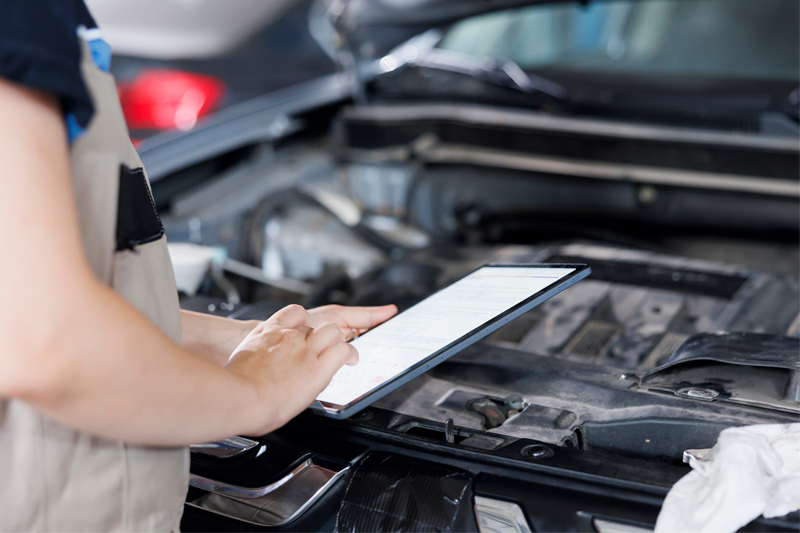
Welcome to the thirteenth instalment of our workshop guide to Bosch’s KTS diagnostics software, ESI[tronic] 2.0. In this instalment, we’re looking at hybrid and electric vehicle capabilities.
In the last instalment we looked at ADAS systems and how the ESI[tronic] 2.0 enables calibration of these across a wide range of vehicles. This time we will look at how ESI[tronic] can also help futureproof your workshop, by enabling you to work safely and efficiently with the hybrid and electric vehicles that are becoming increasingly common on our roads.
ESI[tronic] 2.0 already helps technicians carry out maintenance, service and repair work on a wide range of vehicles equipped with internal combustion engines quickly and efficiently. What you may not know is that it also comes fully equipped with the software needed to carry out the same diagnostic procedures on electric and hybrid vehicles. This makes the move to electric more of a step than a massive leap, as 80 per cent of these vehicles remain exactly the same as those with an internal combustion engine (to be verified). The software required is included as standard – there are no costly extras or plug-ins – just the tools you need to do the job.
There are two features of ESI[tronic] 2.0 that are important for working on hybrid and electric vehicles.
- It lets you easily check a high-voltage (HV) battery’s state of health (SOH).As with every vehicle, electrical vehicles are subject to wear and tear over time, particularly when it comes to the battery, which will lose its overall capacity over time – as much as 2 per cent a year. If customers want to sell or buy a car, or prepare for long journeys or holidays, a regular battery check is essential.
The special functional test in ESI[tronic] 2.0 diagnoses the condition of the highvoltage battery when supported by the vehicle. By investing in ESI[tronic] you will get detailed information of exactly what can and cannot be done to the battery on each vehicle.
After choosing the diagnosing state option (Fig.1), users can check the charge status, as well as the overall state of health (SOH) of the HV battery (Fig.2).
The user can then progress to a visual representation of the HV battery state, including charge status, minimum and maximum cell voltage and the SOH (Fig.3).
The bar graph’s colour changes to red if the battery’s condition is out of tolerance. If this is the case, the software can carry out tests to evaluate the issue cell by cell, identifying the affected cells in the battery pack.
Once the functional test is complete, the user can save and document the results – vital to use as proof of the battery in discussions with the owner.
- High-voltage battery cut-off instructions.As a technician, you will require information on how to work safely on electric and hybrid cars, particularly when it comes to cutting off the power of high-voltage batteries. The cut-off power instructions differ for each type of vehicle – and ESI[tronic] 2.0 contains in-depth guidance on how to execute this process on a wide range of vehicle makes and models, with more in the pipeline (Fig.4).
This is a fundamental requirement when servicing hybrid or electric vehicles, as there otherwise is a risk of coming into contact with a high voltage when carrying out certain procedures. It is essential to turn off the supply, so you can ensure there is no risk to health.
Disclaimer – the following steps are purely an example and not to be followed. Connect your ESI[tronic] 2.0 to get the precise steps for each vehicle make and model, and to ensure your safety.
Step 1
Disconnect the 12V battery so that it’s not connected to the high voltage battery and system.
Step 2
Once you have put on appropriate PPE and cordoned off the area around which you are working, lift the service plug from the high-voltage battery.
This divides the battery into two halves and removes the fuse from the plug disconnecting the voltage supply from the HV battery.
Step 3
Take a tea break! Wait at least five minutes to let the electrons in the capacitors discharge.
Step 4
Once the five minutes are up, you can undo the cover of the inverter. It’s important to note that you must use appropriate high-voltage insulated tools when carrying out this work.
Step 5
Finally, you need to check that there is absolutely no high voltage coming from the battery pack. Use a suitable measurement tool such as the Bosch FSA 050, check that the voltage has drained from the capacitor (Fig.5).
Now the car is safe to work on
These instructions work hand in hand with our complete suite of hybrid and electric vehicle training courses. The courses are designed to suit all needs and requirements, ranging from essential EV knowledge and awareness – that enable you to carry out service and repair tacks that are not connected to the high voltage parts of the vehicle – to fully qualified ‘expert’ technician.
Alongside this training, ESI[tronic] 2.0 is an essential pillar to help you work confidently and safely with hybrid and electric vehicles (Fig.6). A slip up with a fuel vehicle may give you dirty fingers, but you need to make sure you are 100 per cent safe when working on the components of an electric or hybrid car – and only a properly executed disconnect can ensure this.
Futureproof your workshop
As more hybrid and electric cars enter the market and appear on the forecourts, more customers will need support with their vehicles. Workshops that are able to cater for this need will be in a good position to deal with rising demand across the marketplace.
You only need one trained person in your workshop and ESI[tronic] 2.0 to bridge this gap. Your ESI[tronic] 2.0 contains the components you need to work on hybrid and electric vehicles as standard – no extra software expenditure or add-ons required.
The ESI[tronic] online diagnostic software is ready for you when you want to make the move into EV and hybrid work.
Stay tuned for the final instalment of this series where we will learn how the connected workshop will help your business thrive in the future.