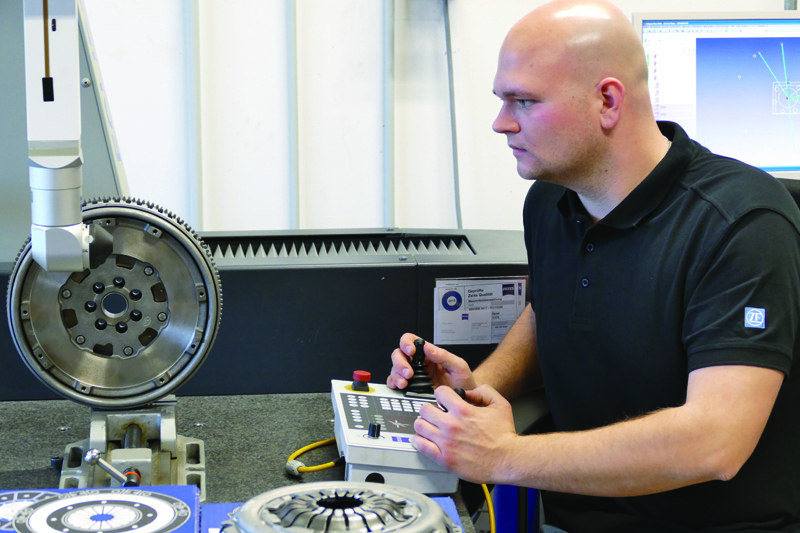
Clutches in passenger cars are subjected to a wide variety of demands every day – from hill starts and traffic jams to winding roads. Ian Gaskell, Product Support Technician at ZF Aftermarket, outlines the common causes and issues associated with clutch failure and the simple steps technicians can take to prevent clutch warranty returns.
Many aspects of driving can put added stress on components. Even so, the typical lifespan of a clutch can be 75,000 miles or more when maintained correctly. When replacement is needed, workshops should use Original Equipment (OE) recommended parts which provide the reassurance that the components have met the vehicle manufacturer’s exacting specifications for fit and performance.
If an OE specified replacement clutch is installed, further work should not be required. Occasionally, some drivers do experience problems with a newly-replaced clutch and after the customer has revisited the workshop, the technician may believe there to be an issue with the part itself and return it under warranty. However, the majority of warranty claims can, in fact, be attributed to the quality of installation rather than a faulty part. For instance, clutch problems could be caused by errors such as misalignment of the gearbox fitting or incorrect lubrication and distortion of the clutch cover.
Identifying the issue
While erroneous warranty returns can often be explained by incorrect installation practices, continuing vehicle issues following clutch or dual mass flywheel (DMF) replacement may also be down to mechanical or electronic system faults. For this reason, it’s important to conduct a thorough inspection before replacement to avoid unnecessary costs and returns to the workshop. When diagnosing malfunctions or damage in clutch systems, a systematic approach should be taken to ensure the correct causes are identified and an appropriate repair is considered.
There are a number of key wear problems which may cause a clutch to malfunction or fail. For example, clutch slip can arise through: an incorrectly installed cover assembly; a lubricant contaminated clutch disc; incorrectly re-machined flywheels; or installation of the wrong clutch for the application. This can result in the clutch cover overheating, causing accelerated rates of clutch friction lining wear.
Incorrect installation
Disengagement problems are often cited as a reason for warranty returns, with issues manifesting themselves through the distortion of the clutch cover housing. A key consideration when installing a new clutch is to ensure the clutch disc is precisely centred even before it is pressed on by the clutch pressure plate. An alignment tool can help ensure the clutch disc is perfectly lined up and minimises the risk of deforming the hub spline in the process, but make sure all installation brackets and transport securing devices are removed after installation. As the tolerance between the transmission input shaft and hub spline is only a few hundredths of a millimetre, the slightest deformation during insertion of the transmission input shaft reduces the mobility that is required for later declutching.
Gearbox misalignment
When installing a replacement gearbox, the input shaft should be precisely aligned on the same axis as the engine crankshaft. Any misalignment of the gearbox can cause the clutch to be pulled out of line or damaged, reducing service life. In order to prevent or correct misalignment, all mating surfaces should be clean and clear of debris. Additionally, route pipes should be clear of the crankcase to the gearbox joint as a trapped earth strap or cable tie can also cause issues. The condition of the pilot bearing in the flywheel and gearbox input shaft guide sleeves can impair shaft location and cause offset too.
Lubrication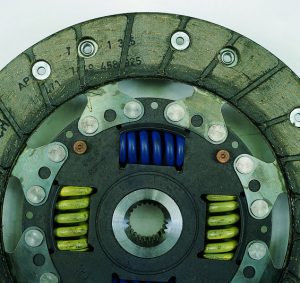
To ensure easy release of the clutch, the clutch splines must be lubricated to ensure rust doesn’t form. In comparison, using the wrong grease or too much product may cause the clutch to slip. The function of the clutch and its shifting characteristics can be further enhanced if speciality grease is coated on the hub splines with a brush or toothbrush. Any excess spline grease should then be wiped from the disc prior to installation.
Friction lining contamination can also occur, leading to premature clutch wear. When the gearbox is removed, it is quite straightforward to inspect the crankshaft rear oil seal, gearbox input shaft seal, and clutch hydraulic system, for oil or fluid leaks and correcting any problems identified. Cleaning the bellhousing thoroughly, removing any debris will also protect the clutch.
ZF clutch kits
Whether the damage is within the clutch itself or the Dual-Mass Flywheel (DMF), it’s always recommended to replace the entire clutch kit. By replacing the vehicle clutch and DMF in the same operation, workshops can improve throughput but also deliver financial savings to the end customer in terms of labour and future downtime.
To help simplify decision making for customers, ZF Aftermarket has applied its long experience of supplying the aftermarket with clutches and DMFs, and developed a complete kit for renewing the components on a range of vehicles. The SACHS clutch kit range contains the clutch cover, clutch drive plate and DMF, together with new fixing screws and assembly grease.