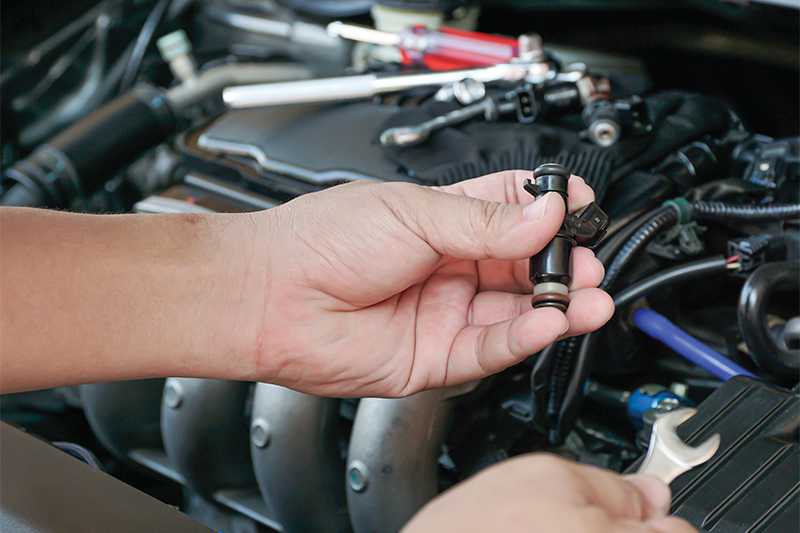
We asked PMM product tester and diagnostics expert Tony Powell to share some of the techniques and knowledge he’s picked up along a career diagnosing vehicle faults stretching over four decades.
When I first started learning to diagnose things over 40 years ago, there was very little in the way of training outside of college, plus it wasn’t called diagnostics back then!
We learnt stuff the hard way: by making mistakes and getting burnt (literally). I remember being told as a young apprentice to put a 1/4 in. bolt into a fuse holder (the old glass type) and then having to pull it out fast when the wire started to smoke where it was shorting out, this is the getting burnt bit as the bolt was very hot and no one told me to use pliers. These days everyone has a scanner that you just plug in and it tells you what’s wrong – or so some customers think anyway.
The modern world of diagnostics has changed dramatically and at a fast pace in recent years, with new tools appearing every day. However, you don’t always need to spend thousands of pounds on tools to be effective at diagnostics.
The biggest and best tool we all have is our brain, working in conjunction with our sight, touch, hearing and even our smell; used in the right way these can be very effective and they’re completely free.
Over the years I have learnt that you never stop learning and every day is a school day.
There are many opinions on how to diagnose a fault but I always start with the basics, for example checking for blocked air intakes. I know of one garage that fitted a new set of injectors, a turbo and a fuel pump – when the fault was found, it turned out to be an old crisp packet that was flapping up and cutting the air off at 35 mph. It was an expensive mistake with a simple cause and an even simpler fix.
Start by looking at things first, you are looking for something that doesn’t fit: green fur on copper wires, broken wires that stick out, loose bolts or nuts, burn marks or rubbing marks from loose parts are always a giveaway. Can you smell fuel or anti-freeze? Do you hear a funny noise? If there’s nothing obvious, move on – although experience can play a big part here, we can all be led down the wrong path. Be careful, because touching can alter things and that fault may disappear for a while.
A code scan can give you a guide as to where to go first, but remember just because it says “X” it doesn’t mean that “X” should be replaced, it could be power or earth or signal fault to or from “X”, not just the part and a solid, structured diagnostic plan is the way to go.
Take a recent “no start, no communication with the ECU” job I did. A code scan said no communication and a low battery fault along with many fault codes for CAN Bus and communication across the vehicle. Just to make things weird, the wipers were permanently running.
I started by putting a decent battery support unit on as there is no point in chasing a low power fault when the battery is flat. The giveaway here was that I still had the low power fault after doing this. Returning to the battery to check my support unit was on ok I noticed the odd one out, the bolt holding the positive lead onto the distribution module was very, very rusty. When I did a few preliminary voltage drop tests the readings I got were nicely over 12 V as they should have been, with no drop off. But using a test light gave me more information as the voltage disappeared. Further investigation showed that the fuses were badly corroded and one even looked fine yet disintegrated when I touched it (this just happened to be the one that fed power to the ECU). This explained the non- communication code and the no start along with the low voltage code. A new module and fuses fixed all the issues here.
Using a decent test lamp that draws a small current can show up a wire that although it allows 12 V along it or it passes a resistance test can soon fail when it is tested under load. Don’t rely on an LED test light for this job!
The same applies when checking fuses they may look ok but using a test lamp puts them under load which shows up the invisible crack or break that a voltmeter may miss.
Voltage drop testing is also a very effective method for tracing faults and is a skill you really need to master. So far, we have only scratched the surface but it’s easy to see that basic tools can still do the job.
As you progress through the years in this trade, you end up with more and more tools and getting off that tool van empty handed, especially in my case, becomes harder and harder – it’s sad to say but Covid saved me a fortune!
Scan tools
Some tools, though, are worth their weight in gold – take the Picoscope oscilloscope, for example. If you can master this tool you can fix some incredibly difficult faults with ease, getting into wiggly lines on a screen can show up some of the most awkward and difficult faults to diagnose in the most easy-to-see way. I for one wouldn’t be without mine. There is a lot of training and back up for this one as well.
Scan tools come in two categories: dealer and aftermarket. Whilst the dealer tool can be brilliant it can also be hard to master and very costly to buy and maintain with minimal back up or support outside the facebook groups that have sprung up.
Aftermarket scan tools are usually cheaper and normally easier to use but often miss some important job options found on the dealer tools or only provide half the details required and many use the same software re-branded.
Yet without these tools many of us wouldn’t be able to perform to the levels we do.