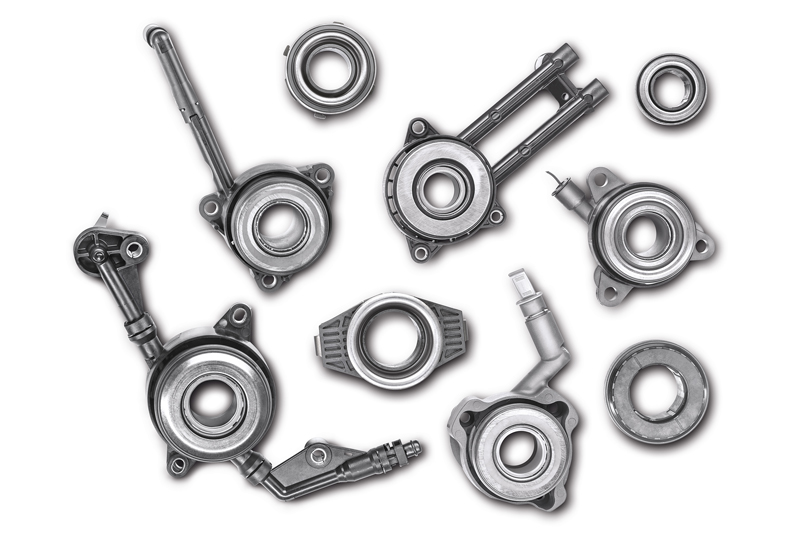
Schaeffler discusses the importance of replacing the Concentric Slave Cylinder when replacing the clutch.
One of the main targets for the modern independent workshop is achieving a ‘first time fix’, as this leads to customer loyalty and an enhanced business reputation. Garages are working hard to do the job once and do the job right, and this has always been Schaeffler’s philosophy too. When Schaeffler supplies a part, it comes with absolutely everything that is required for a professional repair in just one box – a truly complete repair solution.
An example of this is the LuK RepSet Pro clutch kit, which not only contains the clutch assembly but also a perfectly-matched hydraulic Concentric Slave Cylinder (CSC).
A concentric slave cylinder is essentially four clutch components in one: a slave cylinder, pivot/actuation lever, release bearing and guide tube – in a compact, lightweight unit that is more efficient to produce and install. This cost and weight saving is the main reason vehicle manufacturers (VMs) favour incorporating a CSC into the transmission design, instead of an external slave cylinder mechanism.
As the specialists, engineers from both the VMs and Schaeffler know what is ‘best practice’ and would always replace the CSC when replacing the clutch for the following reasons:
■ The guide tube for the seal and bearing can become contaminated, worn or even corroded in extreme conditions, which will damage the rubber seal when the gearbox is removed, with the seal/bearing assembly travelling over this area to reach the relaxed position.
■ It is commonly accepted that the release bearing assembly should always be replaced when replacing the clutch, and as this is an integral part of a CSC, the CSC must be replaced.
■ The rubber seal could become contaminated with old hydraulic brake/clutch fluid, so the system always needs to be flushed and replenished with new fluid to the correct VM specifications and instructions.
■ There are some intricately-designed elements which can be built into a CSC, such as self-centring bearings, peak torque limiters and anti-vibration units – which all enhance clutch operation and need to be in good order to function correctly.
■ CSCs are regularly modified to improve their performance, so by renewing the unit, the vehicle owner can be sure they have the latest and best performing design installed.
If failure of the CSC occurred after a recent repair, not only would clutch operation fail, but the leaking fluid would contaminate the newly-fitted clutch and lead to an expensive rectification bill for the garage. This would involve having to remove the gearbox again to replace it, probably at the garage’s expense and probably resulting in a very disgruntled customer.
A growing problem in the aftermarket is the influx of many cheap, copied parts, usually manufactured from inferior quality materials and not in any way tested to conform to the same VM quality standards as a genuine LuK product. To ensure that technicians don’t get stung by sub-standard parts, Schaeffler supplies exactly the same components to the aftermarket as it does to the world’s leading VMs – many of whom operate a ‘zero defects’ policy.