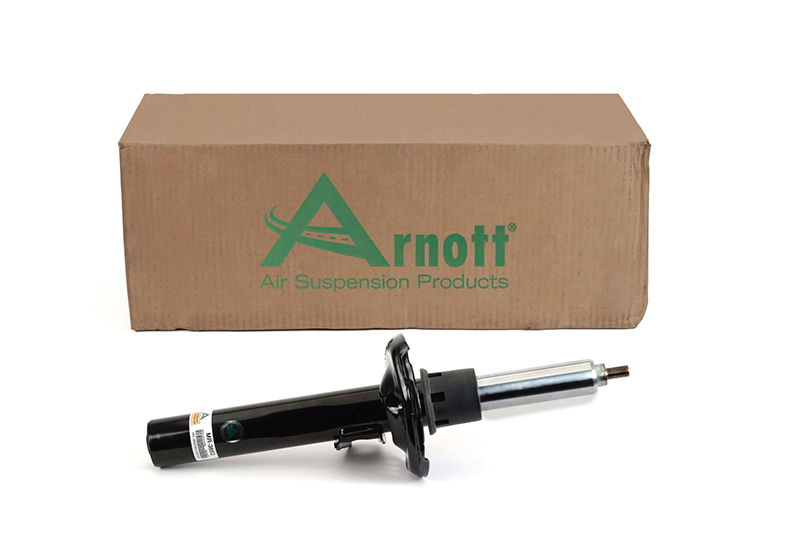
Arnott Europe takes a deeper look at magnetic ride systems, which provide damping for shock absorbers to ensure a smooth ride for drivers.
Automotive magnetic ride systems are quite unique compared to any other electronically controlled adjustable damper systems. Controlled damper systems typically consist of a continuously variable damper, an ECU, and a sensor set. Although these systems all function in a similar manner, the working principle of a magnetic ride damper is very different.
Most adjustable dampers are based upon conventional hydraulic monotube or twin tube dampers. These adjustable dampers are filled with hydraulic oil and use conventional shock valves along with electrohydraulic proportional flow control valves. This permits a wide range of damping force adjustment from very soft to extremely stiff. Magnetic ride dampers look like a conventional hydraulic-based monotube damper from the outside but are completely different internally. They also contain a simple electromagnet assembly and a special liquid known as magnetorheological, or MR, fluid.
Characteristics of MR fluid
The term “magnetorheological” refers to a fluid that experiences a change in its properties when exposed to a magnetic field. The MR fluid used in magnetic ride dampers consists of a base oil, microscopic iron particles, and several other ingredients that hold the iron in suspension. When this fluid is magnetised, it changes from a liquid to a putty-like substance.
Magnetic ride dampers use this unique property of MR fluid to adjust the damping forces. The electromagnet assembly has passages to allow fluid flow past the magnet core as the shock is compressed and extended. The fluid flows easily through the magnet assembly when it is not energised. When electrical current is applied, the magnet energises and creates a magnetic attraction between the iron particles in the fluid. This thickens the fluid into a putty-like state and increases its resistance to flow. The increased resistance to flow results in increased damping force. Also, the intensity of the thickening effect increases as additional current is applied to the magnet. As a result, the damping force can be adjusted to any level desired simply by changing the amount of current applied to the magnet. Unlike a conventional valve-based damper, no valves or additional moving parts are needed to make damping force adjustments. This offers several advantages, including better damping force consistency, reduced internal complexity, no wear of internal moving parts over time, and reduced noise.
One major feature of magnetic ride dampers is the ability to adjust extremely quickly under all conditions. Since damping force adjustments are controlled by magnetising the fluid, force adjustments can be made immediately without any delays due to opening and closing of valves. Also, it is important to note that the force adjustment speed is independent of the fluid flow speed. This characteristic is unique to MR dampers. Valve-based adjustable dampers can also adjust very quickly, but the adjustment speed is dependent on both the configuration of the damper valves and the amount of fluid flowing through the valves. As a result, magnetic ride systems are particularly good at controlling body and wheel motions caused by larger road disturbances.
Potential issues
Magnetic ride offers several advantages compared to conventional valve-based systems, but it also has some disadvantages. Most of the disadvantages are related to the MR fluid itself. The fluid is very expensive due to its complexity. In addition, MR fluid is rather abrasive due to the presence of iron particles in the fluid. This requires the use of costly premium surface coatings on internal damper components. MR fluid also requires elaborate sealing systems that add additional expense.
The abrasive nature of the MR fluid can also have a negative effect on the ride. As a result, magnetic ride dampers tend to have slightly higher levels of internal friction compared to conventional adjustable dampers. The higher friction levels can result in a slight increase in ride harshness on smooth surfaces. The potential for ride harshness was amplified in early MR damper designs by the possibility of residual magnetism in the fluid. However, both issues have largely been resolved by design improvements over time. Finally, magnetic ride dampers can be more prone to base oil leakage because of the abrasive nature of the fluid. Loss of base oil makes the remaining fluid much thicker resulting in a stiffer and harsher ride.
Magnetic ride has now been in production for over 20 years. Continuous improvements to the design have kept it competitive in the growing market for electronically adjustable suspension systems.
Arnott’s products are produced with OE components offering exact form, fit and function. Each product is extensively tested in its American and European facilities and custom-tuned to suit the specific vehicle make and model before being produced.