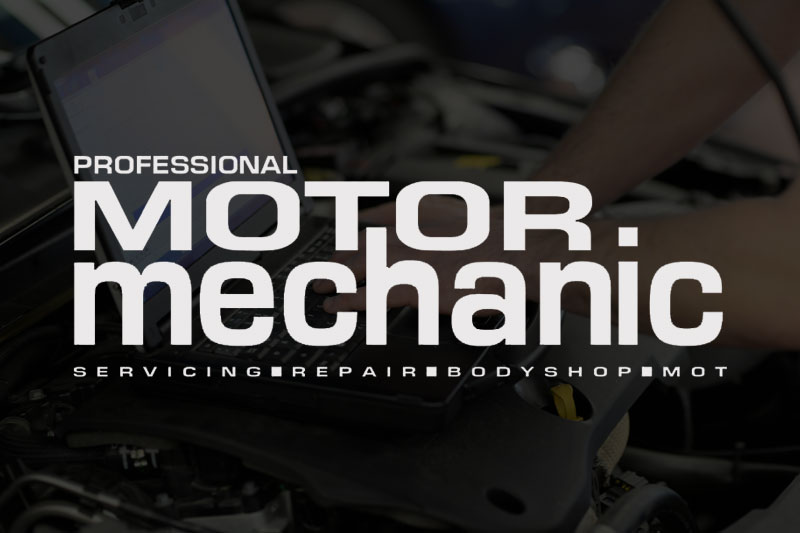
The lifeblood of all A/C systems is its compressor oil as using the correct oil is critical not only to lubricate internal compressor components but, on some vehicles, to prevent electrical damage to a compressor. Compressor oil also acts as a sealing agent for rubber components such as hoses and seals so the oil used in the A/C system must be compatible with all of the materials in the system.
Three types of compressor oils are currently used in automotive A/C systems:
1. Polyalkylene glycol (PAG) oil
2. Mineral oil
3. Polyolester (ester) oil
Polyalkylene Glycol (PAG) oil
PAG oil is a man-made lubricant that is used in R134a and R-1234yf A/C systems, although the two types of PAG oil are different. There are several viscosities of PAG oil used by vehicle and compressor manufacturers and using the wrong viscosity oil in a compressor may create abnormal compressor noise and possible premature internal component wear.
By its chemical structure PAG oil is hygroscopic, meaning it attracts and retains moisture which can come from the atmosphere or from the A/C system. PAG oil and moisture together are not a good combination as when they mix, it forms an acid, causing damage or failure to system related components.
This type of oil should never be used to lubricate O-rings, compressor shaft seals or refrigerant line joints as in time corrosion can set in, which may cause a refrigerant leak. If the corrosion becomes severe enough, joints and fittings can fuse together and may not be removable during a future service repair.
There are some guidelines to follow when using PAG oil to keep it as moisture-free as possible:
- When repairing an A/C system where refrigerant components are being removed, immediately seal off component fittings to minimise atmospheric moisture from entering a component or the system.
- When installing replacement parts, keep caps on the part, except when you’re performing an oil balance or are ready to install the part. This too will minimise exposure of the PAG oil to atmospheric moisture.
- The moisture absorption rate of PAG oil can occur at a rapid pace. If a container of PAG oil was left open overnight, it must not be used as it will have absorbed too much moisture to be effective in an A/C system.
- To keep moisture to a minimum, always reseal the container immediately after dispensing PAG lubricant from it. If it is not known whether a container of PAG lubricant has not been properly resealed, do not use it.
- Pull a vacuum on the refrigerant system after it has been repaired. Follow proper refrigerant recovery and recharging procedures, which typically includes a minimum vacuum of 45 minutes, to remove any moisture that has entered the A/C system during its repair.
Mineral oil
Mineral oil is natural oil and is not hygroscopic, making it different to PAG. In automobile A/C systems, mineral oil is used in those systems that utilise R-12 refrigerant and is also used to lubricate O-rings and seals on both R-12 and R134a systems. Mineral oil does not require special care during storage and handling, but it is good practice to keep its container sealed when not in use to prevent dirt and other forms of contamination from getting into the oil.
Polyolester (Ester) oil
Polyolester or ester oil is also used in automobile A/C systems and until the advent of hybrid vehicles with electric compressors, the use of ester oil was promoted by some A/C compressor remanufacturers for use in servicing systems with R-134a refrigerant.
Ester oil can alter the dimensions of O-ring material and it also has some limitations. Unlike PAG and mineral oil, ester oil does not perform well in high heat load conditions.
New compressor manufacturers and VMs do not endorse the use of ester oil in A/C systems, with one exception – hybrid electric vehicles with electric compressors. Ester oil has greater insulating properties than PAG oil and that is why it is the only oil recommended by VMs during service of hybrid vehicle A/C systems, which use electric compressors. The windings on the air conditioning compressor are immersed in compressor oil and ester oil is used to protect the insulation on the windings to prevent electrical leakage.
Example of failed compressor due to lack of pre-oiling
Oil balancing of A/C compressors
When installing a new service compressor on a vehicle it is important to make sure the compressor is oil balanced correctly with the correct type and amount of lubricant. The purpose of oil balancing is to make sure the amount of oil in the A/C system remains at the correct level. The first thing to consider when performing the process is the amount of oil contained in the replacement compressor. This can vary from a full charge of oil (236 ml), to a half charge of oil or no oil at all. If oil is contained in the replacement compressor it will have to be removed and reinstalled in the correct amount to properly balance the system.
When performing a compressor oil balance, always follow the instructions provided with the compressor or in the vehicle service manual to know how much oil to add to the compressor prior to vehicle installation.
Most times oil balancing involves draining and measuring the oil from the failed compressor, followed by adding a specific volume of new oil to the replacement compressor. The amount of oil to be added to the compressor is specified by the compressor manufacturer. In addition to this you need to use the viscosity of oil recommended by the compressor manufacturer. If the compressor requires heavier weight oil, such as PAG 150, but PAG 46, which is a lighter weight, is used, the result could be noisy compressor operation and premature wear.
Servicing tip
After adding the oil to the compressor, a good service tip is to rotate the compressor clutch at least four turns prior to compressor installation. This serves two purposes: rotating the clutch circulates oil through the compressor, which reduces the potential of compressor damage due to dry bearings and it reduces initial torque when the clutch is first engaged. By design, some compressors have a high initial torque. If the torque is high when the compressor is engaged, the torque that is created could cause the compressor drive belt to snap or cause the engine to stall.
Rotating the compressor clutch is usually done by hand or with a spanner wrench. Another option to the spanner wrench is the compressor turning tool. On direct drive compressors, the pulley and clutch are one in the same. The turning tool performs the same function as the spanner wrench, but it is installed on the threaded hub of the clutch. After the turning tool is installed, use a wrench to turn the tool and clutch.
Delphi product range
The product can be used on some clutches that can’t accept a spanner wrench because of clutch design, or where a solid grip by the spanner wrench cannot be achieved. It can also be used in place of the spanner wrench, providing an easier method of clutch rotation, and can be utilised off or on the vehicle. Never use a socket on the shaft nut or bolt to rotate the clutch as doing so may affect the air gap between the clutch driver and compressor pulley, resulting in compressor issues.