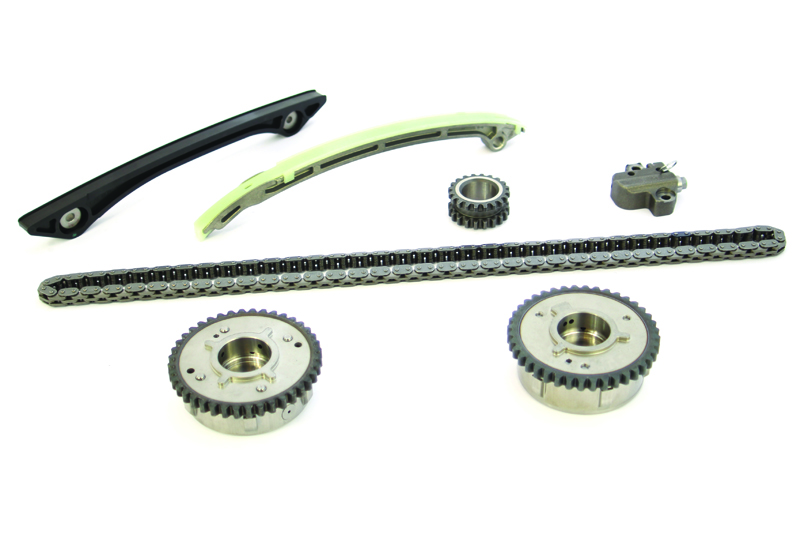
During a vehicle’s service life, one of the major milestones that many owners anticipate is the replacement of the timing belt/chain and the associated components. In this article, BG Automotive goes back to basics, before offering some best practice advice for dealing with this old garage staple.
Timing chain system
The timing chain is the ‘heart of the engine’, and all parts of a timing chain system are subject to wear. The four critical components to control are the guides, tensioner, chain and sprockets. The timing chain is kept under proper tension by the tensioner; the guides are used to keep the timing chain from vibrating; the chain connects the crankshaft to the camshafts; and sprockets transfer the power from the crank to chain to camshafts.
Timing chain
There are three different types of chain – roller, bush and silent. The roller chain consists of inner and outer links. The inner links consist of two inner plates – into which two bushes are pressed – and two rollers that rotate on the bushes. Roller chains are generally fitted to smaller petrol engines.
The bush chain does not contain the rollers that rotate on the bushes. This means the bushes are in direct contact with the sprocket teeth. Better lubrication is required when using this type of chain (poor lubrication is often the main reason they fail). They are generally fitted to more powerful diesel engines.
The silent chain consists of pins, pin link plates and guide link plates. These chains have considerably more inner plates (number is dependent on the application) and are meant to produce less vibration and hence less noise because of the lack of impact with the sprocket teeth. The links are a different shape to the roller and bush chains, so that they can mesh with the teeth in the sprockets with greater ease.
Tensioner
Chain tensioners control the elongation of the timing chain itself. If this is not done then the chain will slacken and run unevenly, which causes extra wear and will result in a snapped chain. An overly tightened chain can also cause problems as it will increase the chain load and wear much more quickly. The use of a chain tensioner that is checked at each service and correctly lubricated will reduce the likelihood of premature chain failure.
There are several different types of tensioner but the most popular is oil fed. Complete with a hydraulic piston that pushes onto the tensioner arm to keep the chain running at its optimum position, this type of tensioner is usually reliable. However, oil contamination can lead to failure, with the tensioner becoming blocked and unable to keep the chain tensioned. A spring-loaded tensioner is more likely to fail when the spring becomes worn or damaged. This can occur when contaminated or ‘dirty’ oil makes its way into the tensioner and starts to wear the spring.
Guide arm
Guide arms are generally made from aluminium, steel, plastic and glass-reinforced plastic. They come in many shapes and sizes, each individual to the application they are fitted to. The guide arm is used to support chains in order to reduce the stress resulting from the chain weight. They also absorb or reduce vibration and are used for noise damping purposes. If a double chain is fitted to an engine then there are always more guide arms fitted in order to support the chain.
A tensioner arm is much more likely to wear than a ‘normal’ guide arm as it is put under much more pressure. As the tensioner plunger moves in and out, the contact point on the arm can wear – normally this happens over a long period of time – i.e. 80,000 miles plus – but it can occur if the contact point is made from an inferior material. It is possible for a guide arm to snap, but this generally occurs because the chain is slack and is ‘slapping’ against the guide.
Best practice – care of the timing chain
When servicing the timing system, it is important that the correct tools are used during fitment. As the majority of timing chain tensioners are hydraulically actuated, they do not require any further specialist tooling other than the tools required to lock the engine in position. While installing a timing belt kit, if a manual tensioner is used, a setting tool may be required to set the belt tension, in addition to a harmonic gauge and locking equipment.
As the timing chain is lubricated by the engine oil, servicing at the correct intervals is especially important to the product’s function and lifecycle. Timing belts are replaced on average at 80,000 miles or after seven years. Timing chains have a similar service mileage when compared to belts, but they do not require replacement after seven years, assuming the vehicle has been serviced regularly and hasn’t reached the manufacturer’s specified service interval. It is important to replace both timing belts and timing chain kits at the correct service intervals to prevent damage to the engine.
Lubrication
Symptoms of poor lubrication in the timing chain system include engine damage, excessive wear/failure of the chain, inconsistent tension due to changing oil volumes, blockage of chain lubrication holes and a high number of contaminants contained in the oil during an oil change.
During every major service, BGA recommends that technicians inspect cam bearings for signs of wear or scoring. Such symptoms indicate poor lubrication, so the technician should ensure oil feed holes on the gasket (if fitted) are clear of contaminants; check that the guides, tensioner and feed pipe (if fitted) are not blocked; and the oil control valve should be checked to see if it is blocked. If it is, ensure that is it cleaned and the electrical connections aren’t damaged.
Oil control valves
Replacement of the oil pump is recommended whilst changing the timing chain kit. An engine flush is recommended, and you should also ensure that an adequate oil level is maintained at all times. If the oil control valve is damaged, BGA has a solution in place.
Oil control valvees are fully functional valve timing solenoids that control the flow of oil to the VVT system as it is engaged. Oil control valves activate when there is a significant load against the engine – for example, while a vehicle is carrying additional weight, traveling up hills or when acceleration is expedited through throttle control. When the control valve activates, oil is sent to lubricate the variable valve timing chain and gear assembly. If the control valve fails or is blocked, the lack of proper lubrication can cause the chain and gear to prematurely wear or break entirely. Symptoms of a failing/poor control valve include the engine light coming on, dirty engine oil, rough engine idle, and a decrease in fuel economy.
As an engine parts specialist with over 15 years’ experience, BGA is now able to offer the aftermarket a complete range of oil control valves. The addition of this product complements the company’s timing chain and timing belt ranges, meaning it is now able to offer a complete package, from VVT to control valve to timing belt and chain. With over 100 part numbers in range, BGA says it is offering garages the opportunity to source from their local factor rather than the dealer.